
Employee safety in any industry is more than a necessity; it becomes much more important for the manufacturing sector. Why? The manufacturing industry involves the usage of complex machinery and hazardous materials, which can raise potential risks at every step.
However, the sad fact is that sometimes manufacturers neglect best employee safety practices. What’s the reason? It’s because implementing safety practices takes extra effort, investment, and time.
Little do they know that maintaining workplace safety can help protect their workers from injury and keep them healthy for long, contributing to increased productivity and profitability. Even a report states that having an effective workplace safety management system in place can help reduce workplace injuries by up to 40%, improving employee morale and productivity.
With advancements in technology and evolving regulations, ensuring employee health and safety in 2024 requires not only adherence to standards but also proactive measures and cutting-edge solutions. Let’s explore the best practices for ensuring the safety of manufacturing employees.
The Importance of Health and Safety of Employees in Manufacturing
Manufacturing is a complex environment where many moving parts, heavy machinery, and dangerous raw materials are used. Do you know employees missed 66 working days on average because of workplace injuries in 2023? So, for manufacturers who don’t want their operations to suffer, they must take care of their employees’ health and safety.
Employee well-being is crucial not only to maintain operational efficiency but also to avoid accidents and injuries, reduce absenteeism, and improve employee morale. Accidents and illnesses at the workplace can lead to devastating consequences, such as lost productivity, higher insurance costs, and sometimes, even legal liability. Safe work culture fosters trust, which leads to improved overall performance and increased loyalty.
In 2024, prioritising employee safety is not just a legal obligation but a core business strategy that strengthens brand reputation and builds a resilient workforce.
Understanding Workplace Hazards for Employees in the Manufacturing Sector
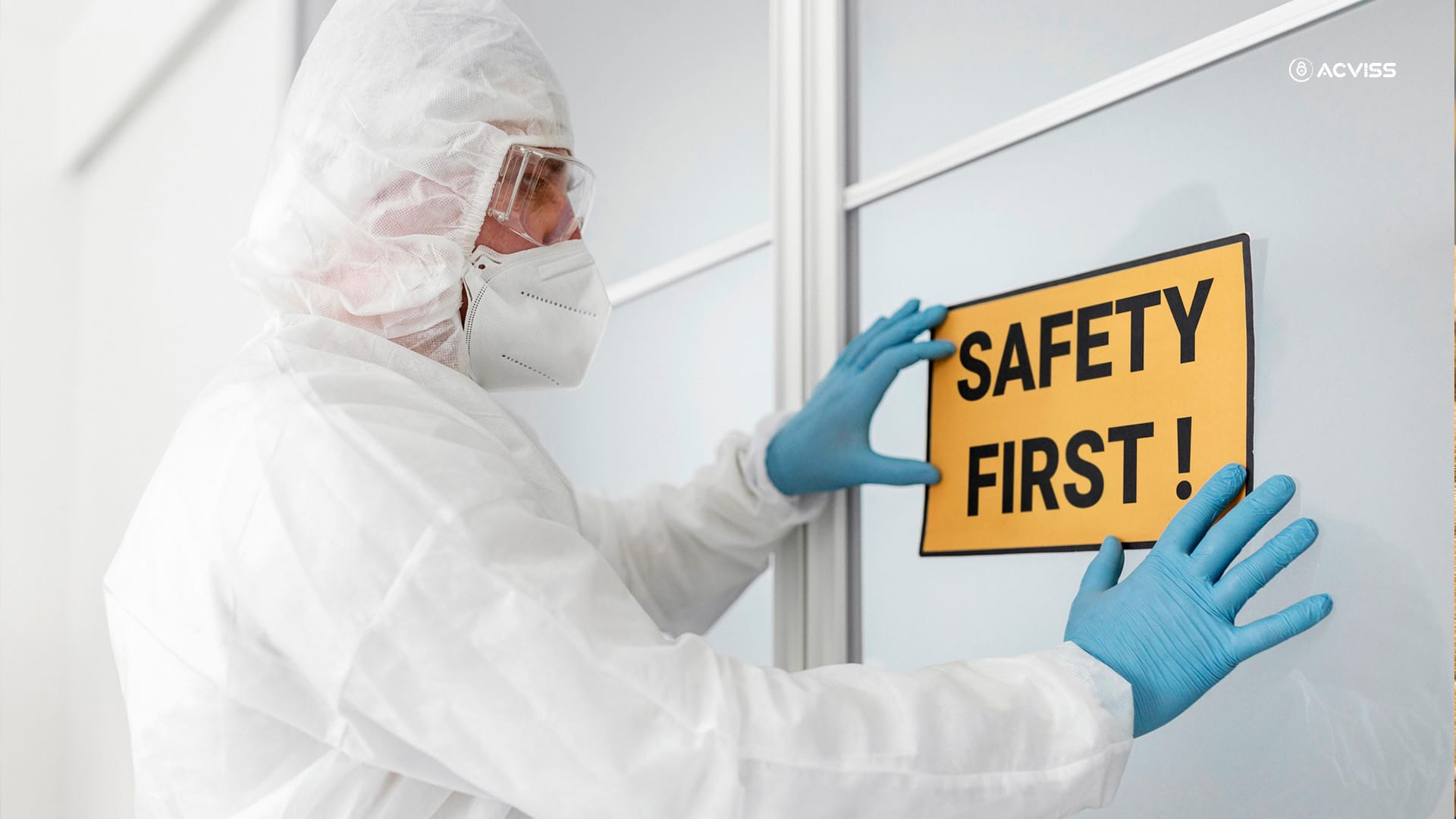
The manufacturing industry is a relatively more risky place to work where workers’ well-being can be threatened. But what hazards can employees actually face in this sector?
Understanding common hazards is crucial to developing and implementing effective safety strategies to mitigate potential risks that manufacturing operations can pose. So, here are some common workplace hazards in manufacturing:
1. Physical Hazards
Physical hazards are among the most visible dangers in manufacturing. Workers face risks from heavy machinery, sharp tools, and moving parts. Slips, trips, and falls are common due to wet floors, misplaced equipment, or poor lighting.
In addition, some workers can also suffer from severe injuries, like crushed limbs or amputations, when operating complex machinery without proper safeguards.
2. Chemical Exposure
Some manufacturing units involve painting, cleaning, or using raw materials like acids and solvents. In such units, employees often encounter fumes, splashes, or accidental spills, which can lead to burns, respiratory issues, or allergic reactions.
Even when exposed to these toxic substances for long, workers might experience long-term health complications, such as organ damage or cancer.
3. Ergonomic Issues
Employees often need to perform the same tasks for hours and tend to lift heavy materials, leading to muscle strain, joint pain, or chronic musculoskeletal disorders. In some cases, poorly designed workstations or tools force employees into unnatural positions, further exacerbating the risk.
4. Noise and Air Quality
Manufacturing plants are frequently noisy, with continuous operation of machines, cutting tools, and conveyors generating high decibel levels. Prolonged exposure to such noise can lead to hearing loss, stress, and reduced concentration.
Similarly, poor air quality, caused by dust, fumes, or particulate matter, can trigger respiratory issues, eye irritation, and long-term lung damage.
Regulations and Standards for Employee Safety in the Manufacturing Industry
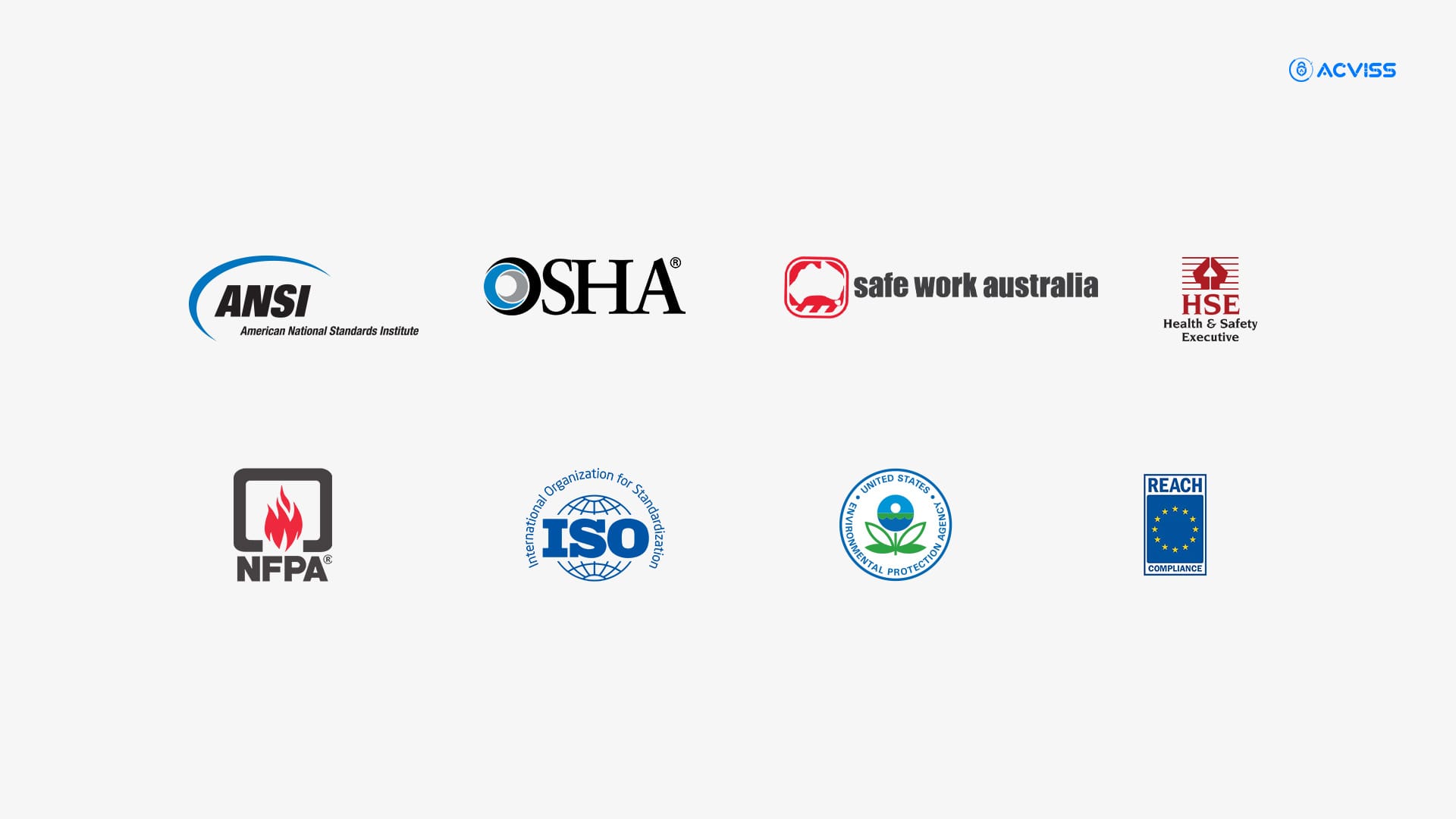
In the manufacturing industry, manufacturers must adhere to the following globally recognised regulations and standards to ensure workers safety in their units:
- OSHA (Occupational Safety and Health Administration): The OSHA establishes safety standards for industries to prevent workplace injuries, illnesses, and fatalities, including manufacturing. In addition, it’s mandatory to train employees and conduct regular inspections.
- ISO (International Organisation for Standardisation): ISO is an international framework designed to improve employee safety and reduce workplace risks. The standard requires organisations to assess risks, establish safety management systems, and continuously improve safety performance.
- REACH (Registration, Evaluation, Authorisation, and Restriction of Chemicals): Administered in the European Union, REACH regulates the use of chemicals in manufacturing. It requires manufacturers to evaluate the health and environmental risks of chemicals they use and register them with the European Chemicals Agency (ECHA). Moreover, manufacturers are restricted from using hazardous substances, and some are even banned.
- National Fire Protection Association (NFPA): The NFPA develops codes and standards to prevent fire-related hazards in manufacturing facilities. NFPA 70E, for example, provides guidelines on electrical safety in the workplace, including safe distances, personal protective equipment (PPE), and risk assessment protocols.
- Environmental Protection Agency (EPA): The EPA enforces regulations that limit environmental hazards from manufacturing processes, indirectly ensuring workplace safety. For example, the Clean Air Act and the Clean Water Act regulate the handling of pollutants that could harm workers and nearby communities.
- SAFE Work Australia: SAFE Work Australia is Australia's national policy body for workplace health and safety. The federal agency develops model codes of practice and guides managing industry risks, including manufacturing.
- Health and Safety Executive (HSE): In the UK, the HSE oversees workplace safety and enforces laws like the Health and Safety at Work Act 1974. It provides extensive resources for managing risks in the manufacturing sector, including guidance on handling machinery, lifting operations, and controlling exposure to hazardous substances.
- American National Standards Institute (ANSI): ANSI develops voluntary consensus standards for various industries, including manufacturing, that complement regulatory frameworks like OSHA. These standards cover diverse aspects of workplace safety, including machine operation, PPE design, and noise control.
Best Practices to Ensure Employee Safety for 2024
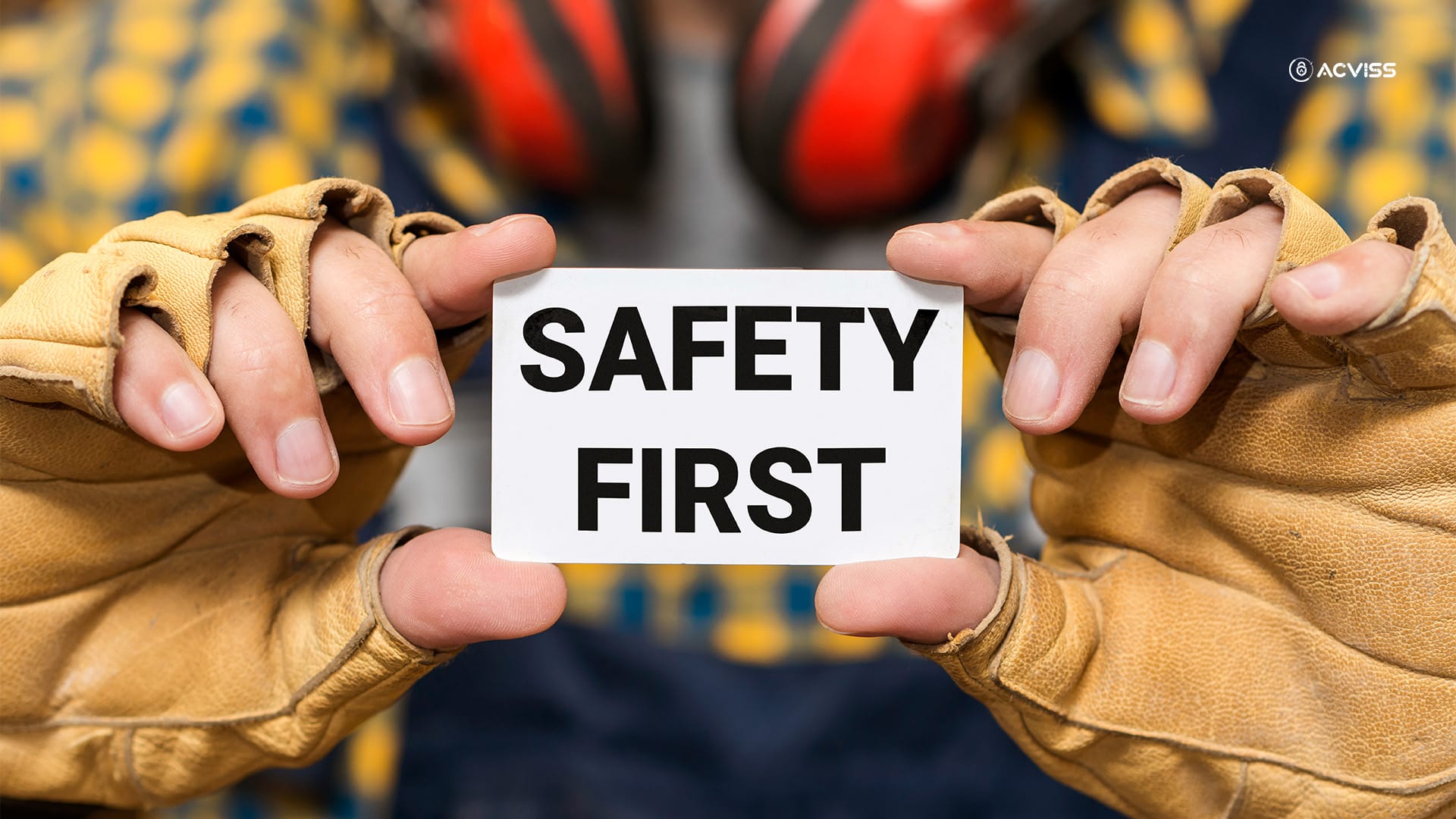
You now know what hazards workers face when operating in a manufacturing facility and what workplace safety regulations your facility needs to comply with. But how will you do it? You can create a safer and more resilient manufacturing environment by adopting the following discussed in comprehensive strategies:
- Implement Comprehensive Training Programs
Employee training is the cornerstone of workplace safety as it will help you ensure your workers understand safety protocols, emergency response procedures, and the correct use of machinery and equipment.
The training and education sessions you organise should address emerging challenges in manufacturing, such as automation hazards and the safe operation of advanced machinery. Moreover, you can incorporate hands-on workshops, virtual reality (VR) simulations, and e-learning modules to make training more engaging and effective.
- Use Advanced Safety Tools
Besides basic personal protection equipment (PPE), such as hard hats, safety glasses, shoes, boots, gloves, respirators, masks, or earplugs, consider using advanced safety tools to improve workplace safety.
For example, you can deploy IoT sensors to monitor environmental conditions such as temperature, air quality, and noise levels, providing real-time alerts for potential hazards. Also, equip wearable devices with GPS and biometric sensors to track workers' movements and health, offering immediate warnings in case of unsafe conditions or physical distress.
You can also use safety management software that centralises all needed data, enabling you to analyse trends, predict risks, and implement corrective actions promptly.
- Conduct Regular Audits and Risk Assessments
How will you know whether there is any workplace hazard or potential risk to employees? You can identify hazards and areas for improvement in your manufacturing unit by regularly conducting safety audits and risk assessments.
Advanced methods like digital audits, 3D mapping, and predictive analytics can provide a deeper understanding of potential risks. For example, identifying structural weaknesses in equipment through predictive maintenance can prevent accidents and improve manufacturing operations.
Organisations like Schindler have been able to improve their processes by logging safety hazards from 20 to 1,200 each year.
- Encourage Employee Engagement
Maintaining workplace safety is not a one-sided job. Your employees also need to be actively involved in shaping safety policies and practices for the culture of workplace safety to thrive.
Gathering feedback and deploying anonymous reporting systems will help foster accountability and collaboration. Employees often have firsthand knowledge of on-the-ground challenges and, thus, can provide you valuable insights to improve safety measures.
In addition, by recognising and rewarding adherence to safety protocols, you can also motivate your workers to prioritise safety in their daily tasks, reinforcing a collective commitment to well-being.
- Maintain Clear Safety Documentation
Clear and accessible safety documentation is essential for empowering employees to respond effectively during emergencies. You should regularly update safety manuals, standard operating procedures (SOPs), and emergency response to reflect current standards and risks.
How Can Acviss Help Improve Employee Safety in Manufacturing?
It’s not enough for you to deploy the above-discussed practices to ensure workplace safety. As we are in 2024, leveraging advanced solutions and technologies from Acviss, such as Certify and Origin, can revolutionise how manufacturing companies manage safety. These solutions go beyond compliance, offering proactive strategies to safeguard employees and streamline operations.
Certify: Enhancing Transparency and Accountability
Acviss Certify ensures that all safety equipment, machinery, and workflows meet predefined standards. By verifying the authenticity of safety gear and monitoring compliance, Certify can help minimise the risks associated with counterfeit products.
Benefits of Certify in Employee Safety:
- Guarantees that safety gear such as helmets, gloves, and masks are genuine and meet industry standards.
- Tracks certifications of equipment and machinery to ensure regular maintenance and proper functioning.
- Helps maintain transparent records for audits and regulatory compliance.
Origin: Transforming Workplace Monitoring and Traceability
Acviss Origin provides comprehensive traceability solutions to monitor manufacturing workflows. From tracking raw materials to final production, it ensures transparency and safety at every step.
How Origin Enhances Safety?
- Monitors the movement of hazardous materials within the manufacturing plant to prevent accidental exposure.
- Provides real-time data on workplace conditions, helping identify potential risks early.
- Enhances product traceability, ensuring that defective or unsafe products are flagged and removed promptly.
Final Words
Remember that ensuring employees' safety in the complex manufacturing environment is not a one-time job but requires continuous efforts. Manufacturers can enhance workplace safety while improving transparency, traceability, and accountability by implementing these discussed practices and trusting innovative solutions like Acviss Certify and Origin.
Take the first step toward a safer manufacturing workplace today. Explore Acviss to learn more about how Certify and Origin can transform your employee safety protocols.