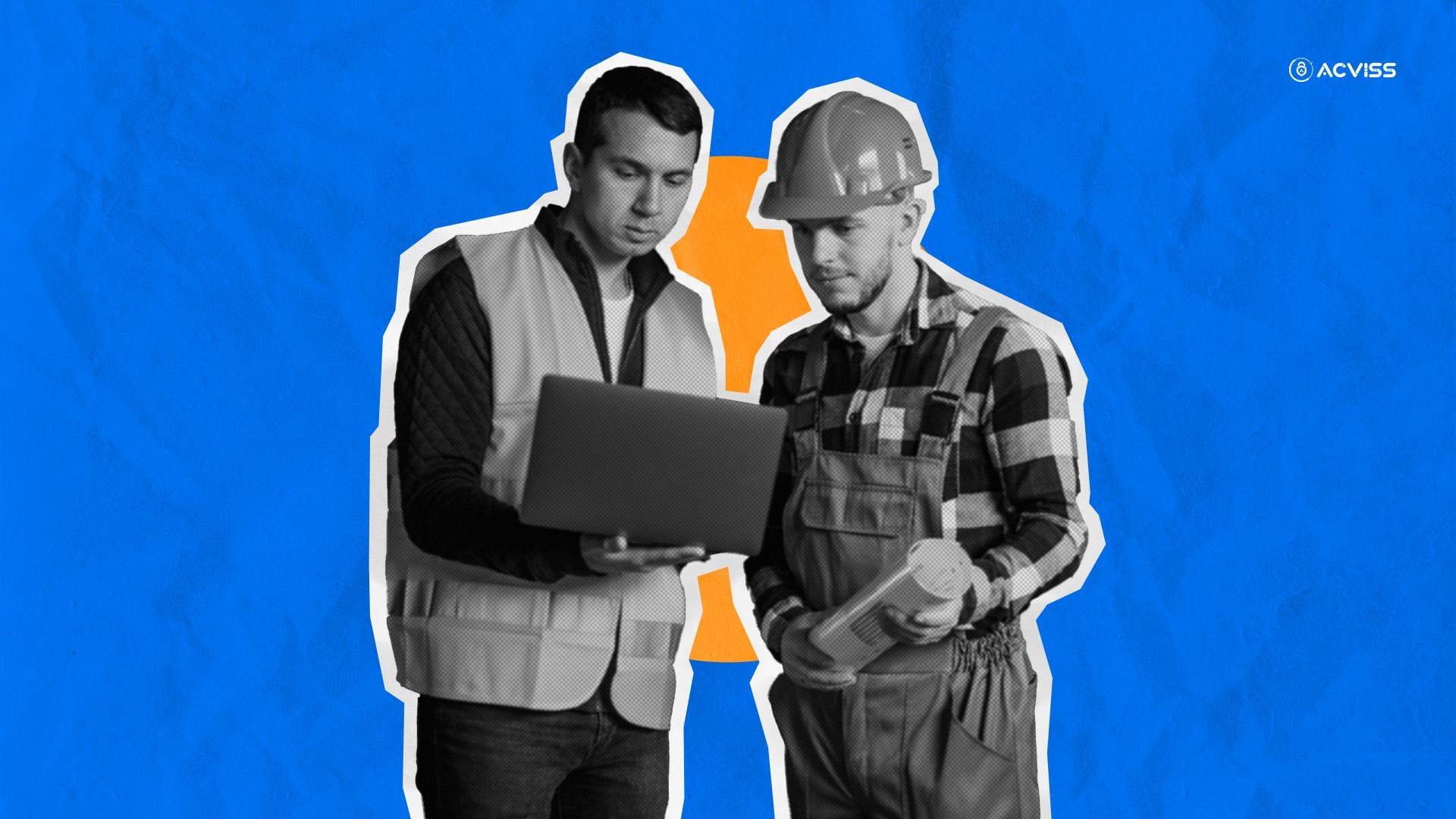
Manufacturing today is no longer a brute-force industry built on the volume of labour or the scale of equipment alone. It’s a data-driven, precision-oriented domain where seconds matter, materials are costly, and inefficiencies bleed revenue. At the heart of this transformation are production engineers, those unsung tacticians who recalibrate the very DNA of a production line to unlock efficiencies, remove bottlenecks, and optimise every moving part in a complex industrial system.
In many ways, they are both architects and surgeons of the shop floor, marrying systems thinking with hands-on interventions. But what exactly do they do to enhance efficiency, and why is their role increasingly becoming one of strategic importance in modern manufacturing?
Let’s delve into the advanced facets of production engineering that are actively shaping smarter, faster, and more sustainable manufacturing systems.
Engineering Efficiency: The Strategic Mindset of a Production Engineer
Production engineers are not confined to supervising machinery or maintaining output levels. Their actual domain is process optimisation at every level. Unlike operations managers who oversee throughput or quality analysts who focus on end-stage inspection, production engineers dive deep into the process itself, redesigning, restructuring, and reprogramming workflows to extract more value per cycle.
They begin by understanding the interconnected flow of processes, not in isolation but as a living, breathing ecosystem. From supply chain logistics and materials handling to robotic programming and waste minimisation, they analyse how each element affects the others. They aim to build lean systems, ones that minimise waste, maximise speed, and retain flexibility.
Precision Through Process Mapping and Simulation
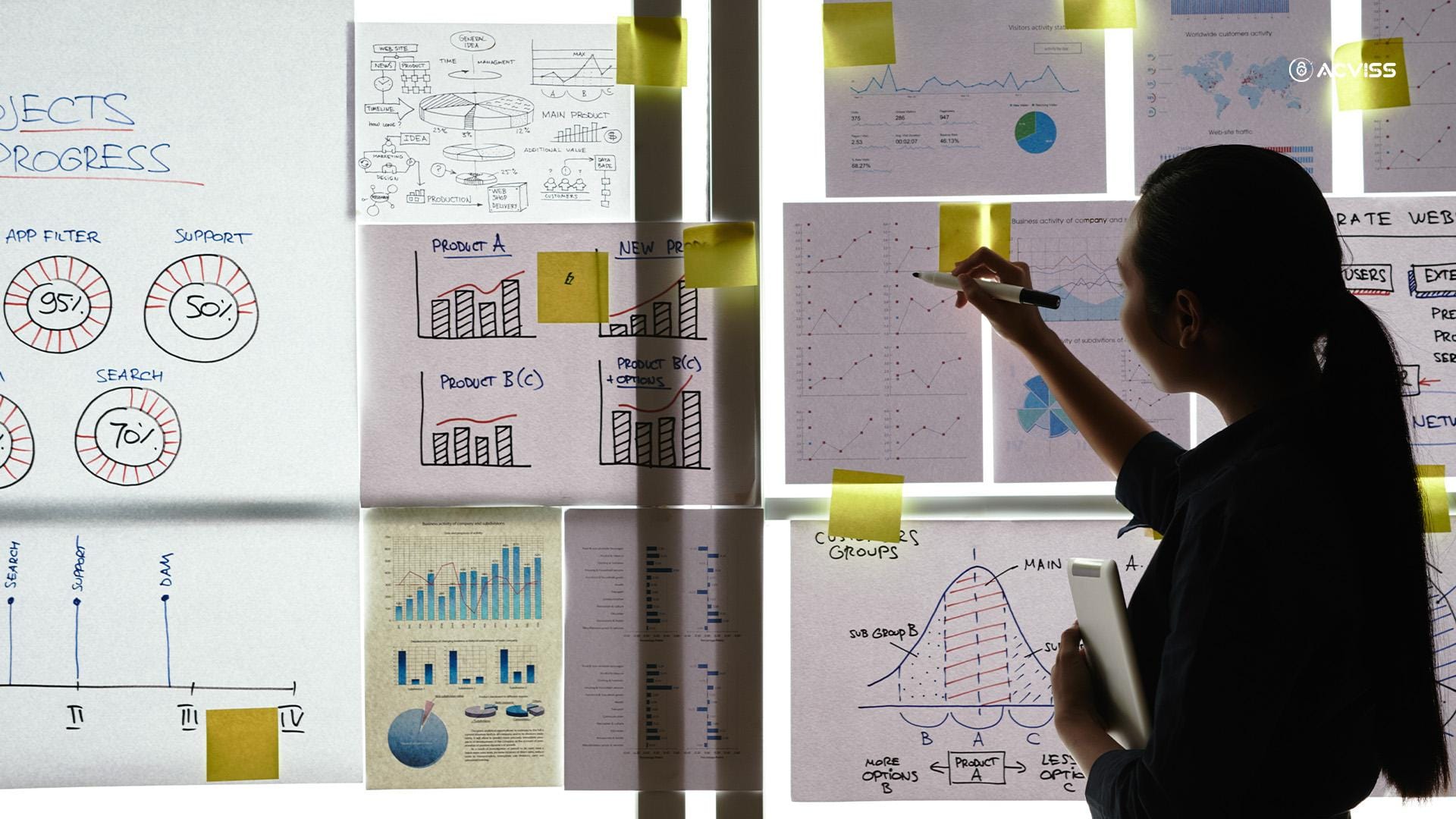
A cornerstone of a production engineer’s efficiency arsenal is process mapping, a detailed layout of how raw materials transform into finished goods through various stages. However, unlike traditional flowcharts, advanced process mapping involves digital twins, virtual replicas of physical production systems. These twins allow engineers to simulate process changes, test production scenarios, and predict impacts without interrupting actual operations.
With simulation models, production engineers can identify:
- Where cycle times can be compressed without compromising quality.
- How machine placement and worker ergonomics affect throughput.
- When to switch from batch processing to continuous flow.
These simulations feed directly into operational decisions, making process design more iterative and intelligent. It turns process optimisation into a science rather than a game of trial and error.
Leveraging Data for Real-Time Decision Making
Efficiency in manufacturing is increasingly driven by data, and production engineers sit at the heart of this data ecosystem. Advanced manufacturing setups are embedded with sensors, machine learning algorithms, and Industrial IoT (IIoT) frameworks that generate torrents of real-time data. But data alone is not enough. The production engineer's role is to convert it into action.
They monitor machine-level data for micro-stoppages, temperature anomalies, and vibration patterns, often indicating wear or future failure. They aggregate production data to assess yield losses and predict maintenance windows. More importantly, they analyse operator and machine interactions, ensuring that human-machine integration is both safe and optimised.
This real-time intelligence allows them to:
- Minimise downtime through predictive maintenance rather than reactive servicing.
- Adjust production schedules dynamically based on inventory levels or market demand.
- Reduce energy consumption by optimising equipment run times and loads.
In essence, production engineers bridge the gap between operations and analytics, ensuring that every decision made on the shop floor is rooted in insight, not intuition.
The Integration of Automation and Robotics
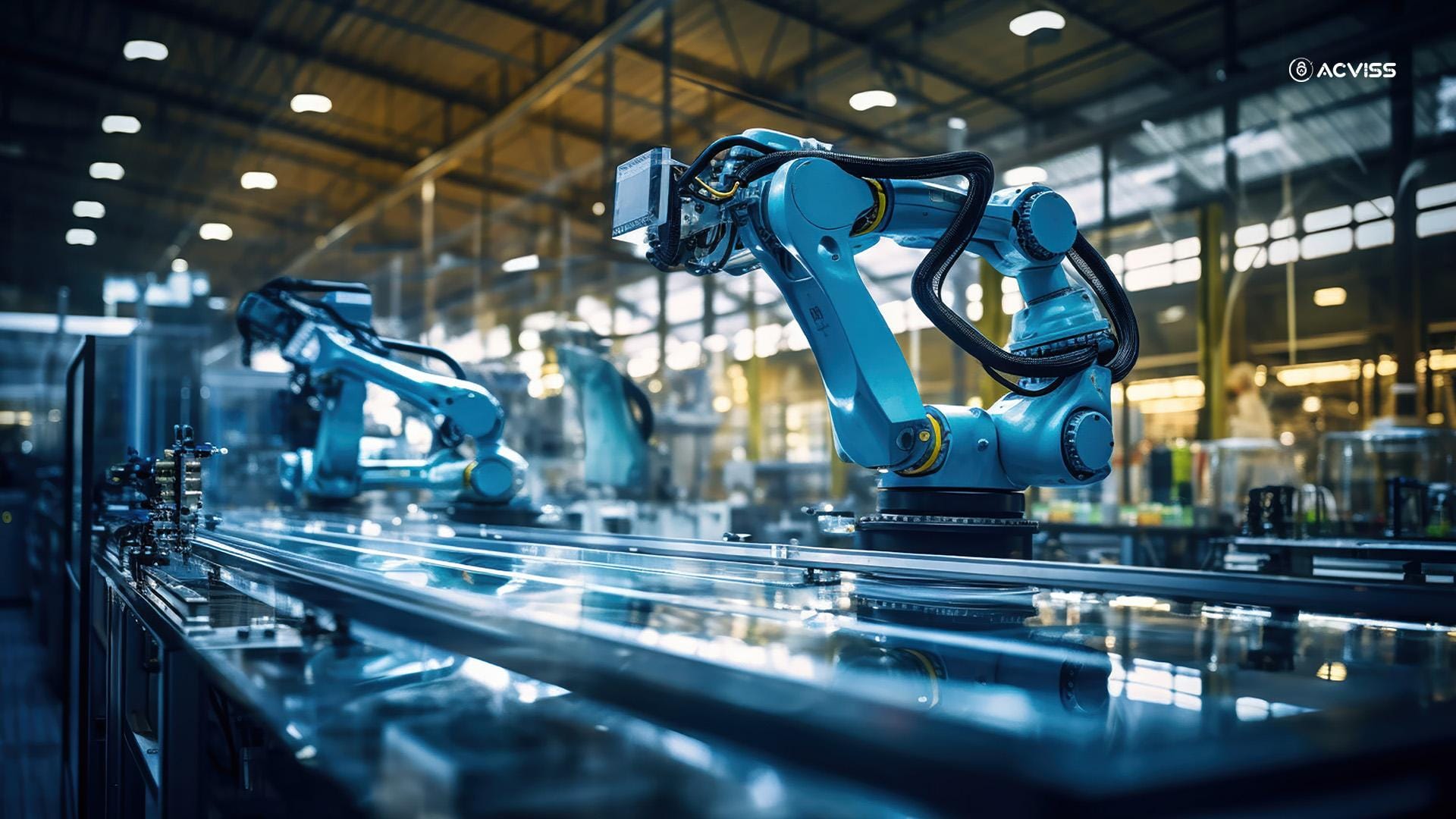
One of the more transformative arenas for production engineers lies in the integration of automation systems and robotics. While automation was once viewed as an isolated system upgrade, it is now an intricate part of manufacturing efficiency, designed, configured, and monitored by production engineers.
They are responsible for:
- Selecting automation systems that align with production volumes and variability.
- Programming industrial robots for repetitive or hazardous tasks.
- Designing control logic and ensuring interoperability between equipment.
Beyond technical integration, they also calculate the return on automation by assessing labour costs, cycle time reductions, and quality gains. Unlike blanket automation strategies, production engineers customise automation to fit production contexts, implementing collaborative robots (cobots) in human-intensive workflows, for example, or designing vision-guided systems for dynamic assembly lines.
This tailored approach ensures that automation doesn’t just replace labour, it enhances it by lifting productivity to levels unattainable through manual methods.
Lean Manufacturing and Continuous Improvement
Lean manufacturing, a philosophy rooted in reducing waste and delivering value, is often where production engineers leave their most lasting impact. They implement lean principles not as static checklists but as dynamic, ongoing initiatives that evolve with changing product lines and market conditions.
Key areas they focus on include:
- Value Stream Mapping: A comprehensive technique to visualise material and information flow across the production cycle, helping identify non-value-adding steps.
- Kaizen Events: Short-term, intensive projects that bring cross-functional teams together to improve specific production areas rapidly.
- Just-in-Time (JIT) Production: Reducing inventory waste by aligning production schedules with actual demand, avoiding overproduction.
But perhaps the most underappreciated aspect of lean lies in cultural transformation, fostering a mindset of continuous improvement among workers. Production engineers act as internal consultants, mentoring floor staff, suggesting improvements, and institutionalising change through Standard Operating Procedures (SOPs).
This cultural alignment makes lean sustainable, ensuring efficiency is not a one-time gain but a permanent shift.
Advanced Materials and Process Innovation
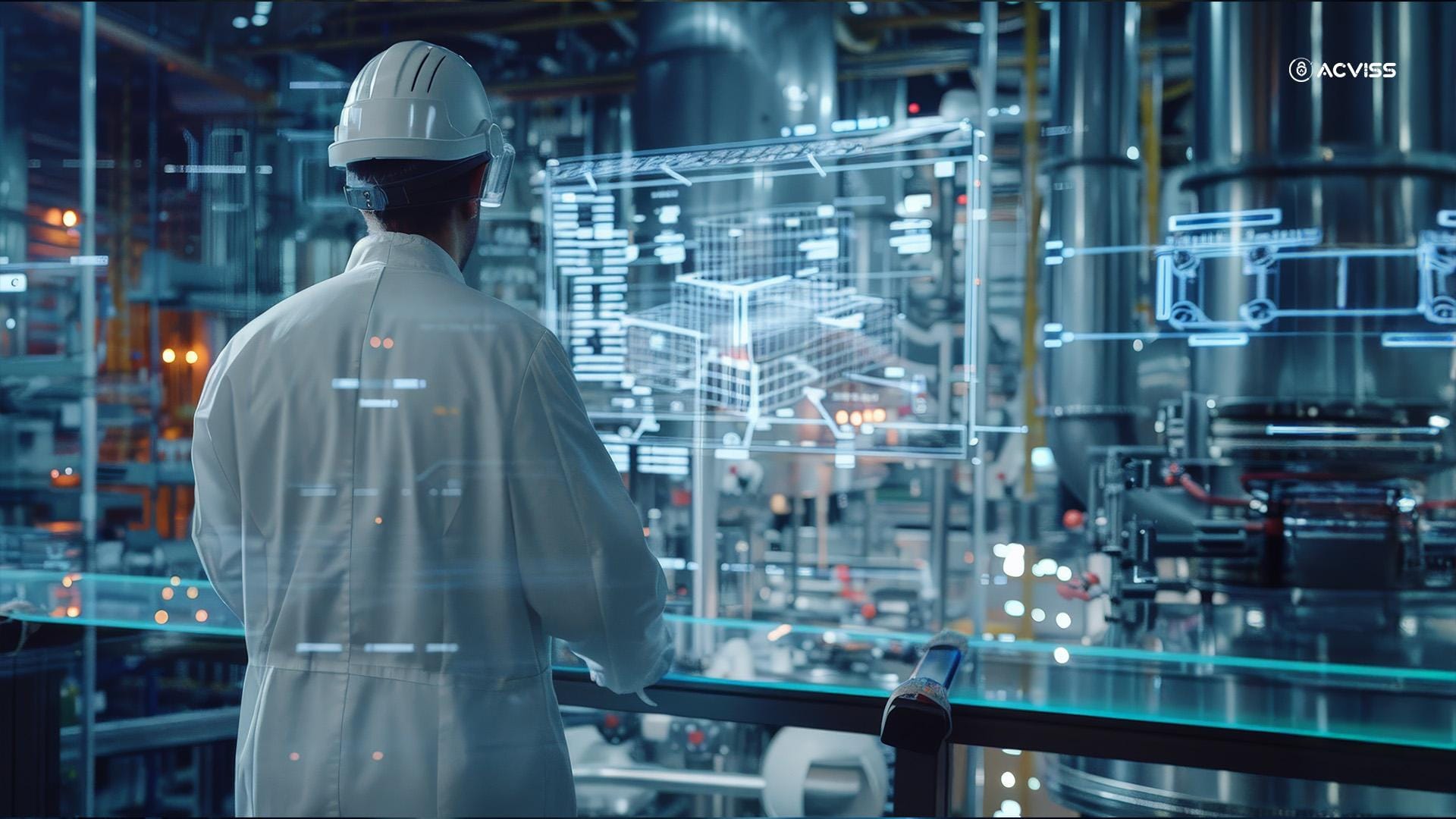
Modern manufacturing demands more than speed; it demands precision, repeatability, and adaptability to novel materials. Production engineers are increasingly responsible for evaluating and implementing new materials and process technologies that enhance efficiency without compromising quality.
This could mean:
- Adopting additive manufacturing (3D printing) to reduce waste and improve prototyping cycles.
- Integrating advanced coatings that reduce friction, wear, and downtime in mechanical systems.
- Using composite materials to cut down weight while retaining structural integrity in automotive or aerospace parts.
These decisions require a deep understanding of both materials science and process dynamics. It’s not just about knowing a material’s properties but knowing how it behaves under real production conditions, under heat, pressure, motion, and speed.
Production engineers work closely with design engineers and R&D teams to bring these innovations from lab to line, ensuring they are scalable, repeatable, and financially viable.
Human Factors Engineering: Efficiency Beyond Machines
Efficiency in manufacturing is not purely mechanical. Humans remain integral to even the most automated factories. From line-side decision-making to manual interventions during anomalies, human behaviour significantly influences output and quality.
Production engineers, therefore, apply ergonomics and human factors engineering to redesign workflows that align with human capabilities and limitations.
They conduct time-motion studies to identify wasted human effort. They optimise workstation designs to reduce fatigue and injury. They implement visual cues, haptic interfaces, and real-time feedback systems to improve decision-making and reduce errors.
By aligning mechanical efficiency with human usability, they create systems that are not only faster but also safer and more resilient.
Sustainability as a Driver of Efficiency
In today’s manufacturing landscape, efficiency is incomplete without sustainability. Energy consumption, emissions, material sourcing, and end-of-life recyclability are all metrics that now sit on the efficiency dashboard.
Production engineers are front-runners in ensuring that manufacturing systems:
- Use energy more efficiently by scheduling high-load operations during off-peak hours or optimising HVAC systems.
- Minimise water usage and chemical waste through closed-loop systems.
- Implement circular economy principles where scrap is not discarded but reintegrated into the production cycle.
In many advanced plants, production engineers now carry carbon budgets, not just time and cost budgets. Their ability to meet production targets while reducing environmental impact has become a strategic differentiator for organisations pursuing green manufacturing certifications or ESG compliance.
Cross-Functional Collaboration and Digital Leadership
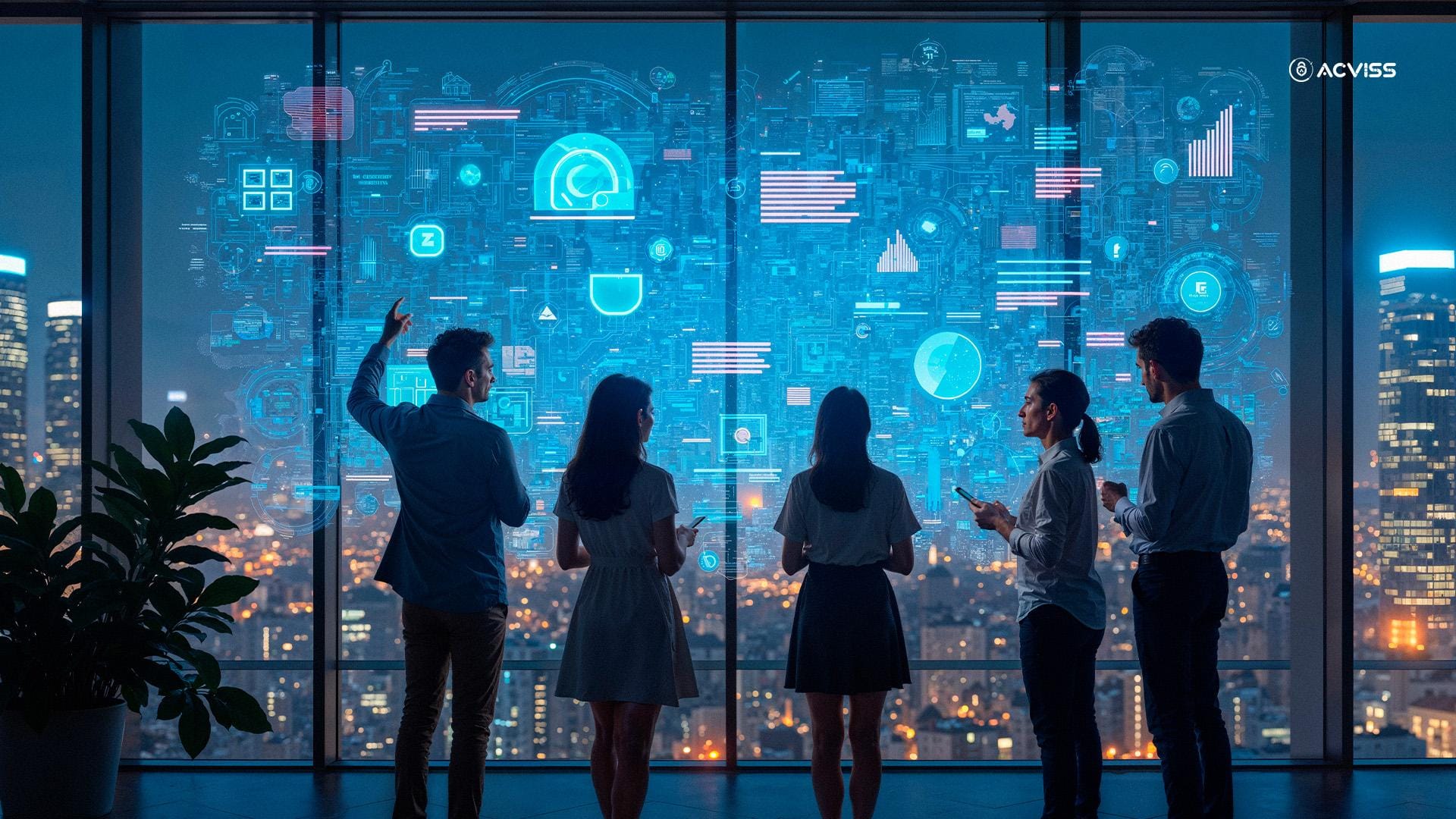
Finally, one of the most profound contributions of production engineers lies in their role as collaborative integrators. Efficiency does not emerge in silos. It’s a cross-functional pursuit where design, procurement, supply chain, quality control, and IT must all operate in sync.
Production engineers act as the glue, speaking the language of design and the dialect of operations, interpreting data while understanding floor realities. Their tools may be rooted in mechanical systems and PLC programming, but their output impacts business continuity, profitability, and customer satisfaction.
As factories become increasingly digital, production engineers are stepping into leadership roles. They champion Industry 4.0 initiatives, pilot digital twins, integrate AI-driven production systems, and mentor teams in hybrid manufacturing models. They are no longer just process improvers; they are digital transformation agents.
The Acviss Advantage: Efficiency Beyond the Factory Floor
In a hyperconnected manufacturing ecosystem, efficiency doesn’t end at the assembly line. It extends into supply chain transparency, product traceability, and brand integrity, where hidden inefficiencies and risks often go unchecked. This is where Acviss steps in.
Acviss empowers production engineers and manufacturers with cutting-edge technology to ensure product authenticity, streamline warranty management, and enhance traceability using blockchain and AI. From tamper-proof labelling to end-to-end supply chain insights, Acviss helps eliminate operational blind spots that traditional production efficiency models may overlook.
The Efficiency Engine of Manufacturing
In a world where market cycles are short, competition is intense, and customer expectations are unforgiving, manufacturing efficiency is not a luxury; it is survival. And production engineers are the unseen heroes powering this evolution. They blend engineering precision with systemic thinking, hands-on innovation with strategic insight, and data fluency with human intuition.
Their work is visible in the seamless hum of a balanced assembly line, in the predictive alerts that prevent breakdowns, in the dashboards that guide plant managers, and in the KPIs that determine corporate growth.
They are the invisible engine behind visible excellence.
Ready to Engineer the Next Level of Efficiency?
Explore how Acviss can work alongside your production engineering team to strengthen your factory’s digital backbone, enhance transparency, and protect your products. Get in touch with our experts today and take the next step towards sustainable, scalable efficiency.