The integration of digital twin technology into production planning is transforming manufacturing processes across industries. This innovative approach offers detailed virtual replicas of physical assets, enabling businesses to optimise operations, predict issues, and improve efficiency. In this blog, we will explore the concept of digital twin technology, its benefits for production planning, and practical applications.
What is Digital Twin Technology?
Digital twin technology involves creating a digital replica of a physical asset, system, or process. This virtual model is continuously updated with real-time data from its physical counterpart, allowing for comprehensive analysis and simulation. Digital twins can range from simple models to complex simulations that replicate entire manufacturing systems.
Key Components of Digital Twin Technology:
- Physical Asset: The actual machinery, system, or process in the real world.
- Digital Replica: A virtual model that mirrors the physical asset.
- Data Connection: Continuous data flow between the physical asset and its digital twin, facilitated by sensors and IoT devices.
- Analytics and Simulation: Tools and algorithms used to analyse data and simulate scenarios within the digital twin.
Must Read: Why is Brand Protection Important for Your Brand
Digital Tokenisation in Digital Twin Technology
Digital tokenisation is emerging as a crucial component of digital twin technology, enhancing security, transparency, and interoperability in production planning. Tokenisation involves converting digital twin data into secure, immutable digital tokens that facilitate seamless data exchange while ensuring authenticity and security.
Benefits of Digital Tokenisation in Digital Twin Technology:
1. Data Security and Integrity:
Tokenisation ensures that data exchanged between digital twins and external systems is encrypted and secure, reducing the risk of cyber threats and data manipulation.
2. Enhanced Interoperability:
Utilising blockchain-powered tokenisation, digital twins can integrate seamlessly across different platforms and supply chain networks, improving collaboration and efficiency.
3. Transparent and Auditable Transactions:
Tokenised data creates a transparent and immutable ledger, enabling manufacturers to track every interaction and transaction within the digital twin ecosystem, ensuring accountability.
4. Efficient Asset Management:
With tokenised digital twins, manufacturers can optimise asset tracking, automate compliance processes, and streamline maintenance operations with real-time verified data.
5. Smart Contracts for Automation:
Smart contracts integrated with digital twin tokenisation can automate workflows, such as predictive maintenance alerts and resource allocation, reducing manual intervention and operational costs.
Incorporating digital tokenisation can further enhance the reliability, security, and efficiency of digital twin technology, paving the way for a more connected and intelligent production ecosystem.
Benefits of Digital Twin Technology in Production Planning
Enhanced Efficiency
- Real-Time Monitoring: Digital twins provide real-time insights into the status and performance of production systems, enabling immediate adjustments and optimisations.
- Predictive Maintenance: By simulating wear and tear, digital twins help predict equipment failures before they occur, reducing downtime and maintenance costs.
Improved Decision-Making
- Data-Driven Insights: Access to real-time and historical data allows for more informed decision-making, leading to better production outcomes.
- Scenario Testing: Digital twins enable manufacturers to test various scenarios and strategies virtually before implementing them in the physical world, minimising risks and uncertainties.
Cost Reduction
- Resource Optimisation: Optimising production processes and resource utilisation through digital twins can significantly reduce operational costs.
- Reduced Waste: By identifying inefficiencies and areas for improvement, digital twins help in minimising material waste.
Increased Flexibility
- Agile Production: The phygital approach allows for quick adjustments to production plans in response to market changes or unforeseen disruptions.
- Scalability: As businesses grow, digital twins can be scaled to accommodate new assets and processes without significant overhauls.
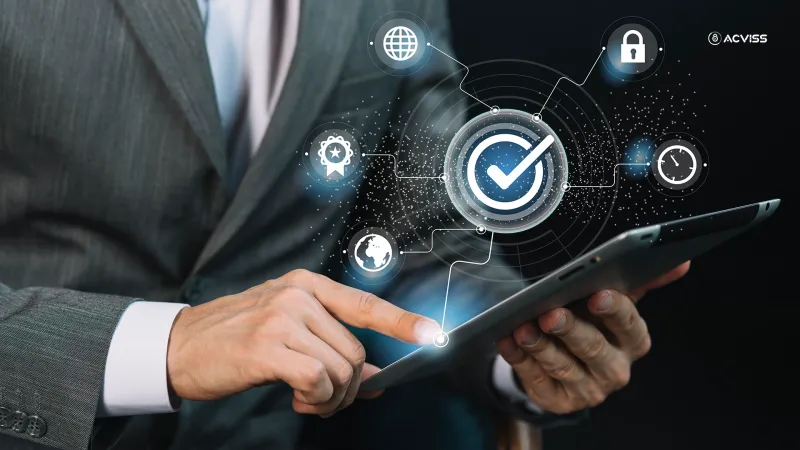
Practical Applications of Digital Twin Technology
1. Manufacturing Operations
- Assembly Line Optimisation: Digital twins of assembly lines can identify bottlenecks and streamline workflows, enhancing overall efficiency.
- Quality Control: Virtual models can simulate production processes to ensure that quality standards are consistently met.
2. Supply Chain Management
- Inventory Management: Digital twins can monitor inventory levels in real-time, ensuring that stock is maintained at optimal levels.
- Logistics Planning: By simulating transportation routes and delivery schedules, digital twins help optimise logistics and reduce delays.
Must Read: How Traceability Solutions are Reshaping Industries in 2024.
3. Product Development
- Prototyping and Testing: Digital twins enable virtual prototyping and testing of new products, reducing the time and cost associated with physical prototypes.
- Customisation: Manufacturers can use digital twins to customise products to meet specific customer requirements efficiently.
4. Energy Management
- Energy Consumption Monitoring: Digital twins can track and analyse energy consumption in production processes, identifying opportunities for energy savings.
- Sustainable Practices: By optimising energy use, digital twins contribute to more sustainable manufacturing practices.
Case Study: Digital Twin Implementation in Automotive Manufacturing
An automotive manufacturer implemented digital twin technology to enhance its production planning. By creating digital replicas of its production lines, the company achieved significant improvements in efficiency and quality control.
Results:
- Reduced Downtime: Predictive maintenance reduced equipment downtime by 30%, increasing overall productivity.
- Cost Savings: Optimised resource utilisation and reduced waste led to a 15% reduction in operational costs.
- Improved Quality: Enhanced quality control processes resulted in a 20% decrease in product defects.
Challenges and Considerations
1. Data Management
- Data Integration: Integrating data from various sources into a coherent digital twin can be complex and requires advanced data management solutions.
- Data Security: Ensuring the security of data transmitted between physical assets and digital twins is crucial to prevent cyber threats.
Must Read: A Comprehensive Guide to Ensuring Product Authenticity
2. Initial Investment
- Cost of Implementation: The initial investment in digital twin technology can be high, including costs for sensors, IoT devices, and software solutions.
- Training and Skills: Employees may require training to effectively use and manage digital twins, adding to the initial setup costs.
3. Scalability
- Scalable Solutions: Choosing scalable digital twin solutions that can grow with the business is essential for long-term success.
- Integration with Existing Systems: Ensuring that digital twins integrate seamlessly with existing production planning and management systems is crucial.
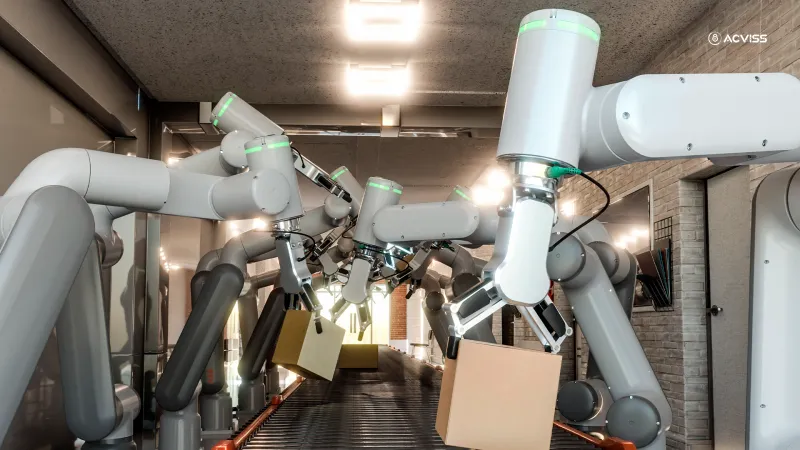
Future Trends in Digital Twin Technology
1. AI and Machine Learning Integration
- Enhanced Analytics: Integrating AI and machine learning with digital twins will enable more advanced analytics and predictive capabilities.
- Autonomous Decision-Making: Future digital twins may leverage AI to make autonomous decisions, further optimising production processes.
2. Increased Adoption in FMCG
- Broader Implementation: As the technology matures, more FMCG companies will adopt digital twins to enhance production planning and supply chain management.
- Cost Reduction: Continued advancements will reduce the cost of digital twin technology, making it accessible to a wider range of businesses.
3. Sustainable Manufacturing
- Environmental Impact: Digital twins will play a crucial role in reducing the environmental impact of manufacturing by optimising energy use and minimising waste.
- Circular Economy: The technology will support circular economy initiatives by enabling efficient recycling and reuse of materials.
Conclusion
Digital twin technology is revolutionising production planning by providing detailed virtual models of physical assets, enabling real-time monitoring, predictive maintenance, and scenario testing. The benefits of enhanced efficiency, improved decision-making, cost reduction, and increased flexibility make digital twins an invaluable tool for manufacturers.
As the technology continues to evolve, its integration with AI and machine learning will further enhance its capabilities, paving the way for more efficient, sustainable, and agile manufacturing processes.
If you are looking for someone to guide you through the anti-counterfeit solutions available, get in touch with us today. We, at Acviss have protected over 2 billion products, to over 80 brands globally. Our advanced anti-counterfeiting and brand protection solutions are always at your disposal. Reach out to us here to meet our experts and take your first step towards counterfeit-free market growth.