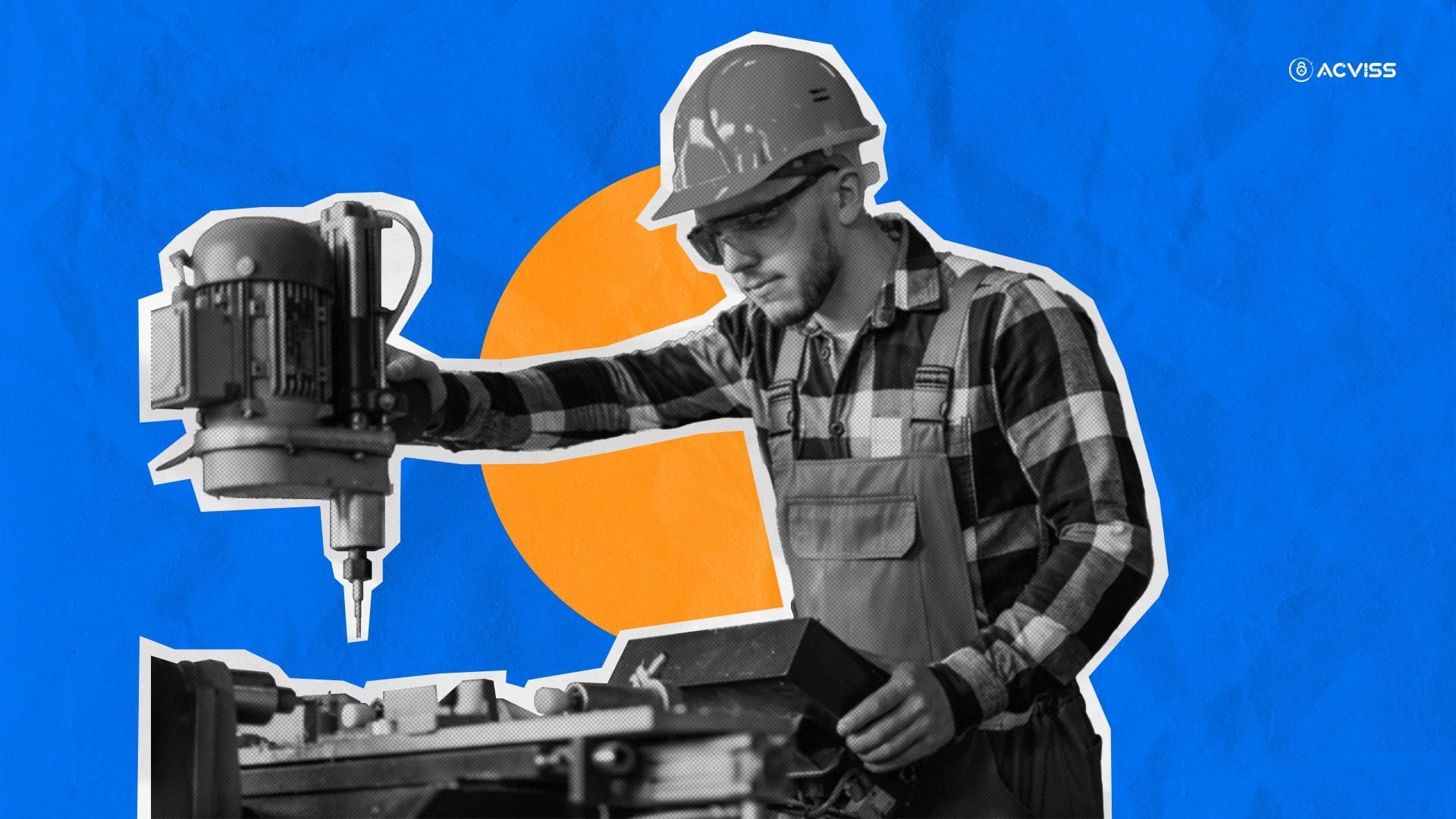
Choosing the right manufacturing process is more than a question of output; it's a core strategic decision that defines your product quality, speed to market, cost structure, and ability to scale. In a competitive, consumer-driven environment, manufacturers must balance efficiency, flexibility, and traceability while safeguarding their brand’s integrity.
This comprehensive guide unpacks the three dominant manufacturing models, Batch, Mass, and Custom, along with their operational intricacies, strengths, limitations, and real-world applications. Whether you're managing pharmaceutical batches, consumer goods, or luxury items, understanding these systems can directly impact your bottom line.
Batch Production: Structured Flexibility in Action
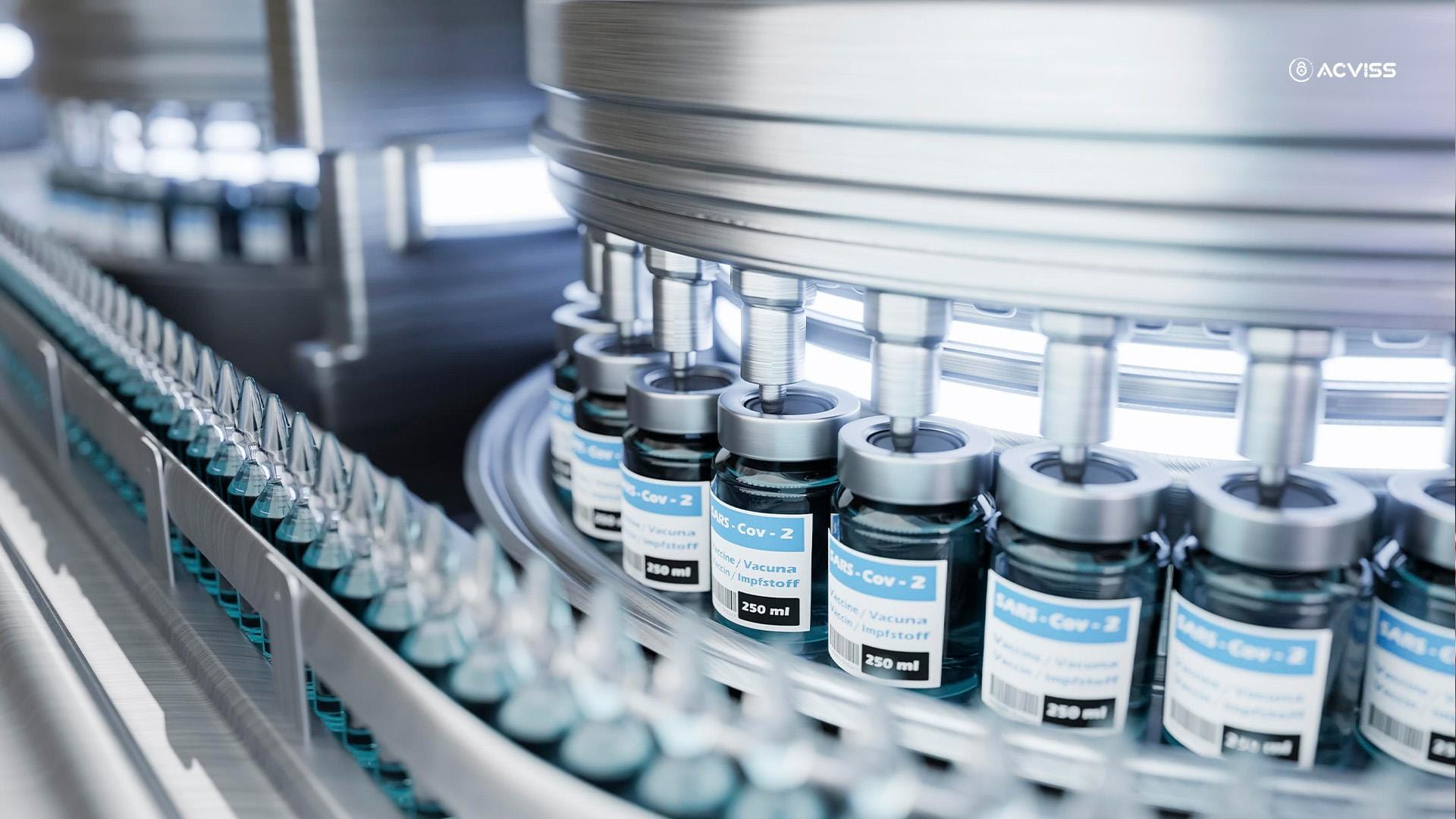
Batch production allows manufacturers to produce goods in defined groups or “batches” before switching to the next type of product. This approach blends flexibility with cost control and is particularly useful when products require variations in formulation or design but do not warrant full customisation.
Key Characteristics:
- Moderate production volumes with flexible scheduling.
- Shared machinery used for different products, reducing capital expenditure.
- Changeovers between batches allow multiple SKUs to use the same line.
Advantages:
- Greater flexibility than mass production, easy to switch between products.
- Efficient resource use, especially in facilities producing multiple product types.
- Ideal for quality control, each batch can be inspected and traced separately.
Challenges:
- Downtime between batches due to cleaning and setup changes.
- Complex inventory planning to ensure raw materials are available in sync.
- Batch variability may arise if processes aren’t tightly controlled.
Common Use Cases:
- Pharmaceuticals (e.g. creams, capsules)
- Food and beverage (e.g. sauces, bakery items)
- Chemicals and coatings (e.g. paints, adhesives)
Why It Matters:
Batch production is favoured in sectors requiring regular product adjustments without full-scale retooling. However, it also demands precise traceability to meet compliance and safety standards.
How Acviss helps: Origin from Acviss adds an extra layer of security and compliance by tracing each batch’s provenance using blockchain, ensuring real-time visibility and tamper-evidence.
Mass Production: Efficiency at Scale
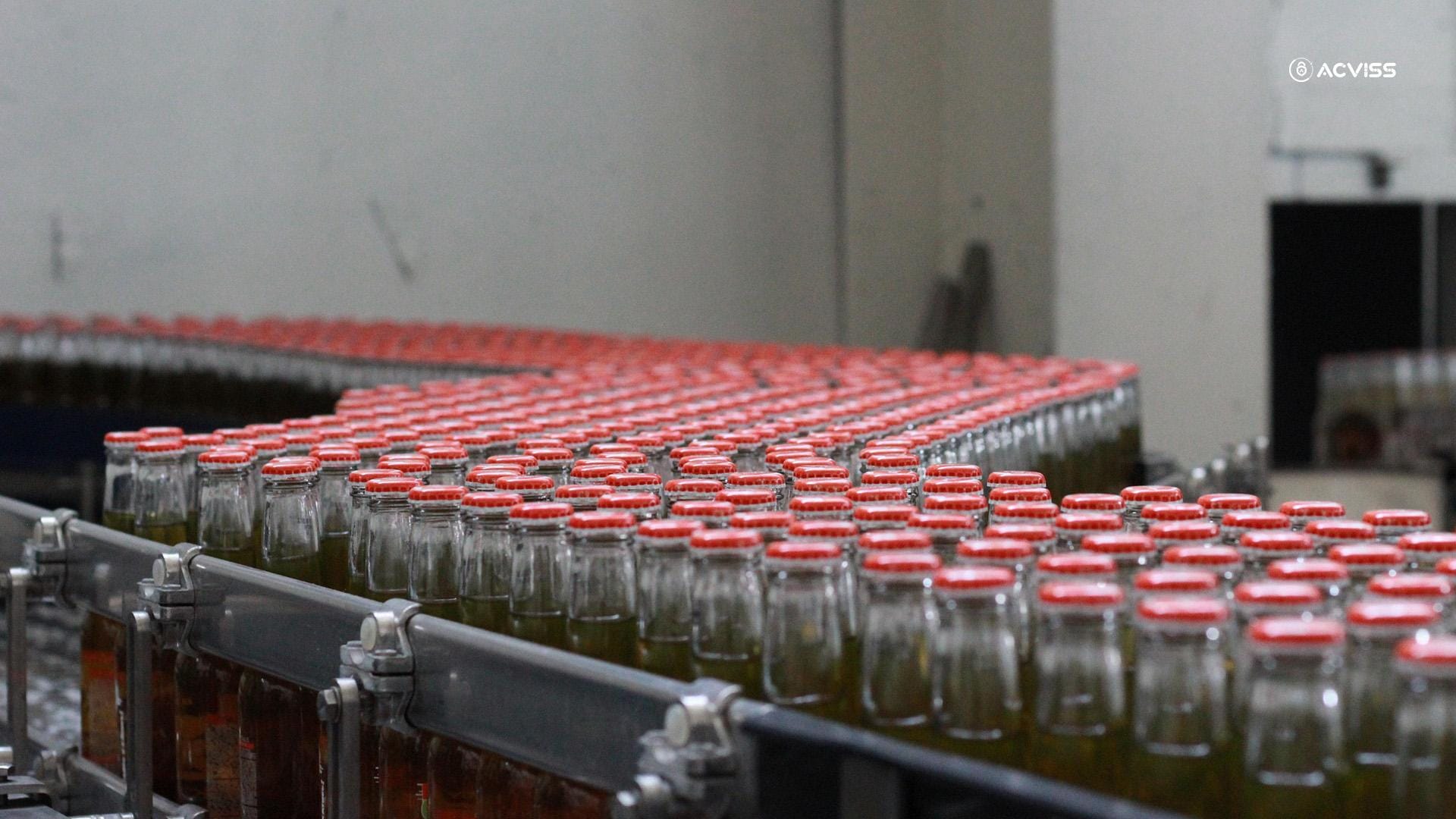
Mass production is designed for high-volume, low-variation manufacturing. Once set up, the process runs continuously with minimal interruption, delivering vast quantities of uniform products at low per-unit costs.
Key Characteristics:
- High levels of automation with minimal manual intervention.
- Standardised outputs, consistent quality, and reduced cycle times.
- Low flexibility, changes are expensive and slow to implement.
Advantages:
- Significantly reduced cost per unit thanks to economies of scale.
- Consistent product quality due to standardised operations.
- High throughput is suitable for global demand and large-scale distribution.
Challenges:
- High initial capital investment in specialised equipment.
- Inflexible production lines make it hard to respond to market shifts.
- Risk of overproduction, leading to inventory waste or markdowns.
Common Use Cases:
- Packaged consumer goods (e.g. toothpaste, shampoos)
- Electronics (e.g. smartphones, TVs)
- Automotive components (e.g. gearboxes, seats)
Why It Matters:
Mass production works when demand is stable, margins are thin, and the market rewards scale. But the very systems that offer cost efficiency can become brittle when customer preferences change or regulatory expectations rise.
How Acviss helps: With millions of identical items produced, counterfeiters target these markets aggressively. Acviss’s non-cloneable labels and real-time verification tools ensure that even mass-produced goods retain unique authenticity, helping manufacturers safeguard both their customers and brand.
Custom Production: Precision and Personalisation
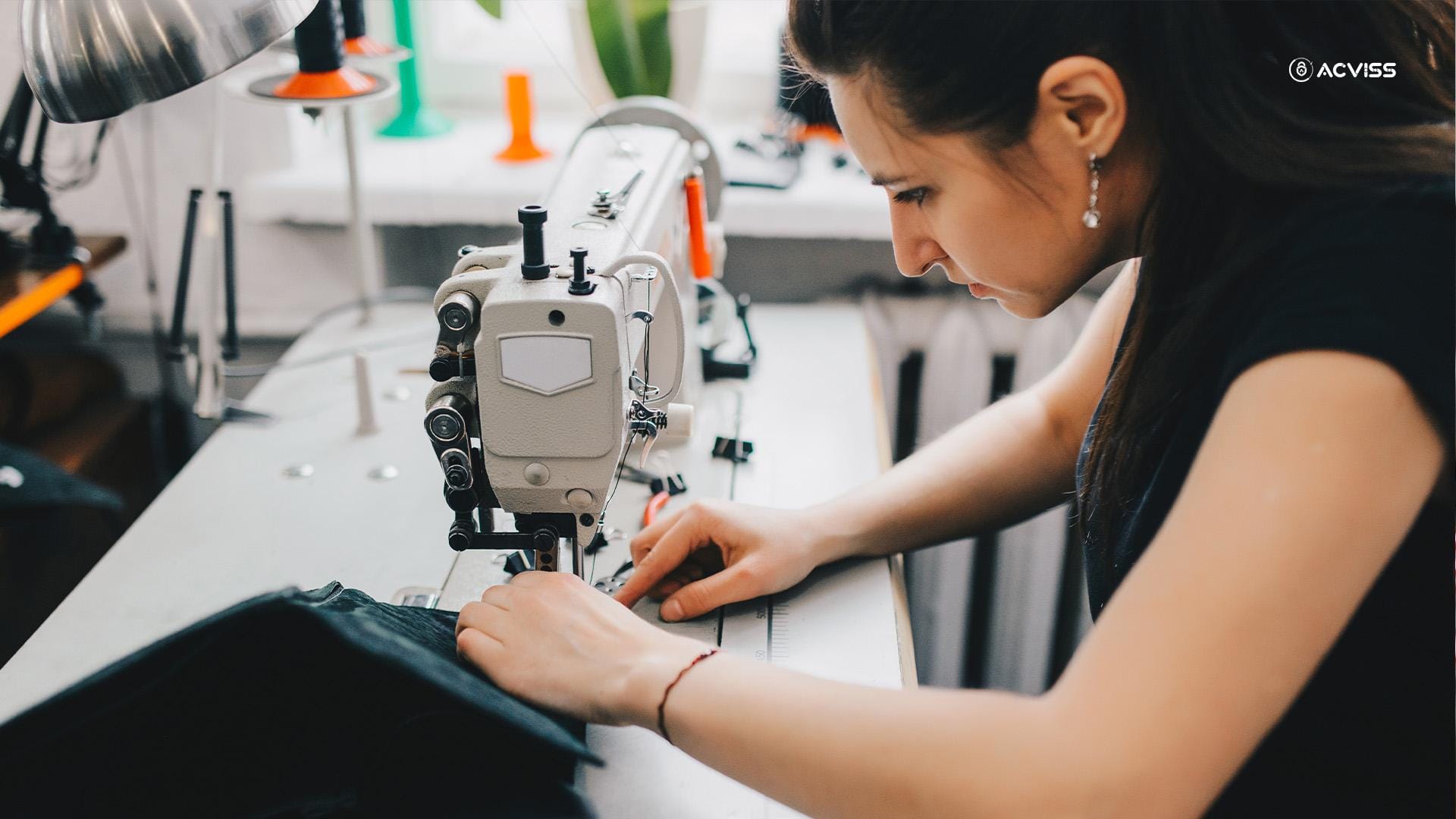
Custom production focuses on crafting unique or highly specialised products tailored to individual customer needs. Each unit may be one-of-a-kind or produced in very low quantities, reflecting a premium, highly personalised value proposition.
Key Characteristics:
- Made-to-order workflows, initiated after receiving a customer specification.
- High involvement of skilled labour, design teams, and iterative planning.
- Low volume, high value, often with extended production lead times.
Advantages:
- Maximum flexibility, products are crafted exactly as required.
- Reduced inventory risk, no large stockpiles or excess goods.
- High-margin potential, particularly in luxury or niche markets.
Challenges:
- Longer production cycles lead to slower time-to-market.
- Due to design, labour, and sourcing demands, there is a higher cost per unit.
- Complex coordination between customer, design, and manufacturing teams.
Common Use Cases:
- Bespoke furniture and interior elements
- High-end fashion and accessories
- Medical implants and precision tools
Why It Matters:
When consumer identity and personalisation drive brand loyalty, custom production enables deep differentiation. But it also heightens exposure to fraud and counterfeiting, especially for premium products with perceived exclusivity.
How to Choose the Right Manufacturing Process
The ideal production model depends on more than what you’re producing; it must align with your business strategy, market expectations, and regulatory requirements. Factors to consider:
1. Product Lifecycle and Innovation
If your products evolve rapidly, batch production provides the ability to innovate quickly without long retooling periods. If you're in a mature product segment, mass production offers stability and efficiency. Custom production suits limited-edition or seasonal offerings with high creative turnover.
2. Market Demand and Consumer Expectation
When the market values price and availability, mass production prevails. When it values uniqueness and craftsmanship, custom production leads. Batch production bridges both, offering limited editions or variations.
3. Compliance and Traceability
Heavily regulated sectors must consider how easily each model supports documentation, traceability, and audits. Batch and custom production excel here, especially when reinforced with technologies like blockchain traceability or non-cloneable product tags.
4. Cost and Operational Efficiency
Evaluate your capex and opex capabilities. Mass production requires upfront capital, but lowers long-term costs. Batch production spreads investment over a wider product range. Customisation demands variable costs but fewer fixed assets.
5. Risk of Counterfeiting
Mass and custom production both face distinct threats; mass products are copied due to scale, and custom ones for their brand value. In both cases, anti-counterfeit solutions like Acviss deliver authentication and trust.
The Rise of Hybrid Production Models
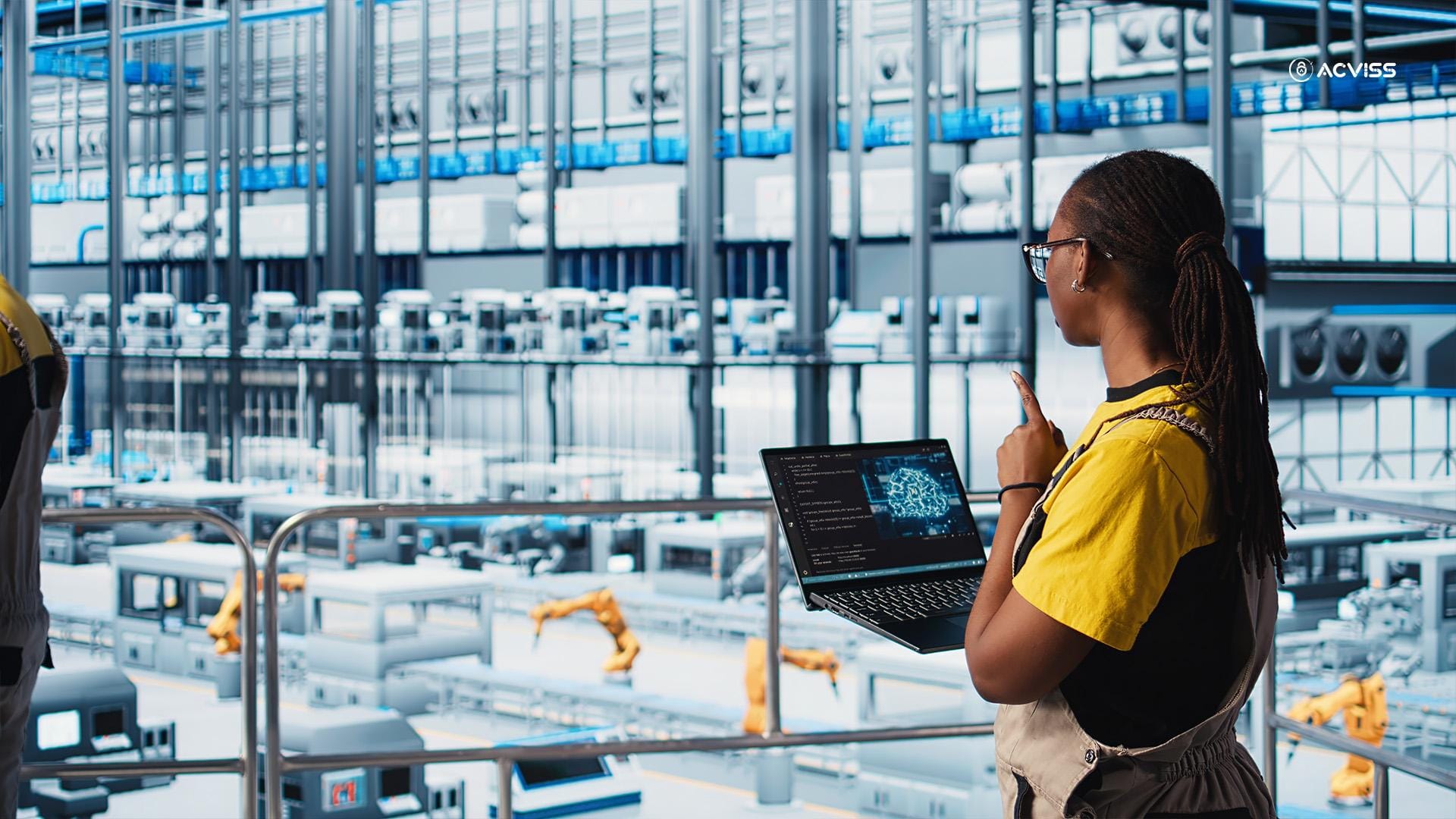
Forward-looking manufacturers are no longer picking just one model; they are combining elements from all three to stay agile. A coffee company might:
- Mass-produce standard blends for supermarkets,
- Batch-produce seasonal offerings, and
- Offer custom-labelled options through their e-commerce platform.
This hybridisation is powered by digitally integrated systems, flexible automation, and responsive supply chains. Tools like Acviss’s Certify and Origin allow traceability, real-time analytics, and authentication across all production scales, enabling consistency without compromising on agility.
Future-Proofing Your Production Strategy
Selecting the right production method is a decision that reverberates through your entire business, from procurement and supply chain to customer experience and brand integrity.
Whether you’re scaling up, diversifying your SKUs, or launching premium personalised lines, your production model should adapt, not just in process, but in protection.
Acviss enables manufacturers across all production models to protect, trace, and validate their products. Connect with us today and make your manufacturing smarter, safer, and future-ready.