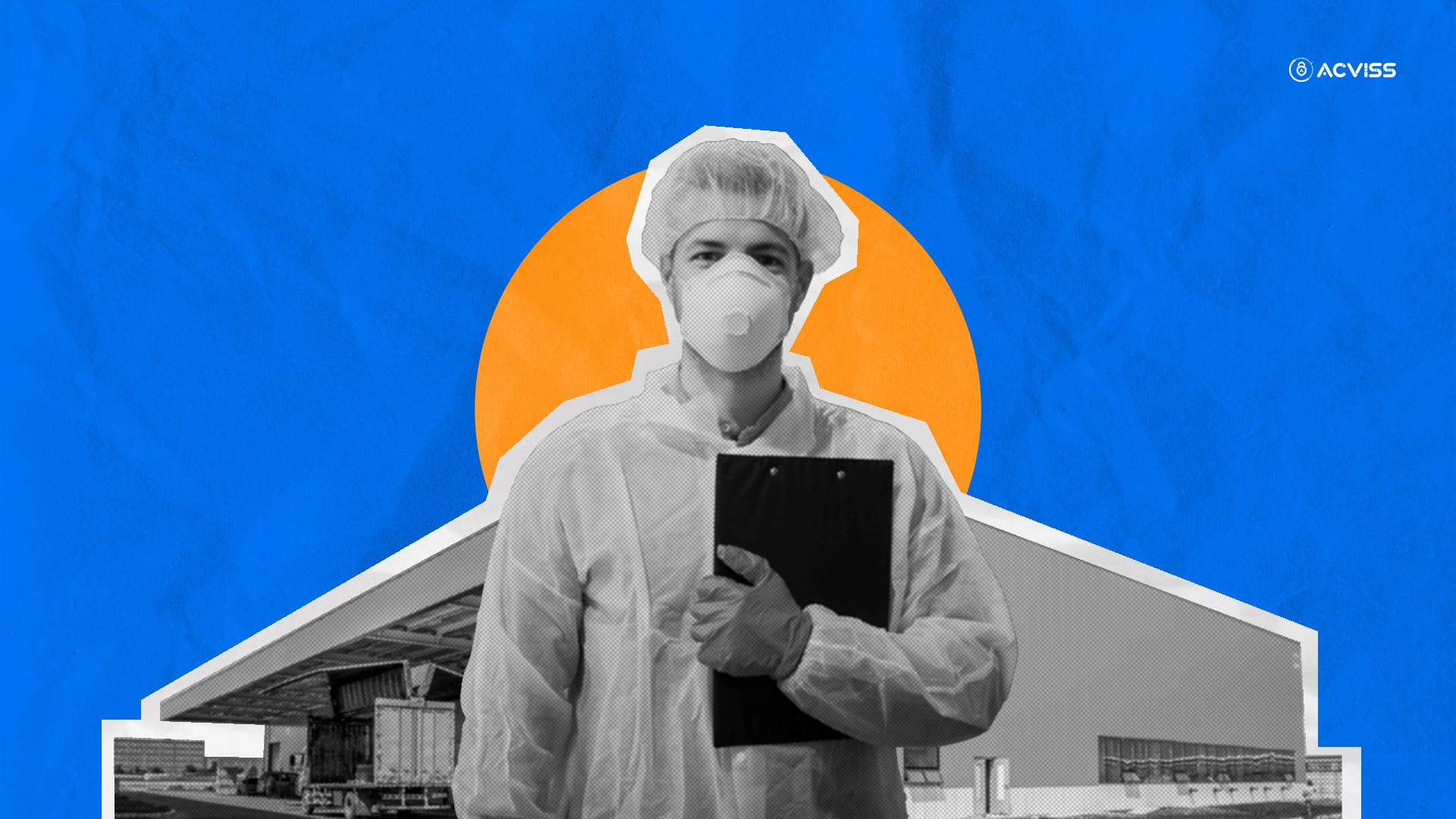
Third-party manufacturing has revolutionized industries, offering businesses a cost-effective and efficient way to produce high-quality products. However, with great opportunities come great responsibilities—particularly in quality control. In this blog, we’ll dive deep into the essentials of quality control in third-party manufacturing, explore common challenges, and offer actionable insights to ensure every product meets the highest standards.
The Foundation of Third-Party Manufacturing
Third-party manufacturing, also known as contract manufacturing, allows companies to outsource their production to specialised manufacturers. This model provides scalability, cost savings, and access to advanced technology. But quality control is the linchpin that holds it all together.
The pharmaceutical industry heavily relies on third-party manufacturers to meet production demands. Ensuring quality in such cases means safeguarding public health and complying with strict regulatory standards.
Without stringent quality control, businesses risk compromising their brand reputation, facing compliance issues, and losing customer trust. Therefore, understanding the quality control processes and implementing robust systems is crucial when partnering with third-party manufacturers.
Why Quality Control Matters in Third-Party Manufacturing
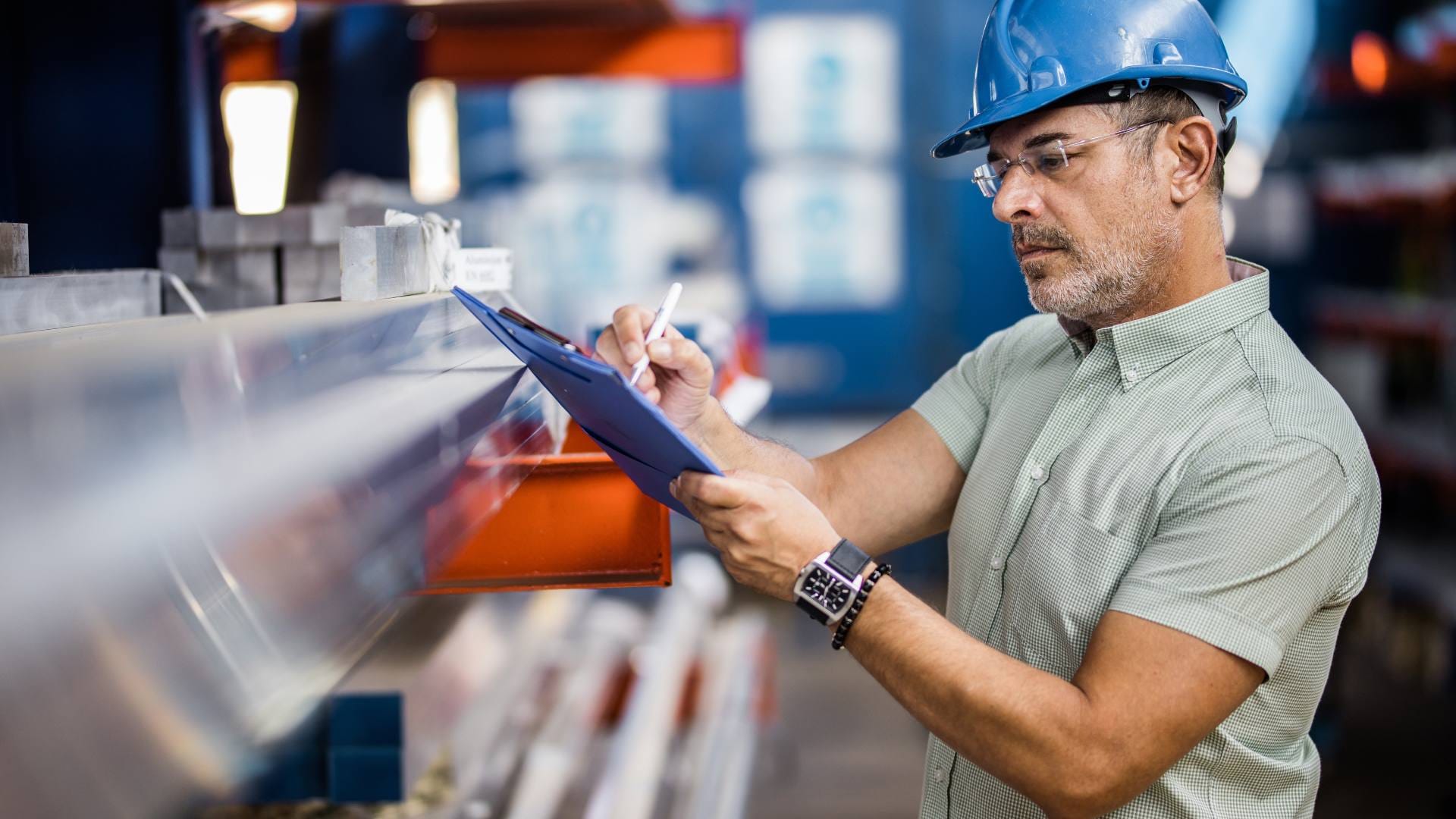
The stakes are high in outsourced production. A single defective batch can result in financial losses, regulatory penalties, and damage to your brand’s reputation. Consider the case of a food brand outsourcing snack production to a third party. If proper quality checks are not in place, contaminated products could reach consumers, leading to recalls and lawsuits.
Quality control ensures:
- Consistency in product standards.
- Compliance with industry regulations.
- Customer satisfaction and loyalty.
By prioritising quality control, businesses safeguard their investment and build long-term trust with consumers.
Key Elements of Quality Control
To ensure excellence, quality control in third-party manufacturing must cover these critical aspects:
a. Raw Material Verification
The quality of the final product begins with raw materials. Rigorous testing and certification ensure that only premium-grade materials are used. For instance, in the cosmetics industry, verifying that ingredients are ethically sourced and free from harmful chemicals is non-negotiable.
b. Process Monitoring
Regular inspections and real-time monitoring during production prevent deviations from the set standards. Advanced technologies like IoT sensors and AI analytics can enhance this process by providing real-time alerts for any discrepancies.
c. Final Product Inspection
Before products leave the facility, they undergo thorough inspections to identify any defects or inconsistencies. Industries like electronics have to ensure that every unit is tested for performance and safety before shipping.
Common Challenges in Quality Control
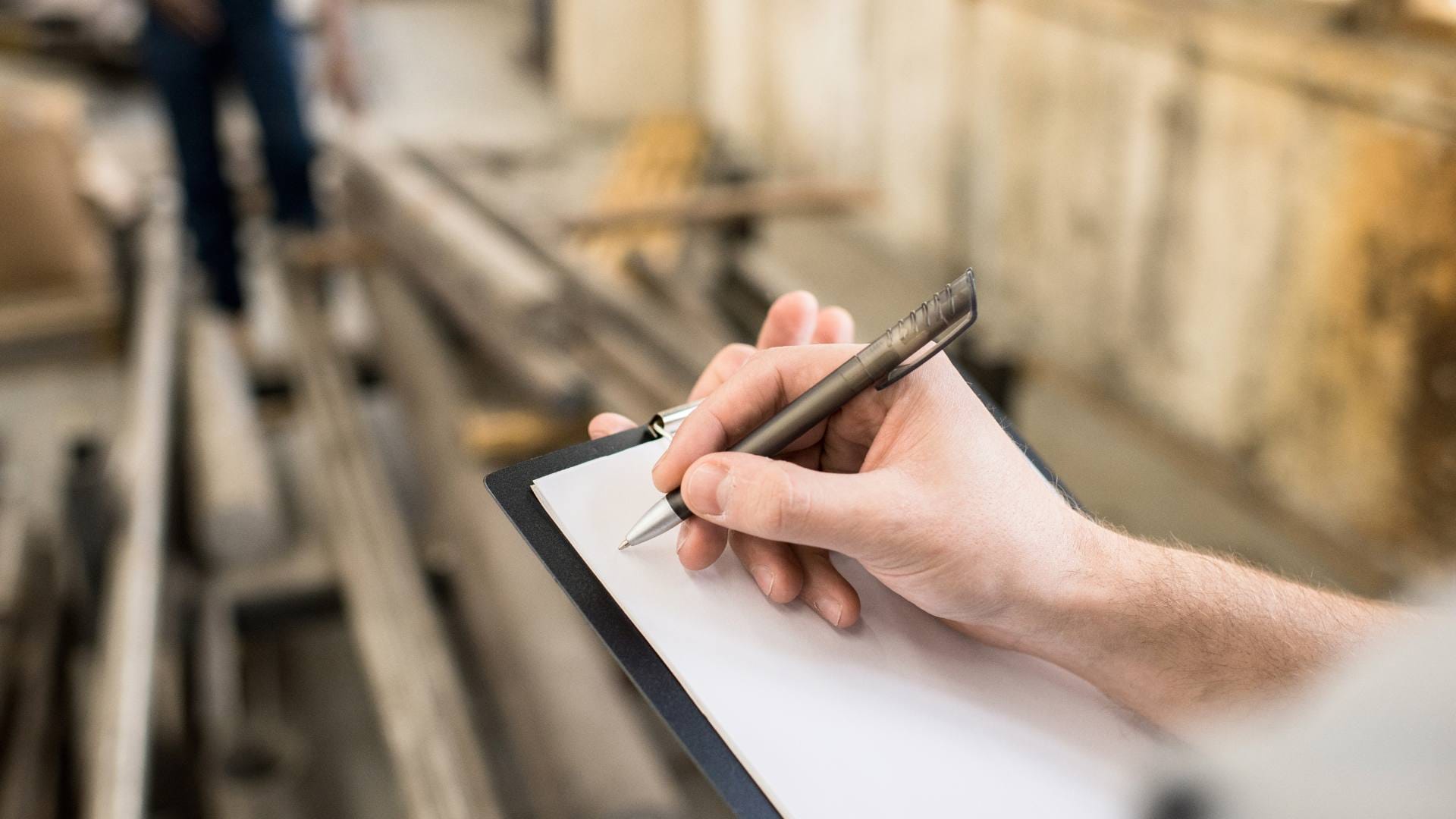
Despite its importance, ensuring quality control in third-party manufacturing isn’t without challenges. Let’s explore some common hurdles:
a. Communication Gaps
Effective communication between the client and the manufacturer is vital. Misunderstandings about specifications or standards can lead to errors. For example, a clothing brand might specify organic fabric, but a miscommunication could result in the use of synthetic materials instead.
b. Limited Oversight
Since the production happens offsite, businesses often have limited visibility into the manufacturing process, making it harder to enforce quality checks. Regular audits and third-party certifications can help bridge this gap.
Selecting the Right Manufacturing Partner
Choosing a reliable third-party manufacturer is the first step toward ensuring quality. Here’s what to look for:
a. Certifications and Compliance
Ensure the manufacturer adheres to industry standards like ISO, GMP, or FDA certifications, depending on your product category. Brands should ensure their partner complies with Good Manufacturing Practices (GMP) to keep their and the customer's values aligned.
b. Track Record
Check their history of delivering consistent quality and meeting deadlines. Client testimonials and case studies can offer valuable insights. Partnering with a third-party manufacturer with a proven track record can help reduce costs and boost production, resulting in the successful launch of their new product line.
OEM vs. Third-Party Manufacturing
When outsourcing production, businesses often choose between Original Equipment Manufacturing (OEM) and third-party manufacturing. While they may seem similar, these models differ significantly in operations and benefits. Here’s a detailed comparison:
Feature | OEM Manufacturing | Third-Party Manufacturing |
---|---|---|
Definition | Produces products under another company’s brand but designs and develops them. | Produces pre-designed products for a company’s brand. |
Control Over Design | High—clients retain control over design and specifications. | Low to medium—clients rely on the manufacturer’s existing designs. |
Cost | Generally higher due to customization and R&D. | More cost-effective as it leverages existing infrastructure. |
Lead Time | Longer due to custom design and development processes. | Shorter as manufacturers use pre-existing templates and processes. |
Customization | Full customization based on client needs. | Limited customization options. |
Responsibility | The OEM handles both production and design responsibilities. | Focuses solely on production based on the client’s design. |
Key Takeaways
- OEM Manufacturing is ideal for businesses seeking unique, innovative products tailored to their brand.
- Third-Party Manufacturing works best for companies focusing on cost efficiency and faster time-to-market.
Understanding these distinctions helps businesses choose the model that aligns with their goals and ensures effective quality control.
Implementing a Robust Quality Agreement
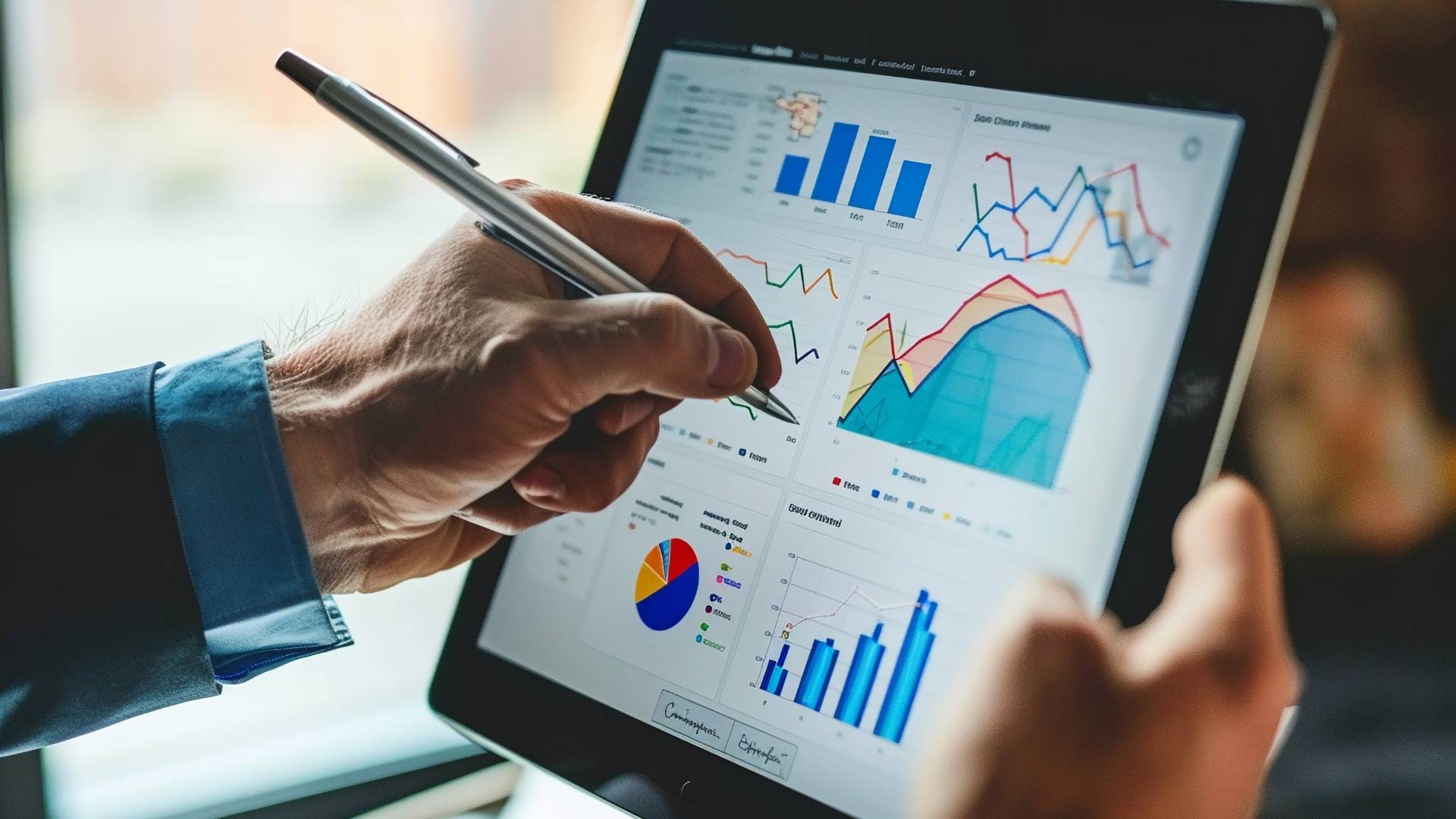
A well-defined quality agreement is a cornerstone of effective quality control. This document outlines the responsibilities and expectations of both parties, including:
- Testing protocols.
- Quality standards.
- Audit schedules.
For example, a pharmaceutical company might specify stability testing intervals and packaging material requirements in its quality agreement with a manufacturer.
By having this agreement in place, businesses can mitigate risks and ensure accountability.
Technology: A Game-Changer in Quality Control
Modern technologies have revolutionized quality control in third-party manufacturing. Here’s how:
a. Automation
Automated quality checks reduce human error and ensure consistency. For instance, automated optical inspection (AOI) is widely used in electronics manufacturing to detect defects in circuit boards.
b. Data Analytics
Advanced analytics tools can predict potential quality issues, enabling proactive measures. Predictive maintenance software in machinery can identify wear and tear before it affects production quality.
Regular Audits and Inspections
Audits are non-negotiable for maintaining quality in third-party manufacturing. Here’s why:
- Pre-Production Audits: Assess the facility’s readiness and capabilities. Verifying whether a factory complies with safety standards and provide an ethical work culture.
- Ongoing Inspections: Monitor compliance with agreed-upon standards during production. Random batch testing is common in the food industry to ensure quality.
- Final Audits: Verify that the finished products meet all quality criteria. For example, in the automotive sector, crash tests are conducted to validate safety standards.
Building Long-Term Partnerships
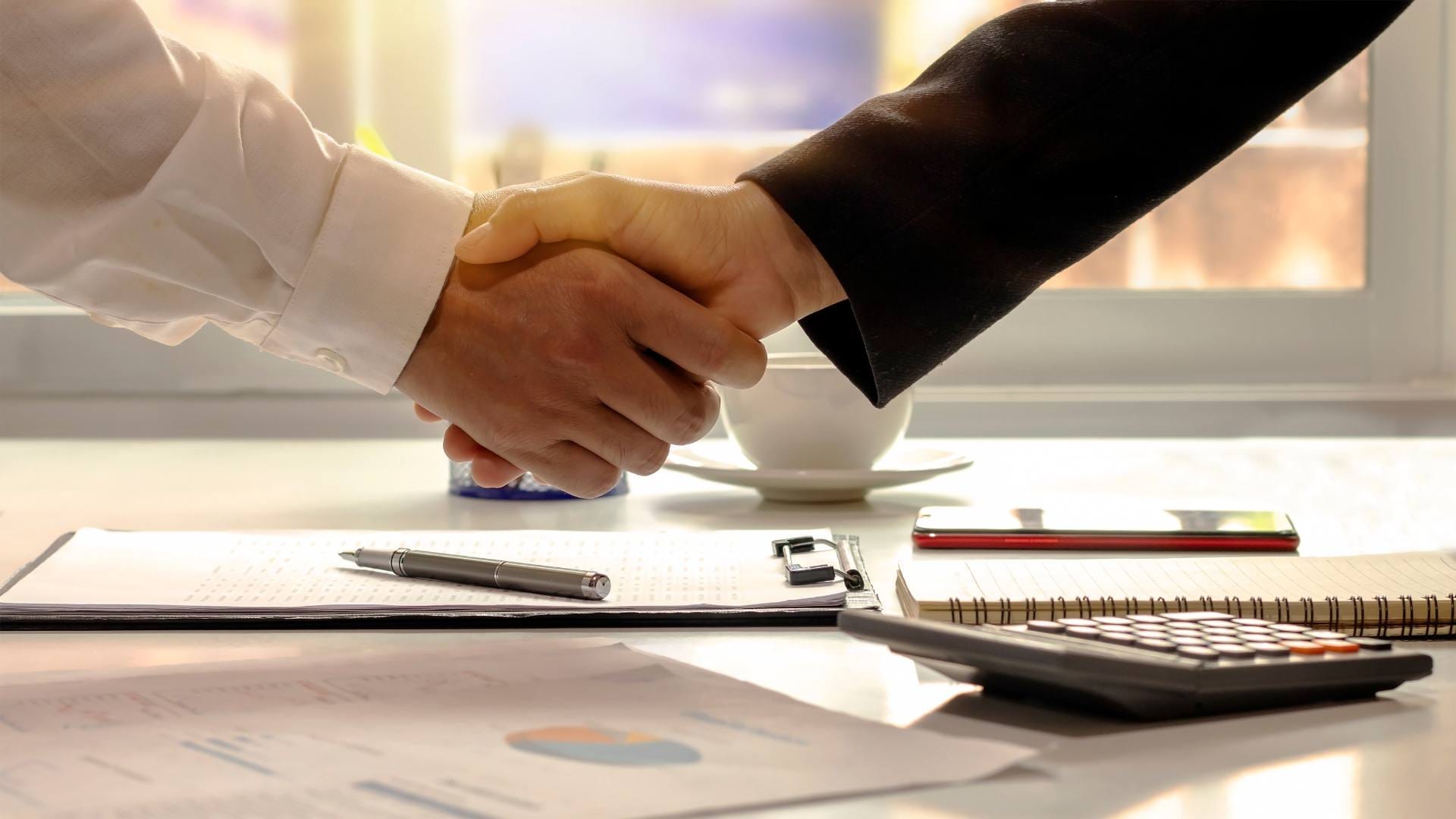
Quality control isn’t a one-time effort but an ongoing process. Building a strong relationship with your third-party manufacturer fosters collaboration and mutual commitment to quality.
a. Transparent Communication
Regular updates and open communication ensure alignment on quality expectations. For instance, using collaboration platforms can streamline communication and issue tracking.
b. Continuous Improvement
Work together to identify areas for improvement and implement solutions to enhance quality further. For example, adopting lean manufacturing principles can minimize waste and improve efficiency.
Conclusion
Quality control in third-party manufacturing is not just a requirement but a cornerstone of success. By understanding the processes, overcoming challenges, and leveraging technology, businesses can ensure their products consistently meet the highest standards.
Outsourcing production doesn’t mean outsourcing responsibility. With robust quality control measures, you can protect your brand, satisfy your customers, and achieve long-term growth.
Interested to learn more about quality control in your manufacturing process? Get in touch with us today and secure, track and verify your products in the factory, warehouse and in the market.