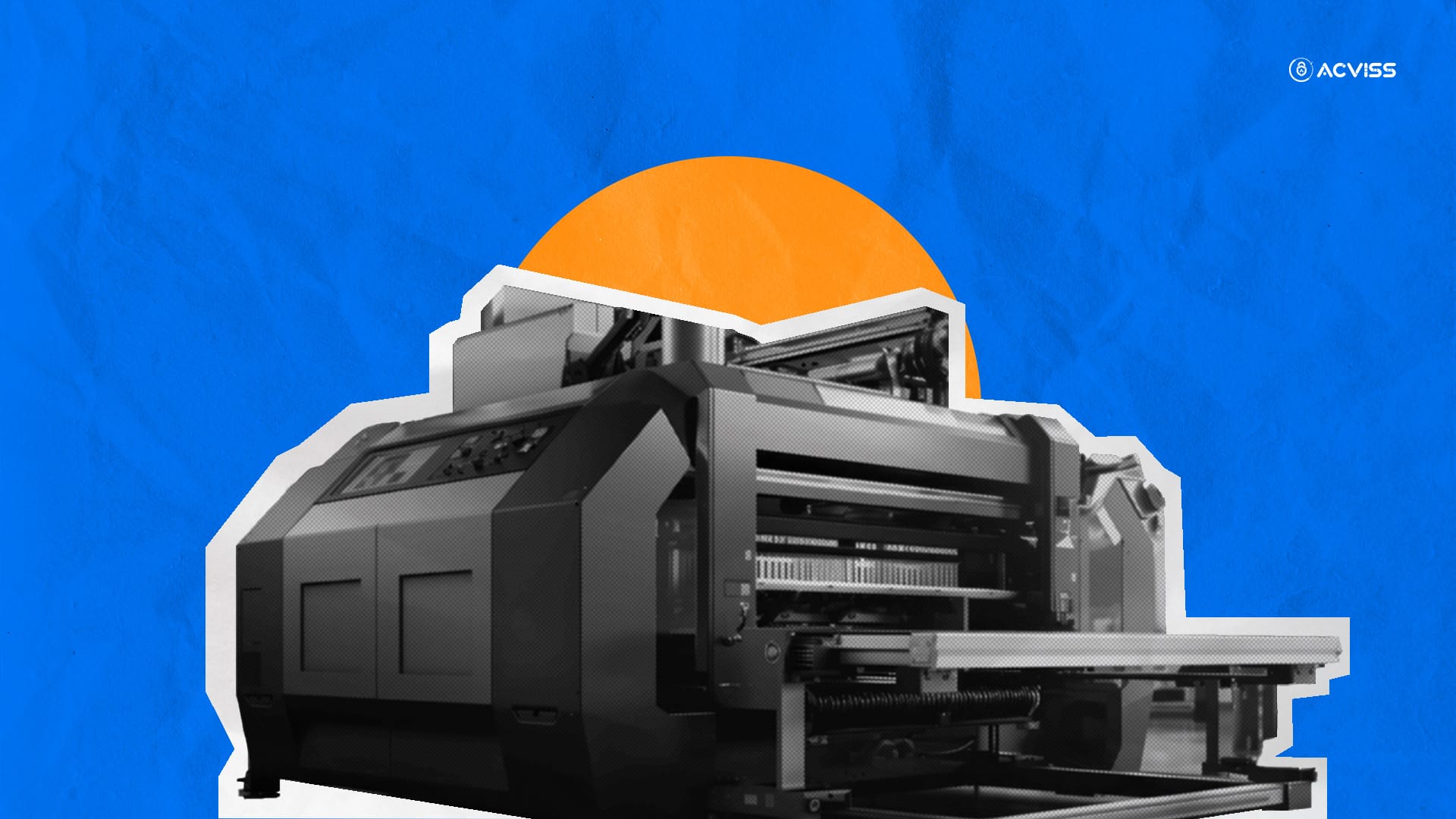
Inline printing is the most effective way to apply details directly onto products during production. It allows real-time customisation and removes the need for pre-printed labels. But, to use it fully, proper setup, maintenance, and quality control are necessary. Following the right practice will improve efficiency, reduce costs and ensure stable print quality, even in high-volume production runs.
Practical Tips for Setting Up Inline Printers
If you want to ensure smooth integration with the production process, you need to set up in–line printers with strategic planning. For seamless operation, proper positioning, system compatibility, and calibration are essential. Considering these aspects will ensure that the printer delivers consistently and with better productivity.
Some of the practical tips are:
- Choosing the Right Technology – Finding the right printer for your needs is essential. Consider factors like substrate materials, speed of the production line and print quality requirements. For high-resolution text, common technologies like thermal inkjet and for high-speed applications CIJ is used, and laser for non–smudging and permanent marks.
- Positioning Matters – Place the printer in a place where it can easily print on the product as it moves along the line. For consistent and clear printing, the printer must be placed optimally. Avoid placing it in places prone to excessive dust and vibrations as these can damage the print quality.
- Implementing Existing Systems – Maintegrates well with your current software and equipment. It must be able to communicate with your production management systems to extract the data automatically, like as real-time printing, expiration dates, and batch numbers.
- Regular calibration – To make printers produce the correct print size and position, you need to calibrate it. Make use of test runs before beginning huge production batches to verify print quality.
- Plan for scalability – the inline printing setup must be able to handle huge volumes as production demands increase. Ensure the printer can be supplemented or ungraded with additional units to match growing demand.
Must Read: Enhance Productivity with PDA Systems on the Manufacturing Shopfloor
Maintenance Tips for Inline Printing Equipment
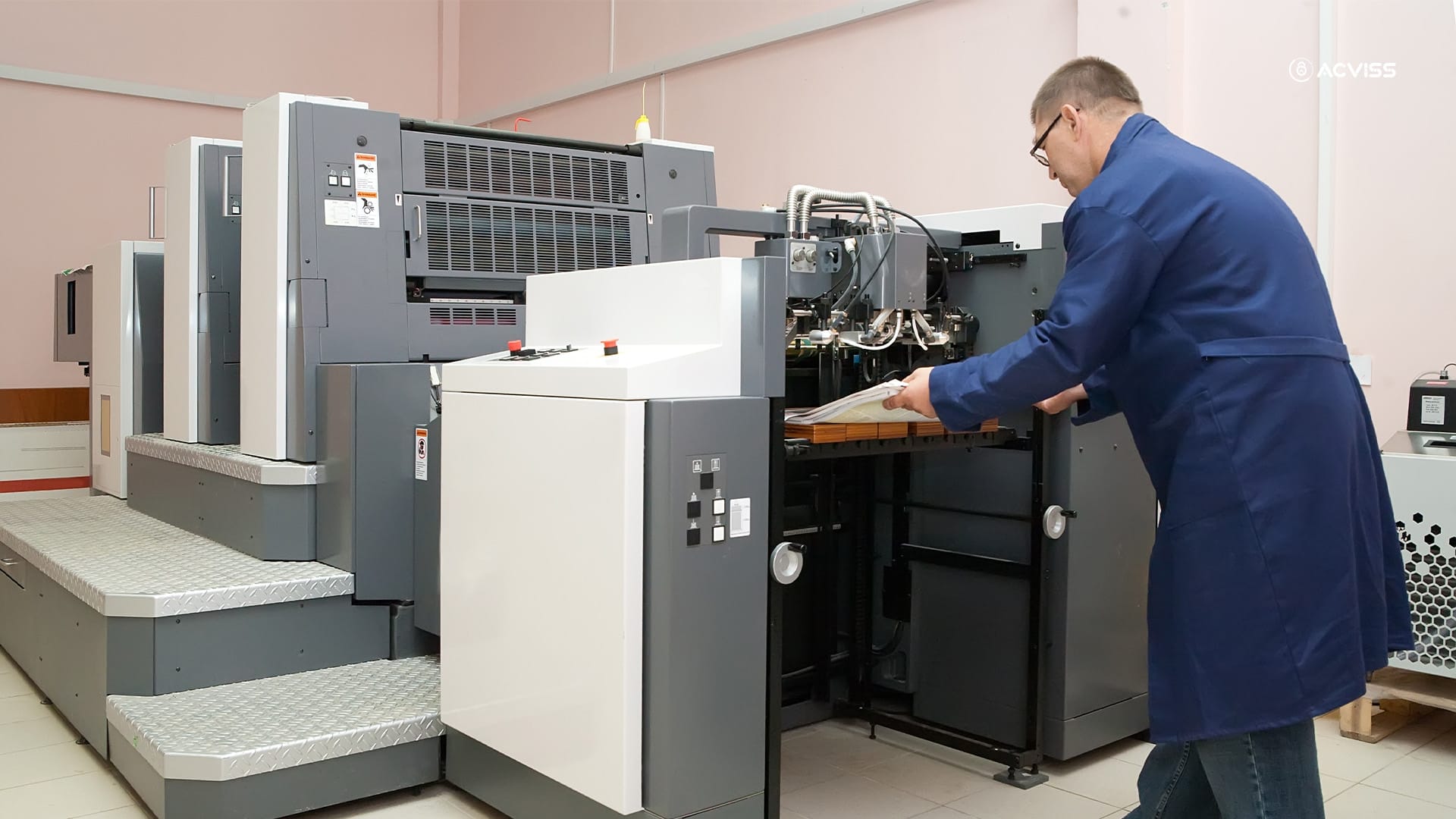
For reducing downtime and ensuring continuous high–quality production, maintaining inline printing equipment is essential. Some of the common issues like printhead blockages and ink spillage can be avoided with regular care. Following a maintenance routine will prolong the life of your printer and enhance overall efficiency.
- Routine cleaning – Dust, dirt, and debris cause printheads to malfunction or clog. You need to clean the printheads and sensors regularly as per manufacturer guidelines. For inkjet printers, this might include flushing the system with cleaning solutions to remove dried ink.
- Inspecting regularly – it is essential to identify any signs of wear and tear. Look for problems like nozzle blockages, alignment issues, or ink buildup. Finding these early will prevent expensive downtime.
- Replacing consumables on time – Track the levels of consumables such as cartridges, tone, and ink. Running out during production might lead to poor quality and delayed printing. Use genuine parks and ink suggested by the manufacturer to avoid equipment damage.
- Software updates – Make sure your printer’s software is up to date. Manufacturers often release updates that enhance functionality, fix bugs, and enhance performance. This helps the printer operate at its best and lowers the risk of errors.
Ensuring Quality and Consistency in Print During High-Volume Production Runs
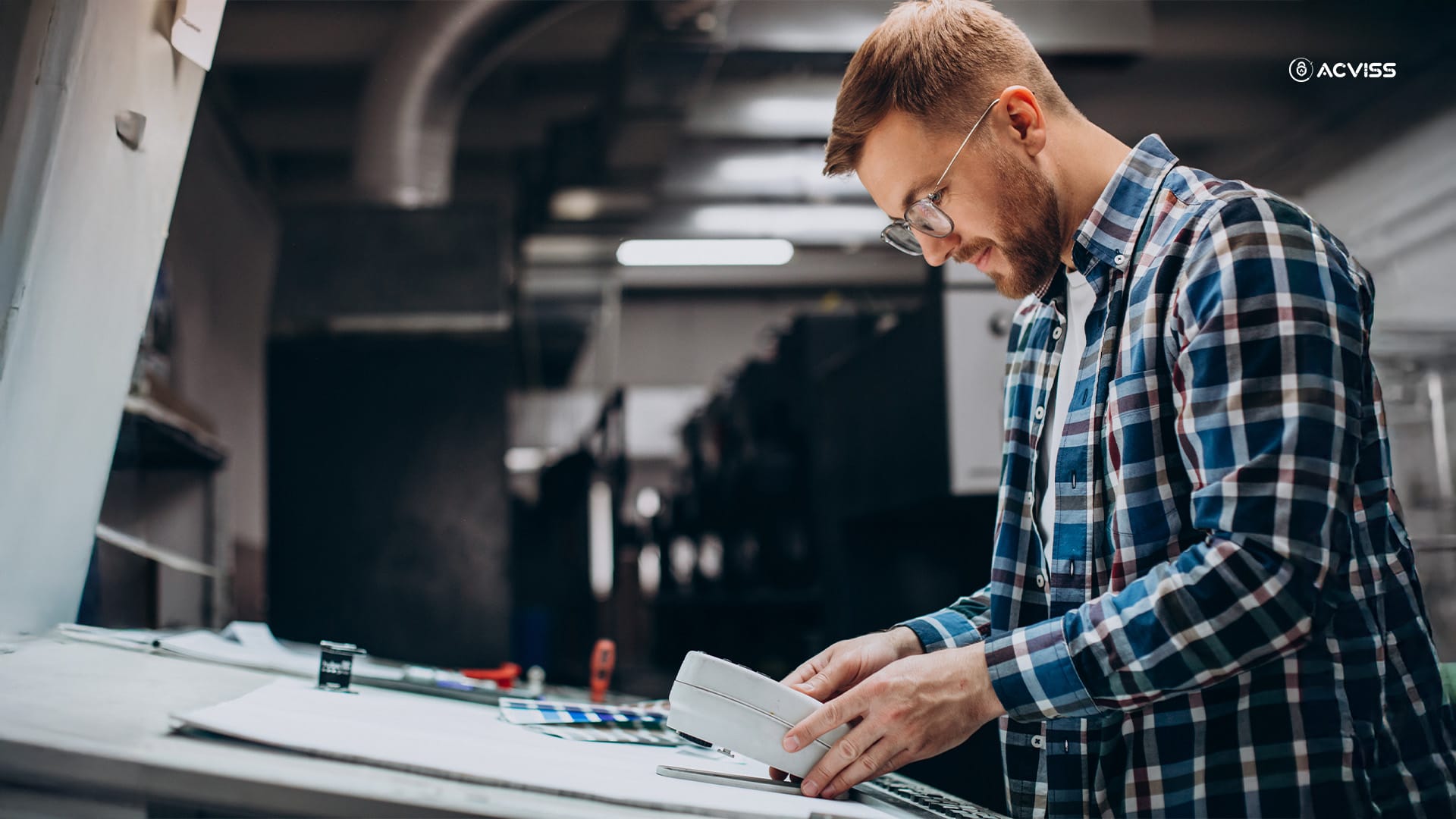
Maintaining consistent print quality can be tiresome when running high–volume production. Factors like environmental conditions, speeds, and material type can affect the results. Some of the effective strategies to make sure that print consistency is maintained throughout large–scale production runs are;
- Optimising the Print Speed: Balance between print quality and production speed. While high–speed printing is needed for fast-paced environments, pushing the printer to run fast might result in poor–quality prints. Which can result in incomplete and smudging text. You need to test the speeds to find the right spot where both print quality and efficiency are maintained.
- Use High-Quality Consumables: Use only high-quality ink toner and print media crafted for your inline printer. Low-quality consumables might lead to inconsistent prints, fade, and smudge over time. Ensure to use only quality materials that are suitable for the environment as well.
- Monitor Print Quality: Set up cameras and sensors to inspect the print automatically. This system can notify operators swiftly if it detects fading or misalignment. Automated quality control systems can help catch issues early and lessen waste.
- Consistent Calibration Checks – You need to have an eye on the calibration settings, especially during high–volume runs. Temperature changes. Physical environment or humidity can affect the print clarity and alignment. Make use of SOP for recalibrating printers after a specific number of units have been made.
- Operator Training – Make sure operators are well–trained in both troubleshooting common print issues and with the equipment’s functionality. They must know how to adjust settings on the fly to stay away from prolonged disruptions during a production run. A well–trained team can swiftly identify and solve the issue that might impact the print quality.
For Long-Term Growth
Implementing inline printing on your shopfloor can greatly increase its efficiency, enhance product traceability, and reduce cost. But, to ensure its long–term success, it is essential to follow the right practices for setup, maintenance, and quality control. An active approach to training and troubleshooting will also help you avoid costly downtime, making sure the inline printing systems work effectively and smoothly.
Choosing the right partners to guide you through the process is important. Get in touch with our expert today and learn more about leveraging inline printing to implement a seamless anti-counterfeiting strategy for your brand.