Compliance with industry-specific requirements is paramount in manufacturing as it ensures safety for produced products and prevents expensive fines. Labelling is a requirement companies must comply with in most industries, such as medicine, food products, and chemical supplies. Inline printing technology may offer a smooth avenue through which the manufacturers can maintain compliance; they present real-time printing capabilities so that every product contains labels that show what is current and accurate. Companies may integrate it into the system to avoid mislabeling, reduce waste, and ensure high operational efficiency.
Importance of Accurate and Clear Labeling for Regulatory Compliance
Control bodies like the Central Drug Standards Control Organization (CDSCO), Food and Drug Administration (FDA) and Conformite Europeenne (CE), among others, impose high standards on what is supposed to appear on the product labels to ensure public safety. Labels are appropriate in the conveyance of information concerning the ingredients of the product, such as when it should expire, how to apply it safely, and its proper use. Noncompliance because of error or omission will lead to product recall and harsh legal consequences.
For instance, the FDA has strict labelling regulations for drugs. This requires precise dosage and warning information to be provided to the consumer. Conformity with CE in Europe also makes labelling crucial since consumer goods and medical devices must meet expectations concerning safety and performance standards. Inaccurate labelling poses a risk to consumer safety, damages the brand reputation and inflicts heavy fines.
How Inline Printing Ensures Up-to-Date Labeling for Perishable Goods, Chemicals, and Pharmaceuticals
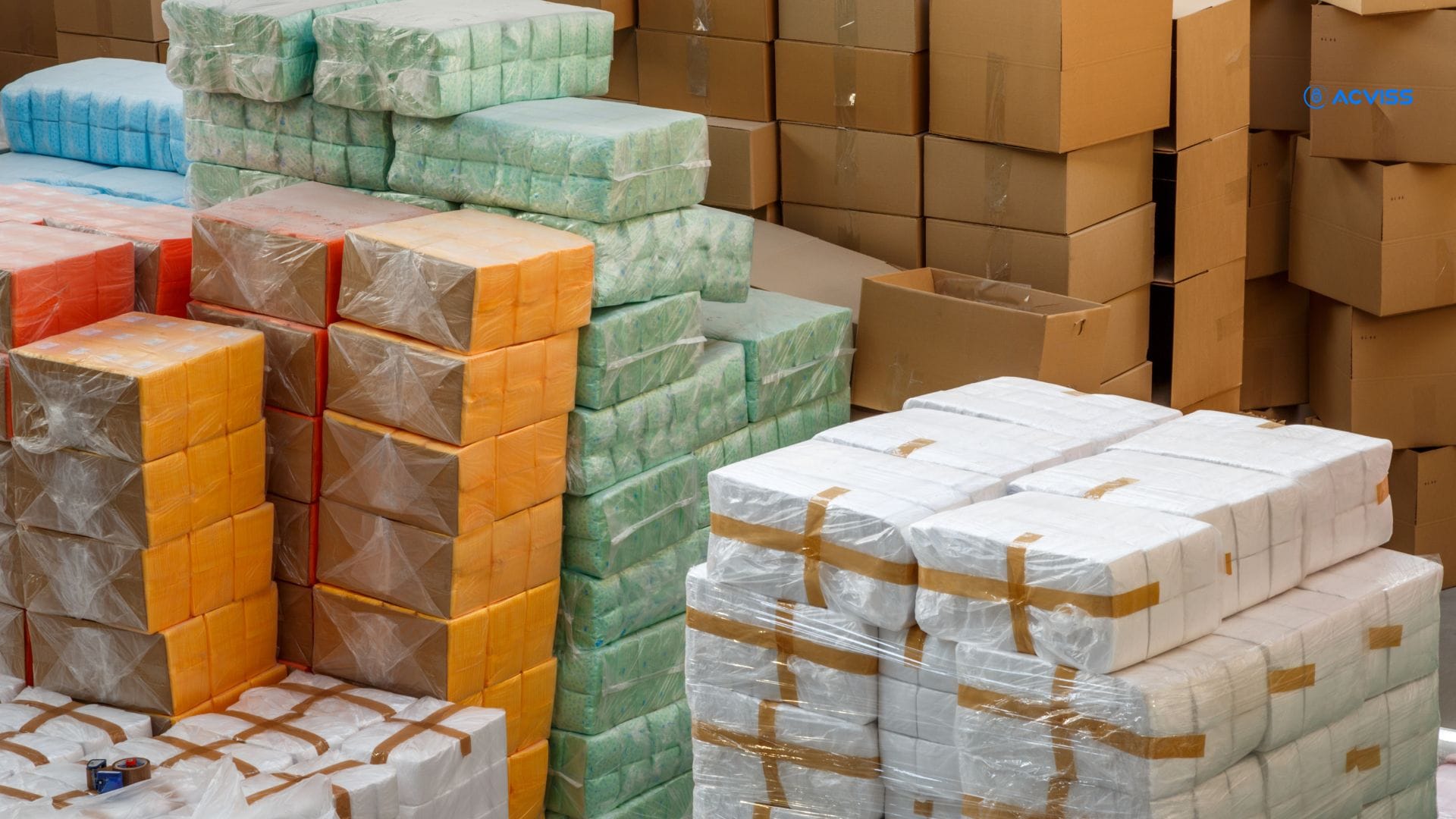
1. Real-Time Updates for Perishable Goods
In the food industry, the shelf lives of perishables often have to be very short. Labelling the date of expiration, batch number, and directions for storage accurately is also critical. Inline printing allows manufacturers to update labels in real-time so that information about the specific product can be printed onto each one as it comes off the line. This minimizes the occurrence of obsolete labels and declines the formation of waste associated with poor packaging, thus enhancing firm compliance with food safety regulations such as the FDA and EFSA.
2. Chemical Industry Compliance
The chemical industry has more specific laws regarding labelling under systems such as the Globally Harmonized System of Classification and Labeling of Chemicals (GHS). Labelling ensures communication of hazard warnings, instructions for handling, and the chemical composition. Inline printing systems easily cater to this without a hitch since they provide real-time label updates, which can be hazard class changes or new safety data. This flexibility is essential in the present scenario of changing regulatory policies. It keeps users away from expensive recalls and penalties.
3. Pharmaceutical Industry Regulations
This is important in the pharmaceutical sector because of the accuracy of labelling to ensure patient safety and conformity with regulatory agencies, such as the FDA and the European Medicines Agency (EMA). Precise dosing is required in the pharmaceutical industry for labelling instructions on dosage, expiration date, and manufacturing details. Inline printing ensures pharmaceutical manufacturers can update labels when new regulatory guidelines are issued or product formulations change. This also prevents mislabelling, which can otherwise lead to hazardous effects on consumers or delayed product shipments due to non-compliance. Serial numbers printed for every batch are another method of supply chain traceability and also facilitate compliance with anti-counterfeit standards.
4. Cost Savings and Reduced Error
Traditional pre-printed labelling can waste several types of labels in bulk when information changes, as entire batches of labels need to be replaced. On the other hand, inline printing offers an on-demand solution, cutting down on inventory costs and reducing errors by directly printing what is needed exactly when it is required. This leaves little room for mislabeling because of human error or outdated label stock, ensuring each product leaves production meets the most recent requirements.
5. Flexibility and Scalability
The inline printing systems are very flexible and can be included in most production environments, from low to high levels of production and industry. This flexibility ensures that manufacturers from all industries can increase or change the scale of their labelling processes to meet increasingly growing orders or adjust to changing compliance requirements without having to dismantle what they already have in place.
Case Studies
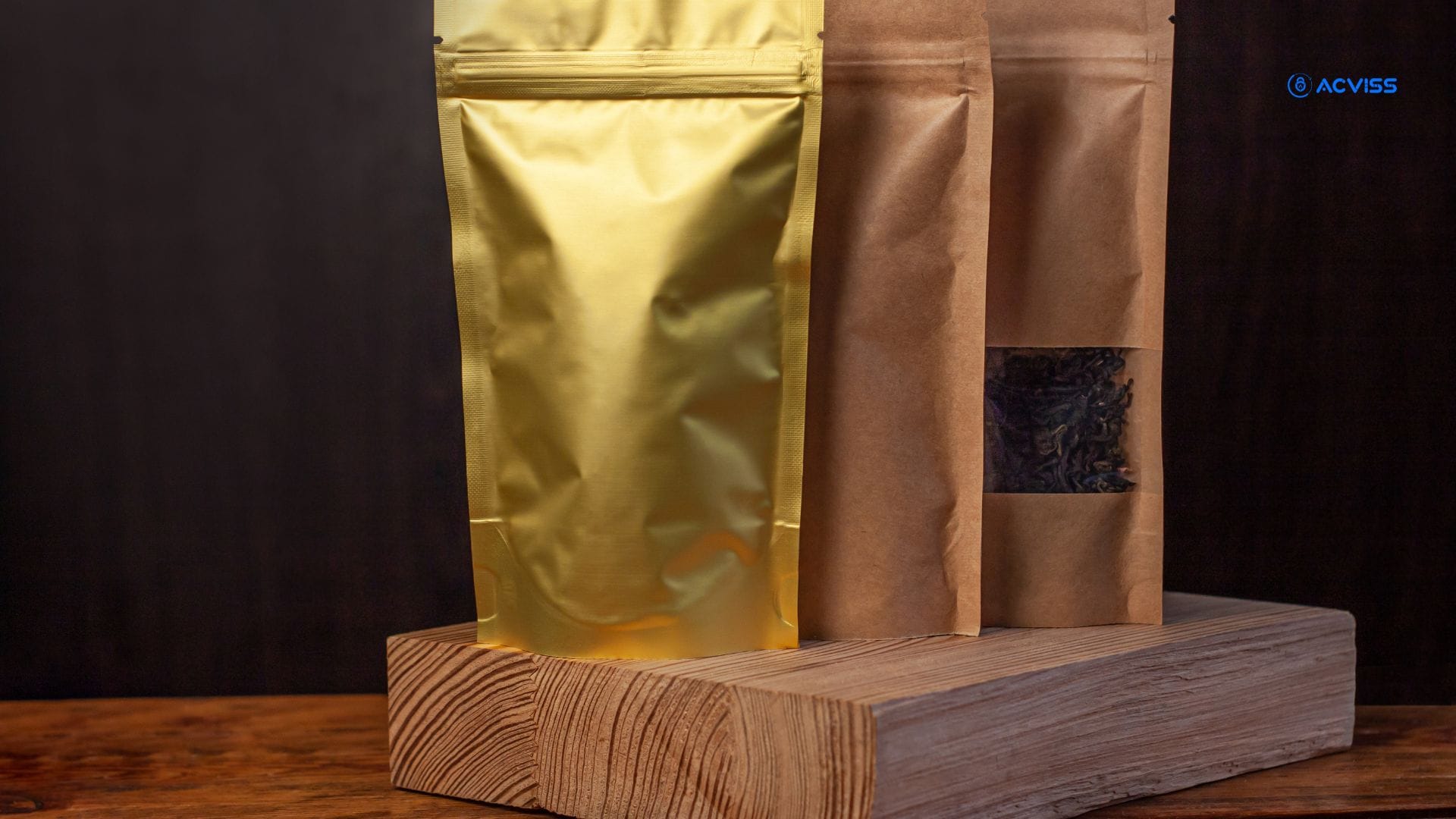
1. Food Production
A leading FMCG company was suffering from label changes from time to time due to changes in ingredient formulation and new safety standards. The brand was able to reduce the time and cost incurred while relabeling by adopting inline printing technology in production. This helped to deliver real-time updates, so every product would be ready after timely compliance with FDA and EFSA regulations. The manufacturer cut down the error rate by 20% in labelling and increased the efficiency in production.
2. Pharmaceuticals
One pharmaceutical company that produced over-the-counter drugs had to abide by the FDA's stipulations of continuous expiry dates and dosage changes. Inline printing meant that the company could affix a direct label to its package at the production point, ensuring that every pack contained the latest available information; this nullified part of expensive recalls resulting from wrong labelling and ensured compliance with regulations improved rapidly.
3. Chemicals Industry
One of the major chemical companies needed precise product labelling to meet GHS compliance regulations. The clients used pre-printed labels, which became outdated if specific regulations were updated causing inventory problems. Inline printing allowed the company to update hazard warnings and product specs in real time to maintain GHS compliance. As a result, waste was reduced by 15% and flexibility in operations improved.
Adapting to the Changing Landscapes
Inline printing is effective to adapt to the changing regulatory landscape and combined with an anti-counterfeiting solution like Origin ensures product safety and supply chain traceabiltiy. The real-time labelling solutions are flexible as well as cost-effective by allowing every item to get correctly and immediately printed information. Implementing inline printing enables manufacturers to avoid hefty penalties, minimize wastage, and achieve better operational efficiencies, making it easier to comply with even the strictest regulations.
If you are interested to learn more about Inline printing and product traceability solution, get in touch with us. Join the ranks of global leaders and implement anti-counterfeiting solution that secures your brand and supply chain across the globe.