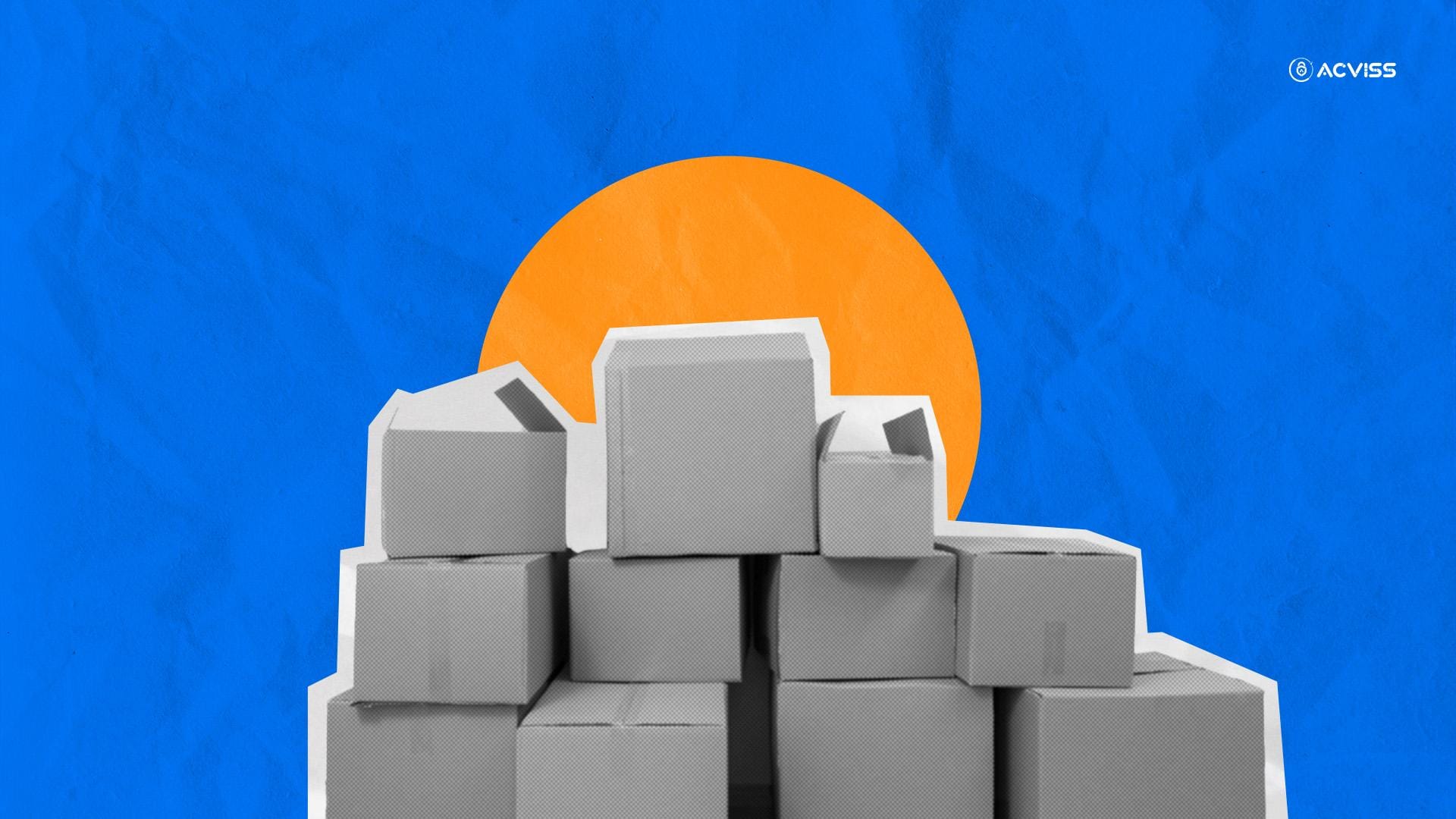
Manufacturing has long been driven by the pursuit of efficiency and profitability. However, in the race to scale production and meet fluctuating consumer demand, companies often fall into the trap of overproduction, producing more than the market requires. This miscalculation, whether due to inaccurate forecasting, competitive pressure, or outdated production models, can have severe consequences, including financial losses, environmental degradation, and supply chain inefficiencies. When sustainability is not just a choice but a necessity, manufacturers must shift from a "produce more" mindset to a precision-driven approach, optimising resources while reducing waste.
Understanding the Overproduction Trap
Overproduction occurs when goods are produced more than the actual market demand, leading to surplus inventory. This phenomenon is one of the most critical wastes in the Lean Manufacturing philosophy, recognised as "Muda" in the Toyota Production System. It often stems from outdated forecasting methods, inefficient supply chains, and an ingrained mindset that more production equates to higher profits.
The Costs of Overproduction
- Environmental Impact: Excess production depletes raw materials, increases energy consumption, and contributes to landfill waste and pollution.
- Financial Losses: Companies incur costs in production, storage, and eventual discounting or disposal of surplus goods.
- Supply Chain Inefficiencies: Overstocking leads to logistical challenges, increasing warehouse costs and reducing flexibility.
- Market Saturation: Flooding the market with excess products can lead to price drops and brand devaluation.
Avoiding overproduction is not just about sustainability; it is about smart business. Companies that master lean and agile manufacturing will gain a competitive edge in an era that values efficiency and environmental responsibility.
Strategies for Avoiding Overproduction
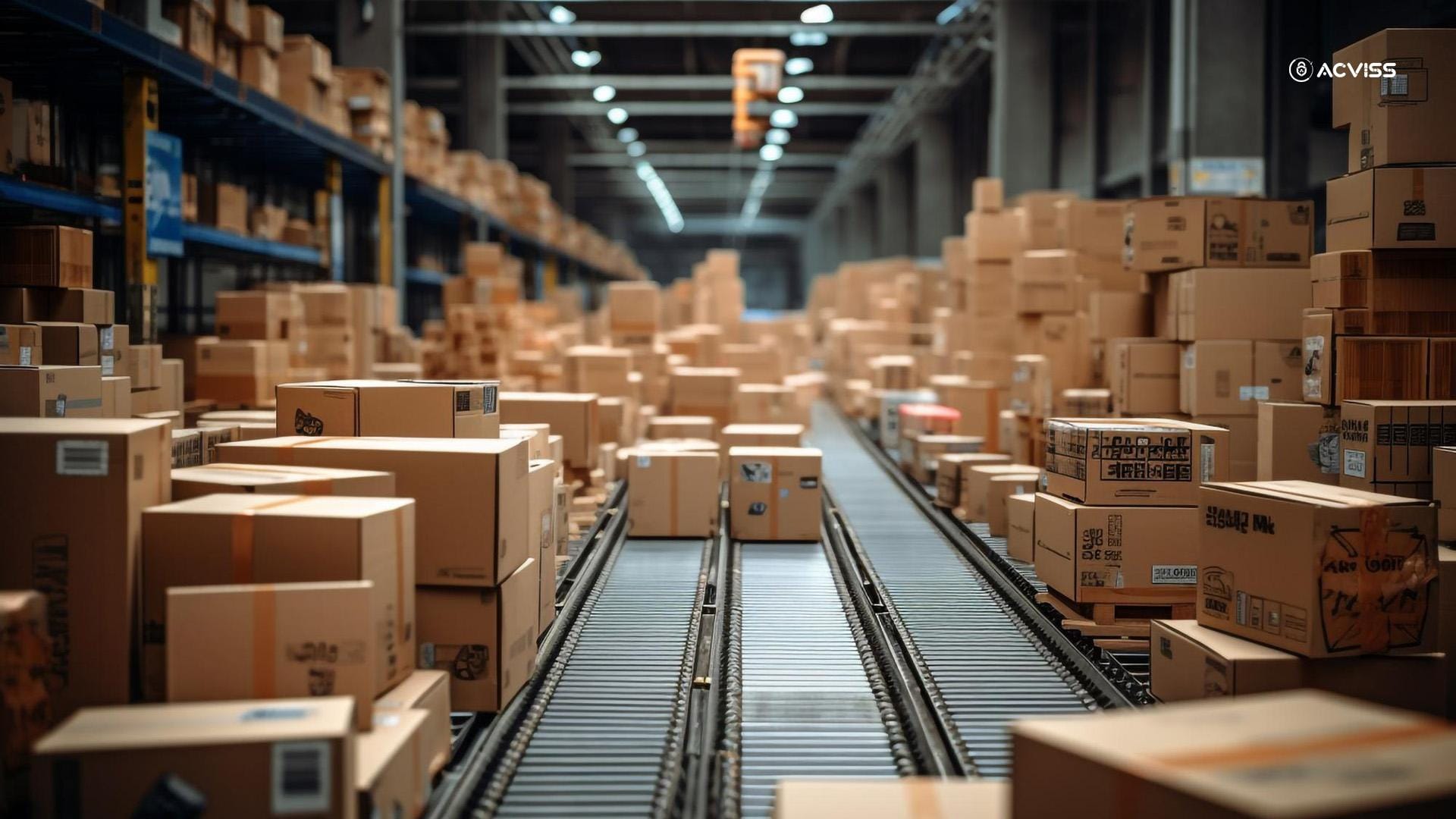
1. Adopt Lean Manufacturing Principles
Lean manufacturing focuses on reducing waste and improving efficiency by producing only what is needed when it is needed. Companies like Toyota have successfully implemented Just-in-Time (JIT) production, where materials and goods are produced precisely when required, minimising inventory and excess.
Key Lean Strategies:
- Implement JIT systems to align production with real-time demand.
- Use Kanban systems to control production flows.
- Conduct regular value stream mapping to identify inefficiencies.
2. Enhance Demand Forecasting with AI and Big Data
Traditional forecasting methods often rely on historical sales data, which may not accurately predict future trends. AI and big data analytics provide real-time insights into consumer behaviour, helping companies adjust production schedules dynamically.
Tools for Smarter Forecasting:
- Predictive Analytics: AI-driven demand forecasting tools help adjust production in response to changing market trends.
- Digital Twins: Simulating manufacturing processes digitally can help predict production needs more accurately.
- IoT-Enabled Smart Manufacturing: Internet of Things (IoT) sensors can monitor supply chain fluctuations, improving responsiveness.
3. Implement Agile Manufacturing
Agile manufacturing enables companies to quickly adjust production in response to market demands, reducing excess output and improving resource efficiency.
Key Agile Practices:
- Modular production lines that can shift between different product types.
- Flexible workforce training to adapt to production shifts.
- Small-batch production cycles to prevent overstocking.
4. Embrace Circular Economy Principles
A circular economy approach aims to design out waste and keep resources in use for as long as possible. This means producing goods that can be easily recycled, repaired, or repurposed rather than discarded.
Steps to Circular Manufacturing:
- Use recycled or biodegradable materials in production.
- Design products for easy disassembly and reuse.
- Establish take-back programmes to recover and refurbish products.
5. Strengthen Supplier and Retailer Collaboration
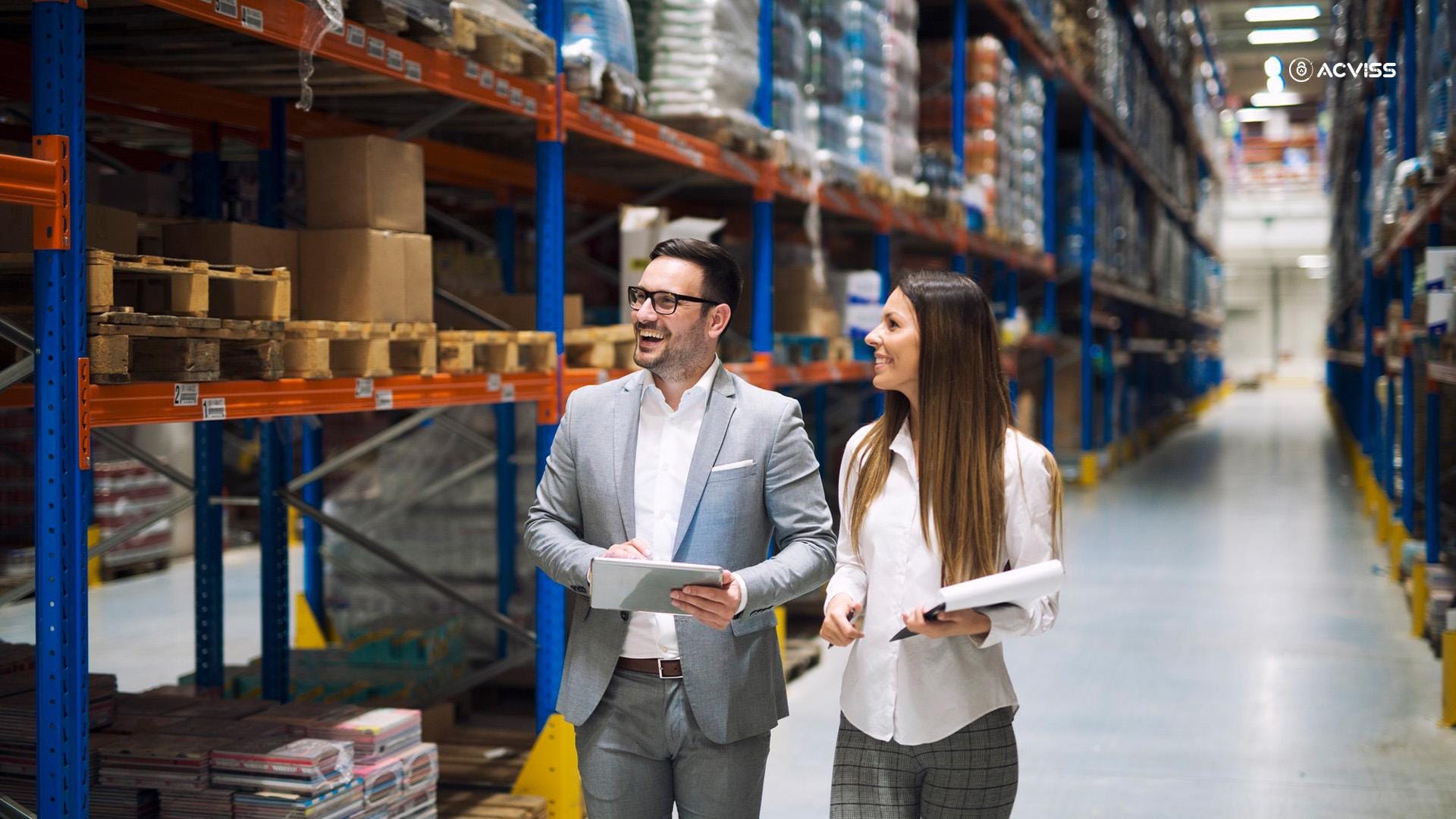
Better coordination with suppliers and retailers can help align production with actual demand, reducing unnecessary manufacturing.
Collaboration Tactics:
- Implement Vendor-Managed Inventory (VMI) systems where suppliers monitor and restock inventory based on real-time demand.
- Use blockchain technology for transparent, data-driven supply chain management.
- Build stronger retailer partnerships for better sales insights and coordinated production planning.
6. Adopt Sustainable Production Technologies
Investing in green manufacturing technologies not only prevents waste but also improves energy efficiency and reduces the carbon footprint.
Sustainable Tech Innovations:
- 3D Printing: Allows for on-demand production, reducing overstock and waste.
- AI-Optimised Manufacturing: AI-driven process optimisation reduces errors and unnecessary production.
- Renewable Energy Integration: Powering factories with solar, wind, or hydro energy reduces dependency on fossil fuels.
7. Empower Consumer-Centric Customisation
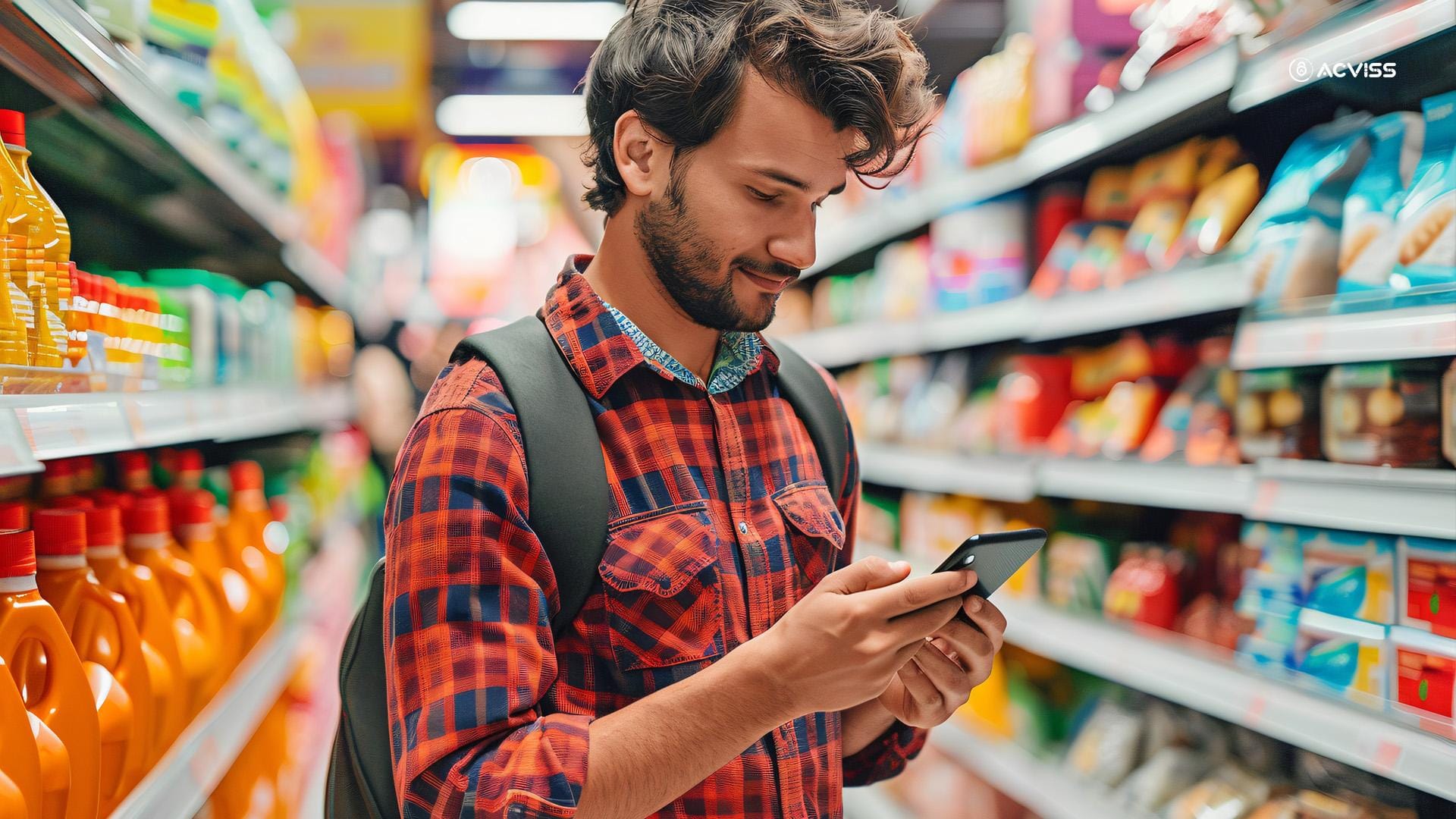
Customisation reduces overproduction by producing only what customers need rather than mass-producing unsold goods. The rise of on-demand manufacturing in industries like fashion and electronics has significantly minimised excess production.
Customisation in Practice:
- Direct-to-consumer (DTC) models, where customers pre-order products.
- Mass customisation using modular product design.
- AI-driven configurators that allow buyers to personalise items before production.
8. Optimising Manufacturing with Acviss Origin Traceability
Acviss’s Origin Traceability solution enhances supply chain transparency, enabling manufacturers to minimise waste and optimise production processes. By leveraging blockchain technology, Origin provides real-time tracking and tracing of raw materials and finished products, reducing inefficiencies that lead to overproduction.
How Origin Helps:
- Real-Time Visibility: Tracks materials and inventory in real time, preventing overstocking and reducing resource wastage.
- Demand-Driven Production: Ensures manufacturers only produce what is necessary by providing accurate supply chain data.
- Fraud Prevention: Protects against counterfeit products, ensuring genuine products reach the market while reducing losses.
- Regulatory Compliance: Helps manufacturers adhere to avoid penalties and inefficiencies.
By integrating Acviss Origin, manufacturers can streamline operations, enhance sustainability, and create a leaner, more responsive supply chain.
Case Studies: Companies Leading the Way
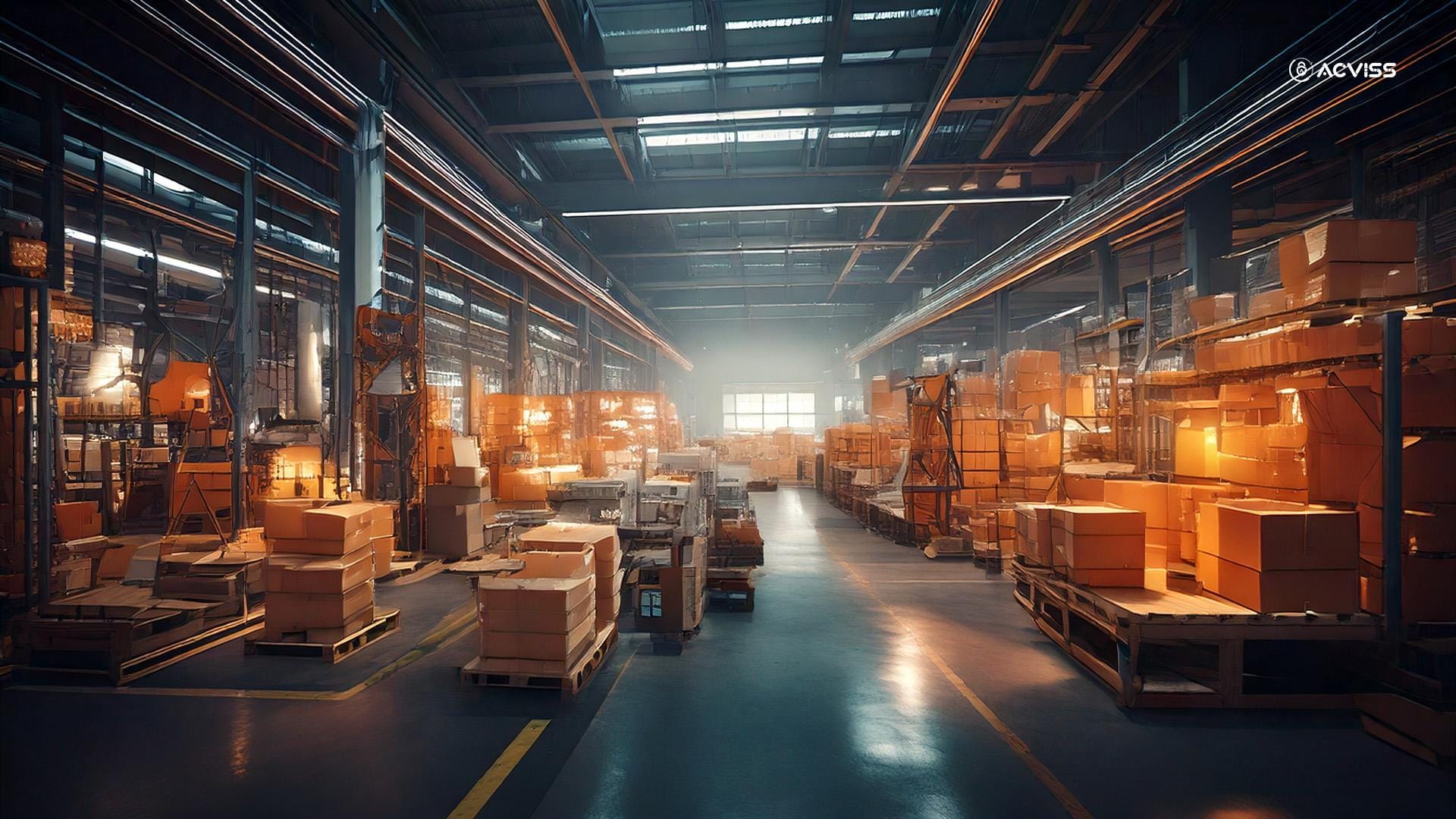
1. Patagonia: Lean and Ethical Manufacturing
Outdoor clothing brand Patagonia focuses on sustainable production, minimising waste and ensuring its supply chain aligns with environmental goals. Their Worn Wear programme encourages customers to repair, reuse, and recycle products rather than discard them.
2. Tesla: On-Demand Manufacturing for Electric Vehicles
Tesla builds cars to order, reducing the risks associated with overproduction. Keeping production flexible and aligned with real-time demand, Tesla minimises inventory waste and improves cash flow efficiency.
3. Unilever: AI-Driven Demand Forecasting
Consumer goods giant Unilever uses AI and big data analytics to forecast demand and optimise production. Their smart supply chain reduces unnecessary manufacturing, lowering waste and carbon emissions.
Conclusion
The battle against overproduction is a critical one, not just for environmental sustainability but for economic efficiency. Manufacturers that embrace lean, agile, and circular strategies will emerge as leaders in an increasingly resource-conscious world. Through intelligent forecasting, technological innovation, and responsible supply chain management, businesses can navigate the delicate balance of meeting demand without falling into the overproduction trap.
Want to see how Acviss Origin can optimise your supply chain and reduce waste? Connect with us today and take the first step toward sustainable, waste-free manufacturing.