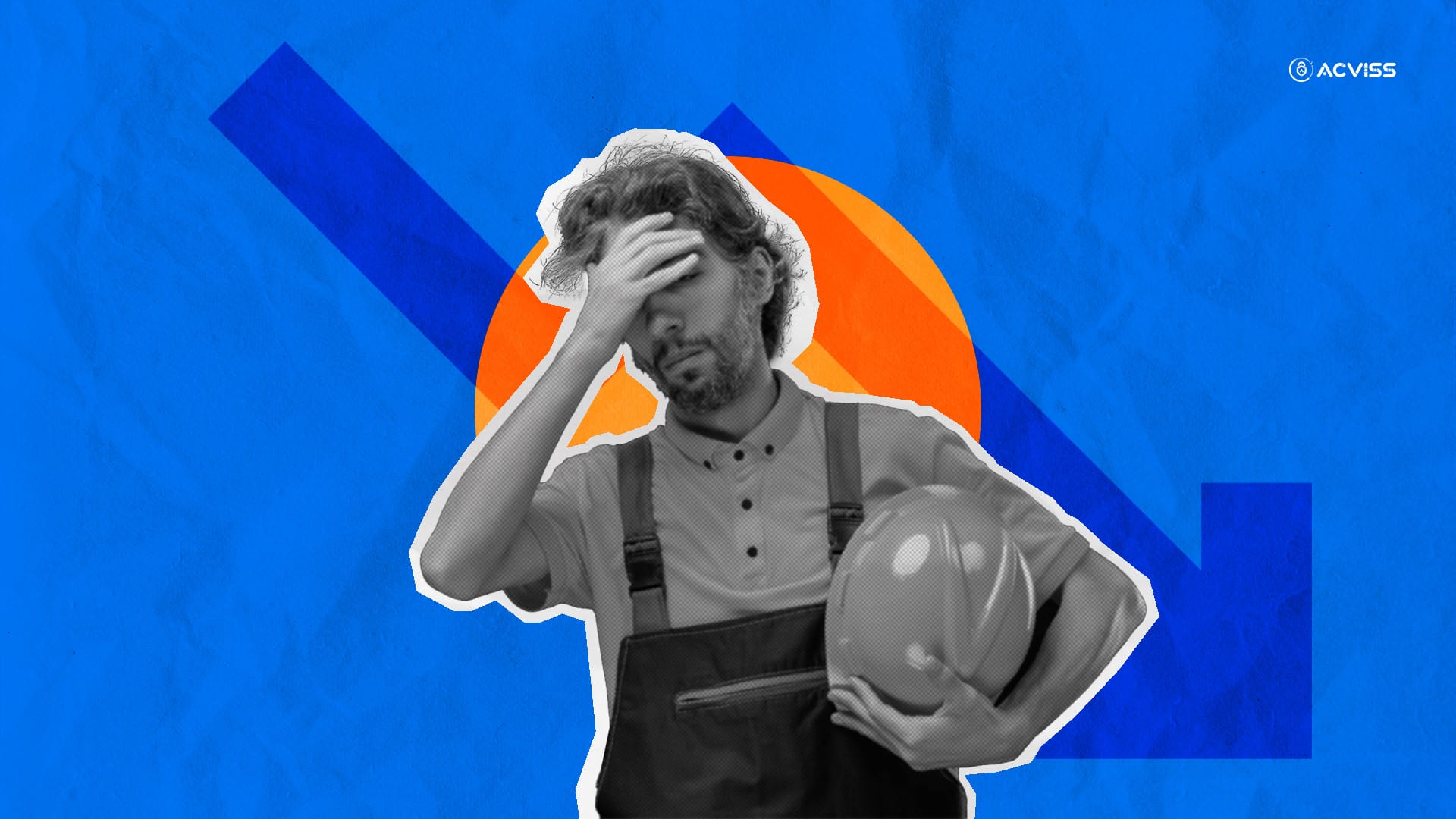
Offshore competitiveness and persistent supply chain shortages are just two of the many issues facing the US manufacturing industry. The lack of workers is currently one of the biggest challenges facing manufacturers. Every level of expertise is needed for advanced manufacturing operations, although many find it difficult to find and keep qualified candidates.
To overcome these obstacles, manufacturers are increasingly using a range of tactics. Although more funding has been allocated to education and other initiatives to address the skills gap as a result of recent laws in the US and overseas, the results of these efforts won't be seen for years. Manufacturers may now take action to create more robust and resilient teams thanks to these initiatives. Most importantly, anti-counterfeiting measures have to be in place to ensure customer satisfaction - the end result of every production.
Wage Growth in A Competitive Market
Due to the persistent labour shortage that affects companies of all sizes, wages have been a major topic of discussion in the public sphere. Wages in the industrial sector have always been competitive for workers with varying degrees of education and experience. Nevertheless, there is now more pressure on many enterprises to raise their offers in order to compete in the labour market.
Hourly wages in the manufacturing sector have clearly increased, according to data from the US Department of Labour. Over the past year, hourly wages have risen by 2.7%, and in the fourth quarter of 2022, they are expected to rise by 3.2%. Even though labour productivity has decreased by 1.5% over the past year, these gains have resulted in higher labour expenses per unit.
Labour Shortage - a pertinent issue
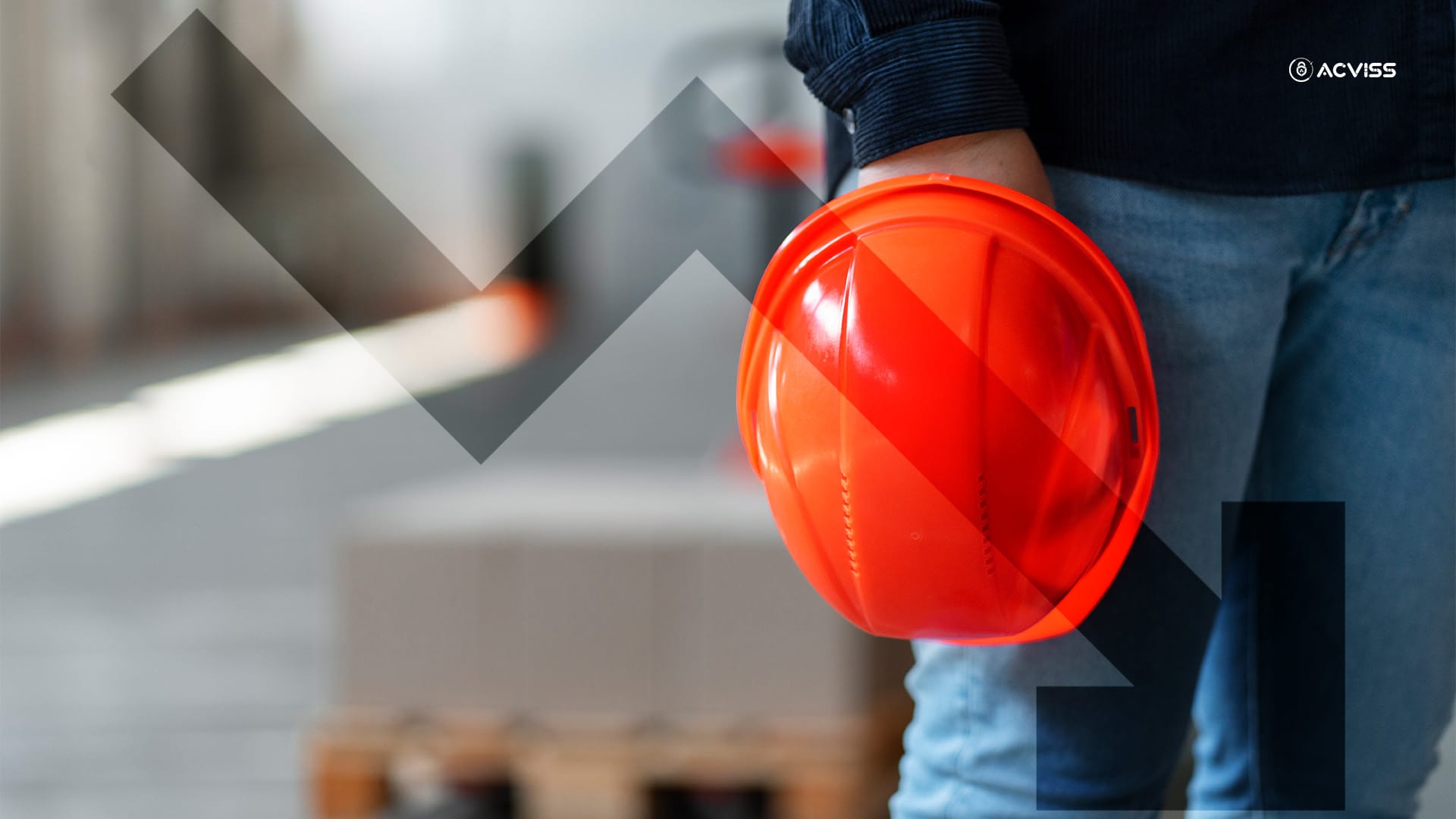
For practically all manufacturers, labour is the second most expensive component after raw materials. If manufacturers are unable to employ their human resources effectively and efficiently, raising pay is a major obstacle to overcome.
Personnel must be on-site in even the most highly automated production operations. Operators, technicians, and other professionals perform essential services that necessitate hands-on contact with equipment and goods. With so many remote work options in other industries, manufacturing is having trouble luring fresh candidates.
Manufacturers, however, have numerous chances to allow for a hybrid workplace culture and, in certain cases, completely remote employment. Technology in manufacturing enables better remote visibility and control. Authorised staff from any location can access real-time production data with a secure cloud solution.
For the foreseeable future, many jobs in the manufacturing sector will still demand hands-on experience. Nonetheless, manufacturers may address one part of the labour crisis by making certain professions more competitive by utilising technology to establish hybrid work cultures when feasible.
There are several reasons for this ongoing shortage:
- Ageing Workforce: As a large number of highly qualified manufacturing workers get closer to retirement age, they are leaving behind important knowledge and expertise.
- Skills Gap: The skills of the available workforce do not match the skills needed due to the rapid improvements in technology.
- Perception Issue: A lot of younger workers don't want to work in manufacturing because they think it's an old or unappealing job choice.
- Emphasis on Education: Potential workers have been drawn away from technical education and vocational training, which are essential for manufacturing positions, in favour of four-year college degrees.
- Competition From Other Sectors: Talent who might otherwise seek professions in manufacturing is frequently drawn to industries like technology and healthcare.
- Demographic Shifts: Variations in immigration trends and population dispersion have impacted the labour pool that is available in conventional manufacturing hubs.
Upskilling Current Employees

Retaining an existing employee is preferable to hiring a new one. Your staff is composed of knowledgeable workers who have become familiar with your business and operational procedures, which has increased their effectiveness and efficiency.
Even while hiring new staff is a constant struggle, manufacturers shouldn't undervalue their current workers. One of the best methods for manufacturers to invest in their current staff and achieve noticeable improvements in their operations is through upskilling. Giving their seasoned team members the required education and training guarantees that they will continue to produce at an exceptionally high level as manufacturers continue to implement new procedures and technology.
This can be done by providing general training for all positions in your company or by helping people develop their own special set of abilities. Upskilling might involve supplying the education and training experienced workers require to assume new responsibilities as well as addressing internal gaps higher up in your company.
Needless to say, the highest expertise level of employees helps them come up with the best quality products, which helps them be the pioneers in issues related to anti-counterfeiting.
Rather than hiring from outside, you can cut down on onboarding time and expenses by relying on staff members who are already familiar with important components of your business. It also makes sure that your team has a variety of viewpoints on your operations, which allows them to contribute even more.
Automating Processes to Reduce Manual Work
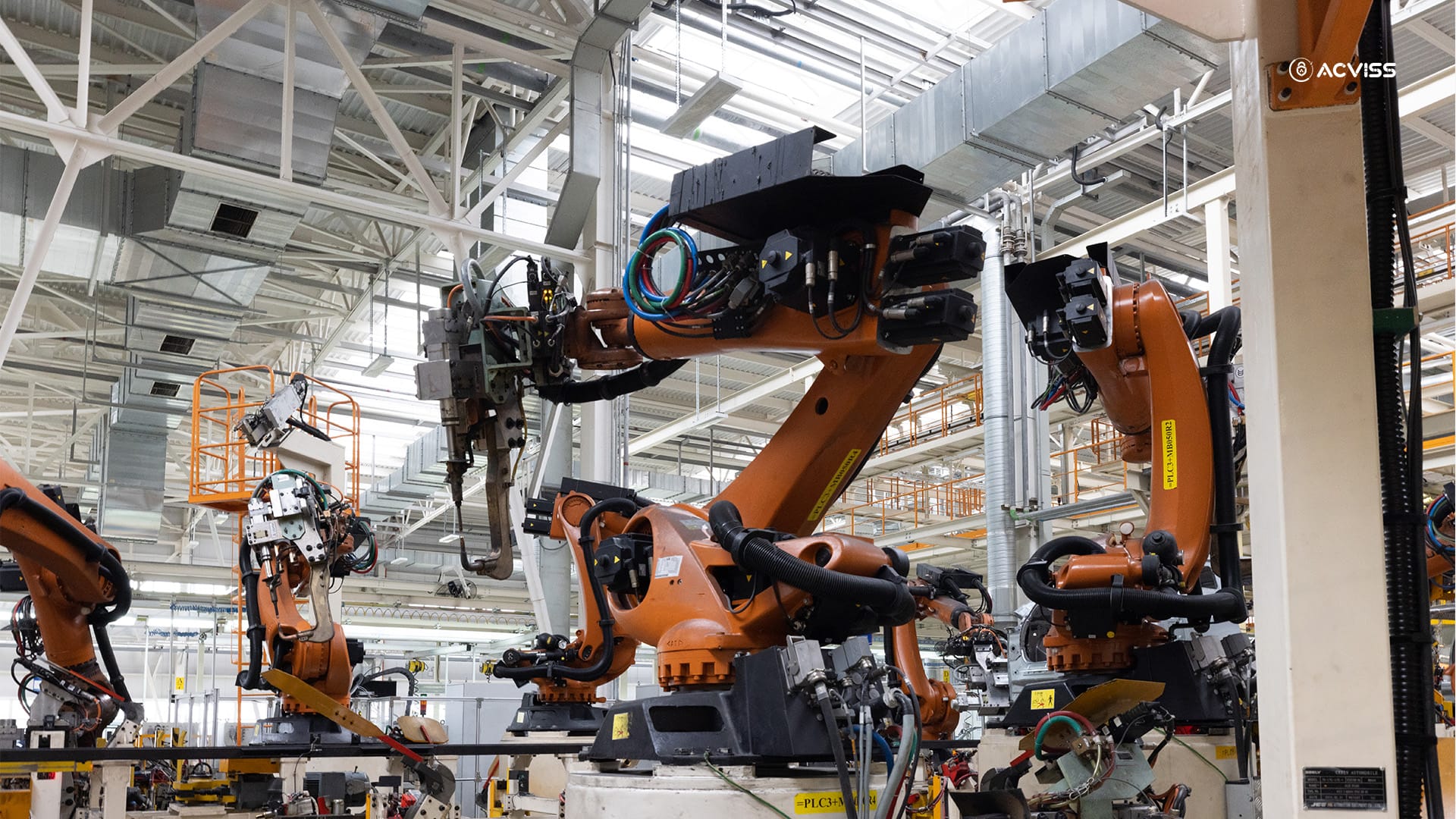
Creating a trained workforce is a major priority for both lawmakers and manufacturers. But automations like AI and ML in manufacturing are also essential for reducing the labour shortage. Numerous levels of automation are currently widely used in manufacturing, and Industry 4.0 technology is opening up even more possibilities.
Introducing State of the Art Automation: Various forms of automation have long been employed in manufacturing operations to lessen the need for manual labour and oversight. The first programmable logic controllers (PLCs), a technology still widely used today, emerged in the late 1960s, marking the beginning of what most people would consider modern automation.
The proper implementation of automation can lower the total amount of labour needed. Modern technologies have made it possible to manage many forms of control, monitoring, and inspection without the need for direct human involvement. The overall labour required is significantly lower, even if trained operators and technicians are still needed.
Providing Advanced Manufacturing Tools to Empower Teams
A new trend in advanced manufacturing has evolved, yet automation remains a key component of manufacturers' solutions to the labour problem. Modern production tools are being used to empower and enhance human resources rather than to replace or reduce them with machines.
Inventory Management
- One example is the increased visibility and transparency provided by industry solutions for inventory management. Production teams and management can gain valuable insights from the real-time consolidation and analysis of critical process data by using the appropriate solution. In contrast to the comparatively low-value work of manual data aggregation, they can then concentrate their attention on decision-making and implementation.
Initiating Seamless Workflows
- Additionally, competent workers can more precisely and efficiently navigate workflows with the aid of the appropriate technologies. Every level of planning and decision-making is facilitated by the ability to schedule and manage operations using a single platform with clear insight into the effects of any changes.
Real-time Operational Intelligence (RtOI) from Matics gives manufacturers the resources they need to empower their employees. Then there are task management solutions to help a team perform better and cut down on time spent on manual data collecting, monitoring, and analysis.
Tackling Challenges with Innovation and Integrity
The manufacturing industry faces significant challenges, from labour shortages to rising competition. Overcoming these requires a dual focus on workforce upskilling and advanced automation. By empowering teams with cutting-edge tools and technology, manufacturers can boost efficiency, uphold product quality, and reinforce anti-counterfeiting measures, ensuring customer satisfaction and long-term success in a competitive market.
Interested to know more about optimising your manufacturing process for maximum results? Get in touch with us today