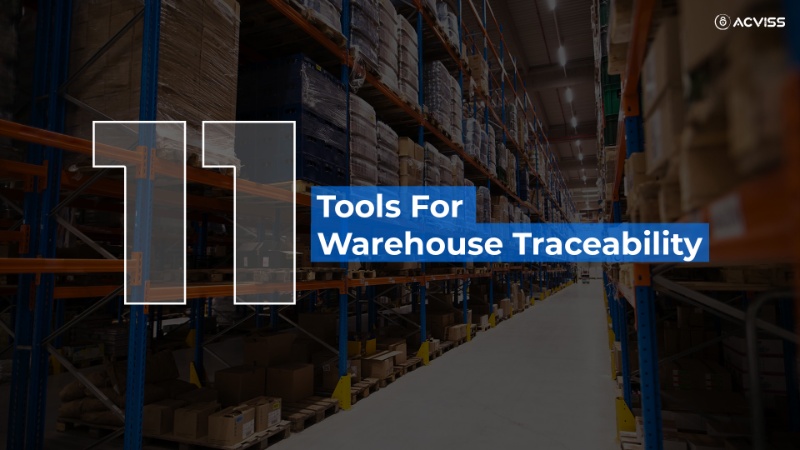
The success of your business depends on how well you control your inventory. A properly managed warehouse cuts down half the hassle of running a company. Plus it reduces a tremendous amount of unnecessary costs and enhances your supply chain visibility, adding to your profits!
Protecting inventory and securing your warehouse operation is the fundamental stage of your brand protection strategy.
So, if you are looking for a proper measure to take control of your warehouse operations and wish to double the profits, buckle up and tag along.
Contents
- Search For The Best Warehouse Management Practices.
- 1. Warehouse Management System (WMS) Software
- 2. Mobile Computers
- 3. Pick-to-Light Systems
- How it Works:
- 4. RFID Tags and Readers
- 5. Sortation Systems
- The advantages:
- 6. Voice-Directed Picking Systems
- 7. Automated Storage and Retrieval Systems (ASRS)
- 8. Conveyor Systems
- 9. Barcode Scanners
- 10. Packaging Machines
- 11. Real-time inventory visibility.
- 5 Basic Warehouse Management Processes.
- Key to Success
Search For The Best Warehouse Management Practices.
One key aspect of warehouse management is the use of tools and technologies that can help optimize warehouse operations and processes. There are many such tools available in the market that can assist warehouse managers and workers in various tasks, such as inventory management, order fulfilment, picking and packing, shipping and receiving, quality control, security and more.
Here Are 11 Tools For Healthy Warehouse Management
1. Warehouse Management System (WMS) Software
If you run a warehouse, you know how important it is to have a clear picture of your inventory at all times. Without it, you could face problems like running out of stock, overstocking or misplacing items. WMS software can help warehouse managers plan, organize, control and optimize warehouse operations and processes. It can be integrated with other systems, such as ERP (enterprise resource planning), CRM (customer relationship management) or TMS (Transportation Management System), to provide a holistic view of warehouse activities and performance.
A WMS can also provide features such as:
- Inventory optimization
Order management
Picking and packing optimization
Shipping and receiving management
Quality control
Reporting and analytics
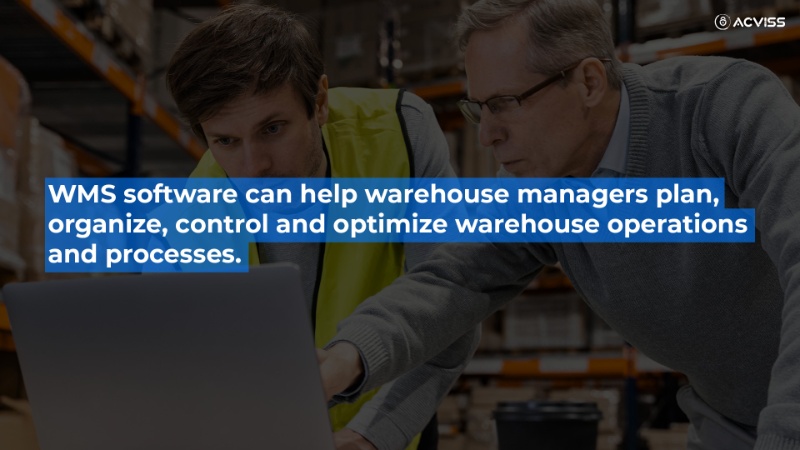
2. Mobile Computers
Mobile computers play a crucial role in modern warehouse operations, offering a versatile and efficient means of performing various tasks. These handheld devices are designed to enhance the functionality of warehouse management systems (WMS) and streamline the overall logistics process.
They perform various functions including scanning barcodes or RFID tags, accessing the WMS or other systems, communicating with other workers or managers, printing labels or receipts, capturing signatures or images, and more.
It helps warehouse workers to increase their mobility, flexibility, efficiency and productivity.
3. Pick-to-Light Systems
These systems utilize lights to guide warehouse workers to the correct locations and quantities of items to be picked for an order. Pick-to-light systems can help warehouse workers speed up the picking process, reduce errors and improve accuracy.
How it Works:
Each storage location in the warehouse is equipped with a light module. When an order is generated, the Pick-to-Light system communicates with the warehouse management or order processing system to identify the items and their locations. Lights at the corresponding storage locations illuminate to guide the worker to the correct spot. The system may also display the quantity to be picked at that location.
When the worker reaches the designated location, they confirm the pick by interacting with the system. This confirmation can be done through a button press, barcode scan, or other methods, depending on the system's design. Once the pick is confirmed, the system updates the order status and may trigger the illumination of lights at the next pick location.
4. RFID Tags and Readers
RFID (Radio Frequency Identification) tags are small electronic devices that can store and transmit data using radio waves. These devices can read and write data to RFID tags. It allows warehouse workers to automate the inventory management process, as they can track the location, status and movement of items in real time without requiring line-of-sight or manual scanning.
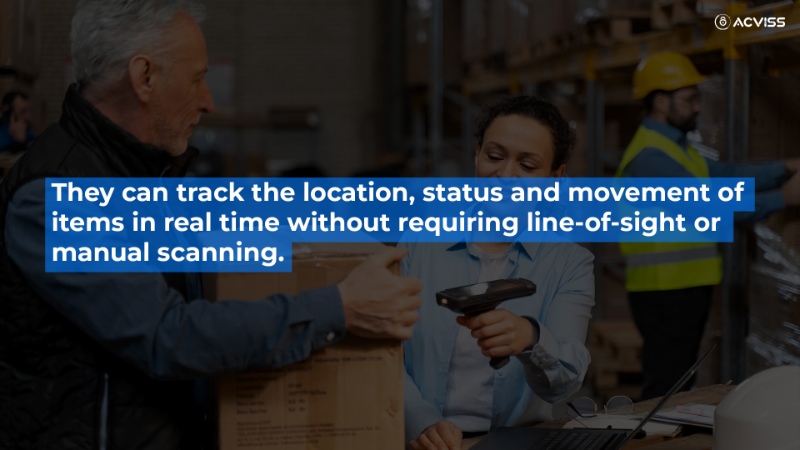
When an RFID tag enters the read range, the reader sends out radio waves. Passive RFID tags use the energy from these waves to power up and transmit their data back to the reader. The reader captures this data and can interpret it based on the unique identifier stored on the RFID tag. RFID readers come in various forms, including handheld devices, fixed readers installed in specific locations and integrated readers in other systems or equipment.
Find out how to Protect your brand in the modern landscape.
5. Sortation Systems
Sortation systems use sensors or scanners to sort items based on certain criteria; destination, weight, size or shape. This helps warehouse workers to improve order fulfilment speed, accuracy and quality.
The advantages:
Order Fulfilment Speed: Automating the sorting process fastens the order fulfilment, reducing the time it takes to process and dispatch orders.
Quality Control: The automated nature of the system helps eliminate human errors, ensuring that items are accurately sorted based on the defined criteria.
6. Voice-Directed Picking Systems
These systems use voice commands to instruct warehouse workers on what items to pick for an order. Voice-directed picking systems can help warehouse workers eliminate the need for paper lists or handheld devices, free up their hands and eyes, improve safety and ergonomics, and increase productivity and accuracy.
Workers are equipped with a headset and microphone connected to a voice-directed picking system. When an order is initiated, the system communicates the details to the worker through voice instructions. Interaction with the system is hands-free, allowing workers to focus on the task without needing paper lists or handheld devices.
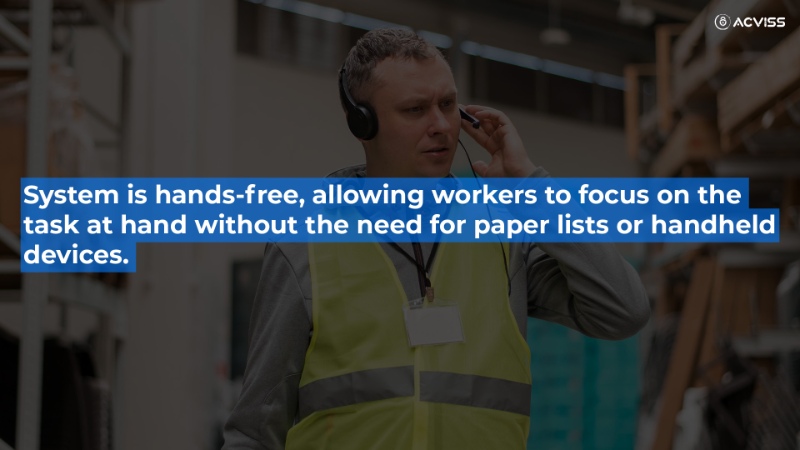
The worker receives spoken directions on the items to be picked, along with the quantity and the location within the warehouse. They can confirm the completion of each pick by responding verbally or through voice-activated commands afterwards.
7. Automated Storage and Retrieval Systems (ASRS)
ASRS use machines to store and retrieve items from high-density racks or shelves in the warehouse. ASRS typically consists of robotic arms, conveyor systems and automated vehicles that operate within a high-density storage structure. Items are stored in racks or shelves and the ASRS system is programmed to locate, pick and transport items to designated locations. The system is often integrated with a warehouse management system (WMS) to receive and process orders.
It helps warehouse managers optimize space utilization, reduce labour costs, increase inventory accuracy, improve security and safety and enhance efficiency by restricting access to authorized personnel and providing a controlled environment for inventory management. However, ASRS is advised to be used in industries with high-volume storage needs, such as e-commerce, manufacturing and distribution centres, to for optimum operational efficiency.
Must Read: How to Improve Brand Security by Reducing Shop Floor Theft
8. Conveyor Systems
Conveyor systems are systems that use belts or rollers to transport items from one point to another, connecting different areas such as storage, packing, and shipping.
Items placed on the conveyor system are automatically transported along a predefined path, eliminating the need for manual carrying or pushing.
This provides a number of benefits:
Reduction in Manual Handling.
Time and Energy Savings.
Workflow Streamlining.
Increased Throughput.
9. Barcode Scanners
Barcode scanners are devices that can read and decode barcode labels attached to products or packages. Barcode scanners can help warehouse workers quickly and accurately identify, locate, and track items in the warehouse. Barcode scanners can also reduce human errors, save time, and improve data accuracy.
A barcode scanner uses a light source and a photosensitive receiver to capture the patterns of black and white bars on a barcode. The captured data is then decoded by the scanner to reveal information such as product details, serial numbers, or other identifiers. The decoded information is often sent to a connected computer or warehouse management system for further processing.
Warehouse workers can use handheld barcode scanners to scan barcode labels on products, pallets, or bins. The scanned information is instantly displayed on the scanner's screen or transmitted to a central database, providing real-time updates on inventory status.
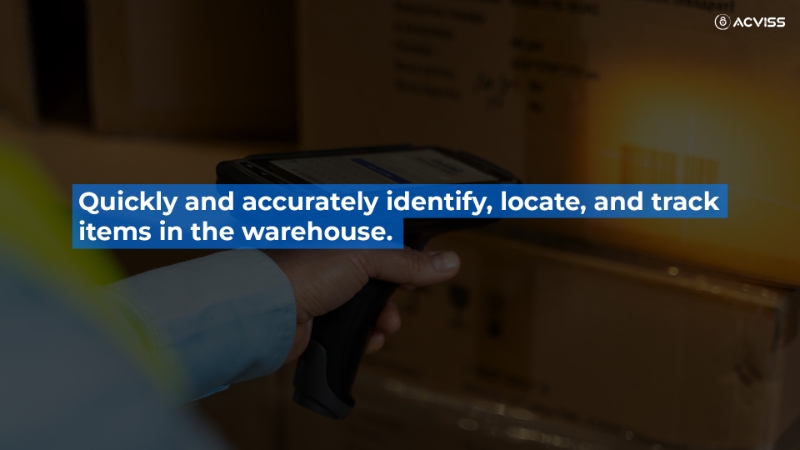
10. Packaging Machines
Packaging machines play a crucial role in the final stages of warehouse operations by automating various tasks related to packaging items for shipment. These machines are designed to handle functions such as sealing, wrapping, labelling and weighing, contributing to the overall efficiency of the packaging process.
This allows the organisation to minimise waste and ensure that materials are used in the most cost-effective manner, saving cost through increased efficiency, reduced labour requirements and minimized material expenses. Packaging systems also improve customer satisfaction by ensuring that products reach customers in optimal condition, enhancing overall customer satisfaction.
11. Real-time inventory visibility.
Real-time inventory visibility is the feature that allows you to see your inventory levels as they change in real-time. It shows you what you have, where it is and how much of it. This way, you can manage your inventory with accuracy and confidence.
But how to achieve real-time visibility?
Investing in Track-and-Trace Solutions helps monitor and verify the movement of your products throughout the supply chain, from the point of procurement to the point of production. Solutions like Origin have the capability to track the packages in real time providing updated reports in a format of your choice, enabling efficient supply chain management.
How did Amazon's transparency program fail to meet expectation?
Real-time inventory visibility helps you to:
Control your inventory precisely. You can track every item in your warehouse, from receiving to shipping. You can also optimize your storage space and layout, ensuring that your inventory is organized and accessible.
Maintain stock balance. You can monitor your inventory levels and replenish them as needed. You can also avoid ordering too much or too little, saving you money and space.
Better demand prediction. You can analyze your inventory data and identify trends and patterns. You can also anticipate customer needs and preferences, allowing you to plan ahead and meet demand.
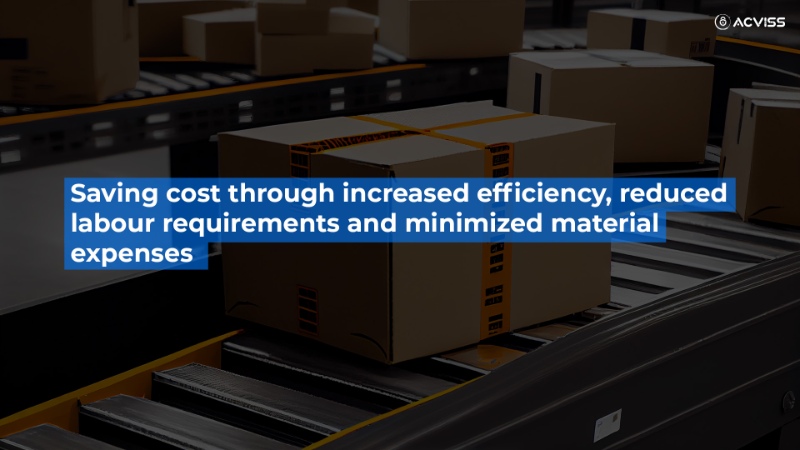
5 Basic Warehouse Management Processes.
Warehouse and inventory management is essential for running a business. But what is essential for operating a warehouse? Take a look at 5 essentials for warehouse management.
Inventory tracking
Monitor and constantly update stock levels, as well as forecast demand and replenish inventory when needed. Inventory tracking helps to optimize storage space, reduce costs, and prevent stockouts or overstocking.Receiving and stowing
The process of accepting incoming goods from suppliers or manufacturers, inspecting them for quality and accuracy and storing them in the appropriate locations within the warehouse. It requires efficient and rapid handling of goods, as well as accurate recording of inventory data.Picking and packing
This is the process of retrieving items from storage locations and preparing them for shipment to customers or stores. It involves generating pick lists, locating and scanning items, packing them securely and labelling them correctly.Shipping and quality control
Dispatching orders to customers or stores, as well as ensuring that they meet the required standards and specifications should be a top priority for any business or warehouse. Shipping and quality control concerns coordinating with transportation companies, verifying orders, tracking shipments, and resolving any issues or complaints.Reporting and analytics
Enhance performance with real-time visibility and data-driven decision-making. Utilize warehouse management software to collect, analyze, and present crucial data on inventory, staff productivity, order fulfilment and customer feedback.
Key to Success
Remember, your warehouse management is not limited to just 11 tools. As technology continues to evolve, newer, refined solutions will rise and adopting these tools and updating them constantly will be key to staying ahead in the competitive landscape of modern logistics.
If you are interested in learning more about our track-and-trace solutions and how they can help you improve your warehouse management and supply chain performance, get in touch with us today. We at Acviss have secured over 400 million products globally across various industries including Agri-tech, pharmaceuticals, cosmetics, electronics and many more.