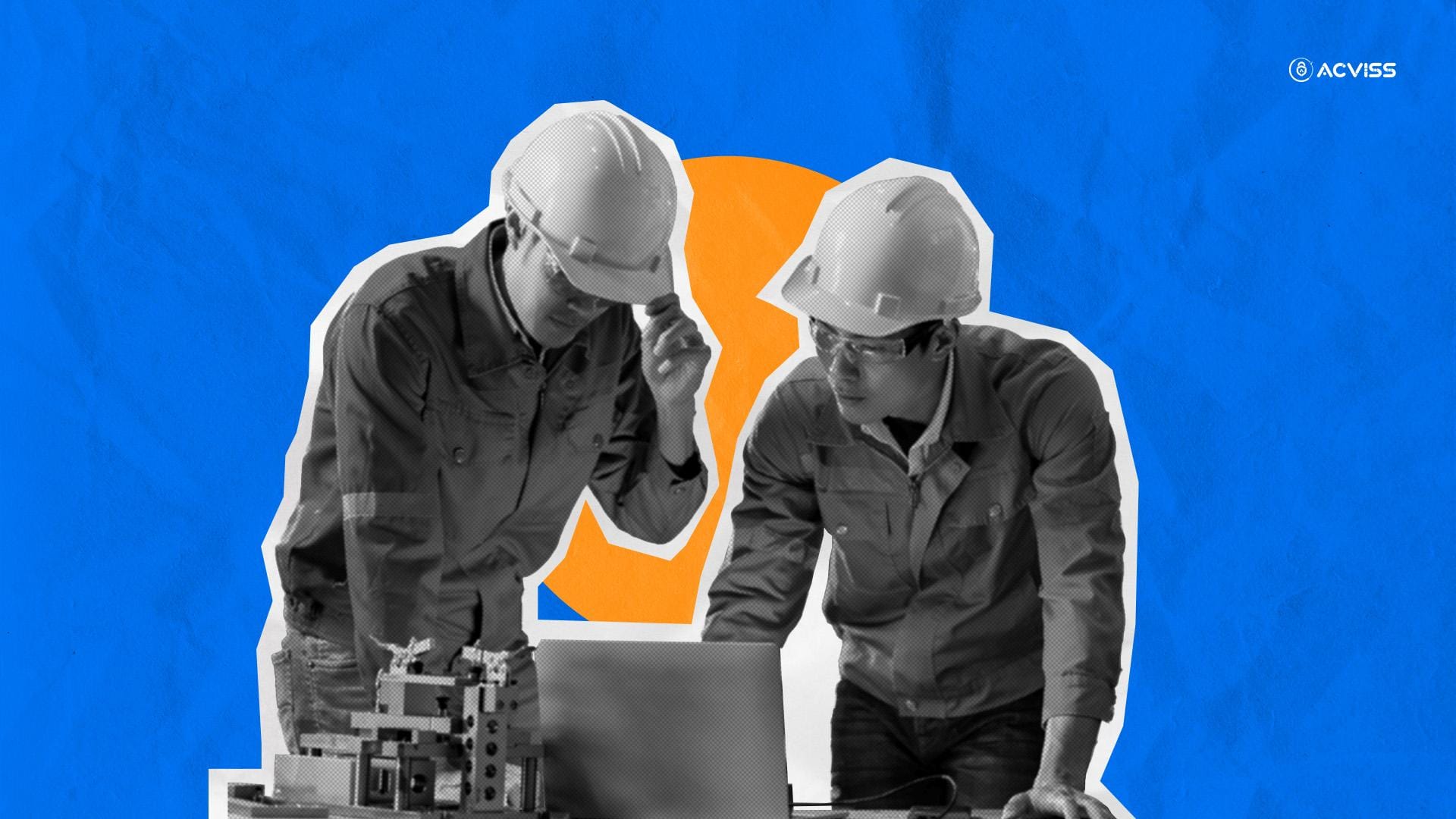
Before a regulated product reaches the market, there’s a decisive checkpoint that manufacturers must pass: proving that their production process can reliably deliver consistent, high-quality output at scale. This checkpoint is defined by the use of Process Performance Qualification (PPQ) batches.
PPQ is not just another procedural requirement. It is the definitive stage in process validation that confirms whether a process is ready for routine commercial use. These batches are produced using commercial-scale equipment, trained personnel, and under the same operating parameters intended for full-scale manufacturing. The aim is to confirm that the process performs reliably and reproducibly, meeting all pre-established criteria.
What Exactly Is a PPQ Batch?
A PPQ batch is produced during the second stage of process validation. Stage one focuses on process design, figuring out how the product should be made. PPQ is stage two, where you put the design into action under real manufacturing conditions.
During this stage, you make a specific number of consecutive batches, often three, but the number can vary based on risk, while closely monitoring every step. You're looking to confirm that the process performs as expected, not just once, but consistently. Parameters like temperature, mixing speed, timing, pressure, and pH are tracked in detail, alongside product quality attributes.
The Strategic Objectives of PPQ Batches
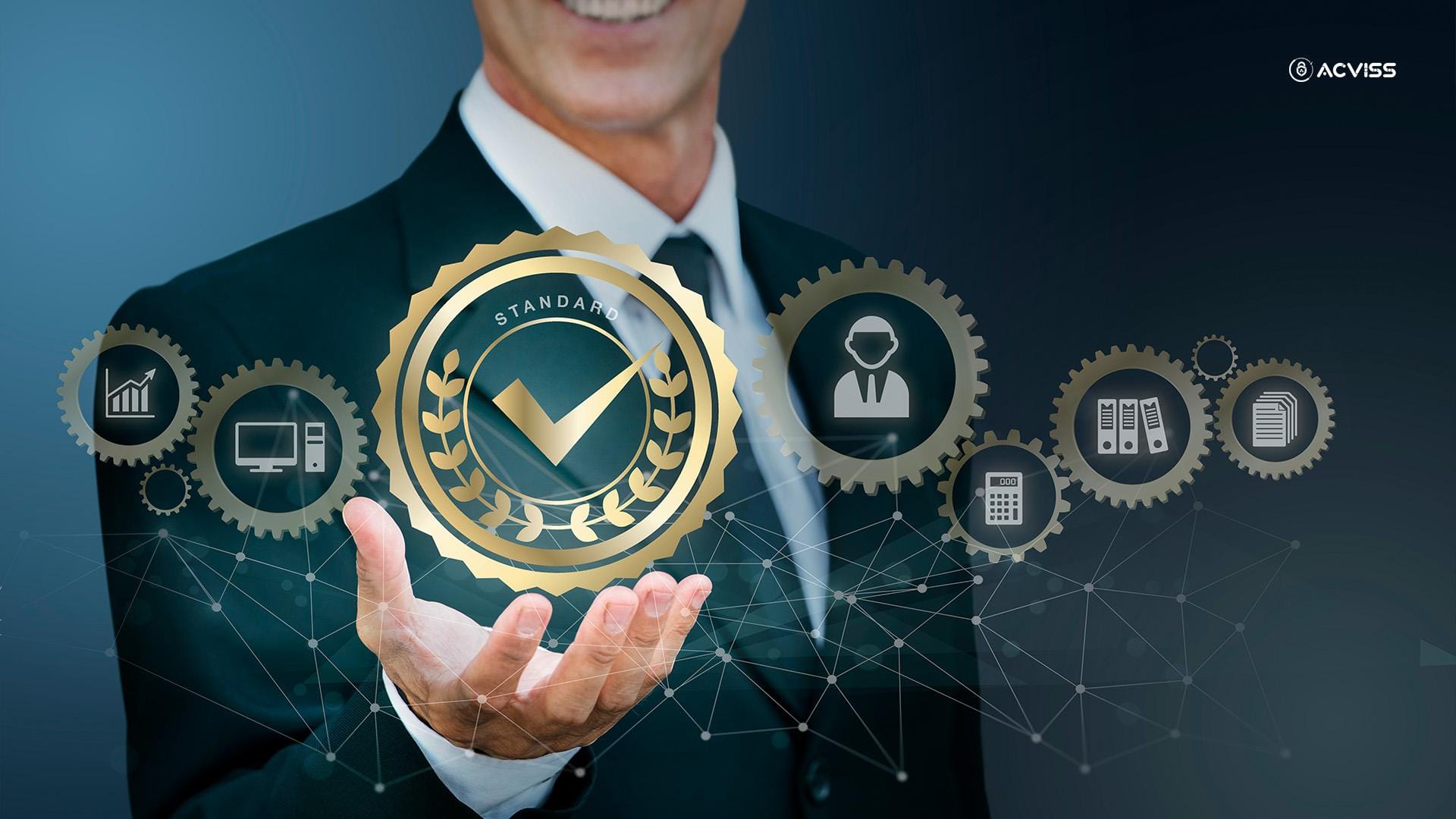
PPQ batches are designed to answer one critical question: Can this process consistently manufacture quality products at commercial scale? To arrive at that answer, several strategic objectives must be met, each of which contributes to the integrity and predictability of the manufacturing operation.
- PPQ batches are used to establish a baseline for product quality and process performance. They set the statistical expectations for critical quality attributes (CQAs) and critical process parameters (CPPs). These baselines are then used for trend monitoring, control strategy development, and future investigations.
- PPQ enables the identification and mitigation of variability. During this phase, the process is subjected to rigorous scrutiny under normal and slightly stressed conditions. This includes evaluating worst-case scenarios, such as upper and lower parameter limits or potential process shifts, to assess the boundaries within which the process remains in control.
- PPQ batches solidify the control strategy. It’s not enough for a process to merely pass; manufacturers must demonstrate that the controls built into the process are sufficient to detect and prevent deviations before they affect product quality. This requires robust data capture, real-time monitoring, and a strong understanding of process dynamics.
- PPQ lays the foundation for ongoing process verification. The data and insights gathered from PPQ batches inform the design of continued monitoring programs and support the establishment of a state of control throughout the product lifecycle.
What Goes Into a PPQ Batch Campaign
PPQ is preceded by extensive planning. Your Validation Master Plan (VMP) and Process Validation Protocol will define the scope, criteria, number of batches, sampling strategy, acceptance limits, and risk mitigation plans.
Then comes execution. Every PPQ batch must be:
- Manufactured using commercial-scale equipment in its qualified state.
- Handled by trained staff following SOPs and GMP protocols.
- Subjected to in-process controls that capture both variability and stability.
- Monitored for deviations, with any anomalies triggering root-cause analysis.
And yes, documentation is king. The PPQ report is a meticulous record of compliance, the kind of document that can make or break your next regulatory audit.
Regulatory Expectations: More Than a Formality
Regulatory bodies such as the FDA, EMA, MHRA, and others do not merely expect PPQ to be conducted; they expect it to be rigorous, risk-based, and scientifically justified. The FDA’s 2011 guidance on process validation clearly articulates that PPQ must be grounded in sound science and quality risk management principles.
This means that a "one-size-fits-all" approach no longer suffices. The number of PPQ batches, for instance, must be scientifically justified. While the traditional rule of thumb involved three successful consecutive batches, regulators now expect manufacturers to use risk-based rationale to determine the number of batches required based on product complexity, historical performance, equipment variability, and process maturity.
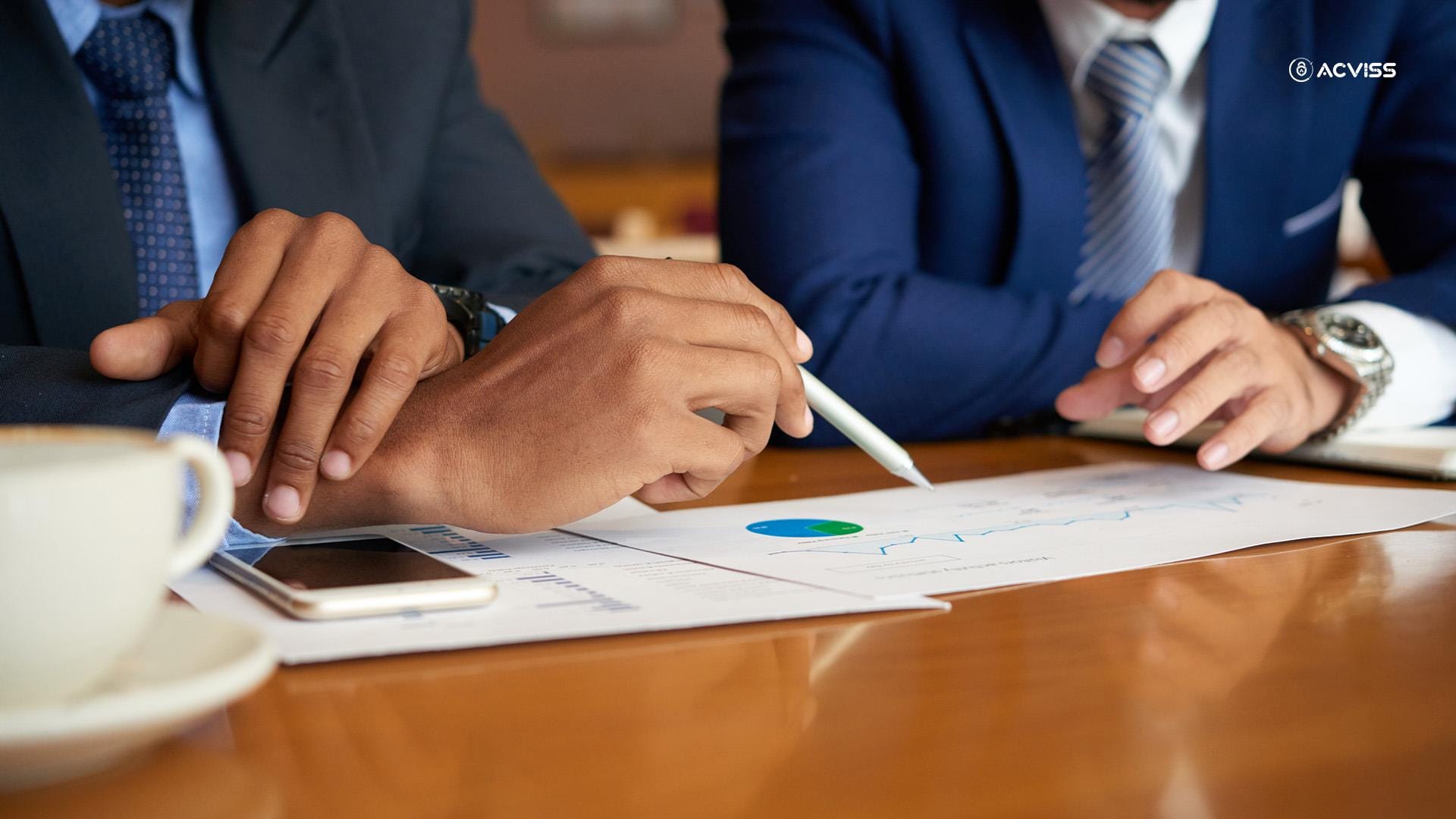
Moreover, regulators place heavy emphasis on data integrity and traceability. From raw material logs to equipment qualification records and in-process monitoring charts, every element of the PPQ campaign must be auditable and tied to a defined validation protocol. Deviations, if any, must be investigated and closed with documented root cause analysis and corrective actions before moving forward.
This is where solutions like Acviss play a transformative role. Acviss’s track and trace technology, built on blockchain, provides immutable data trails that enhance traceability across the supply chain and production process. During the PPQ phase, where traceability and data validation are non-negotiable, Acviss ensures every unit of production is accounted for, verified, and linked to verifiable process data, creating a digital backbone for audit readiness and regulatory compliance.
Crafting a PPQ Protocol: The Blueprint for Execution
A well-structured PPQ protocol is the linchpin of a successful qualification campaign. It serves as a comprehensive roadmap detailing every aspect of the validation effort, from batch numbers and sampling strategies to statistical methods and acceptance criteria.
1. Objective and Scope:
The protocol begins with a clear objective and scope, followed by a detailed description of the manufacturing process, including equipment, materials, and controls. It outlines the rationale for selecting specific batch sizes, frequencies, and process parameters, and provides a risk-based justification for the number of PPQ batches.
2. Sampling Plans
Sampling plans are crucial in the protocol, not only for finished product testing but also for in-process verification. This includes defining the locations, time points, and quantities for sampling, as well as the analytical methods used for evaluation.
3. Methodology
Equally important is the statistical methodology. The protocol must articulate how data will be evaluated, whether through control charts, capability indices (Cp, Cpk), regression analysis, or other tools, to confirm process stability and capability.
4. Contingency Planning.
Another vital aspect is contingency planning. The protocol must define how deviations will be handled, under what conditions a batch may be rejected, and what steps will be taken in case of failure to meet predefined acceptance criteria.
Acviss’s solution Origin integrates seamlessly with protocol execution by enabling tamper-proof labelling and real-time visibility into batch-level movements. These tools empower manufacturers to monitor batch journeys, verify authenticity, and ensure compliance without adding manual overheads, while reducing the risk of data tampering or label duplication, a critical risk during the PPQ phase.
The Execution Phase: Where Theory Meets Reality
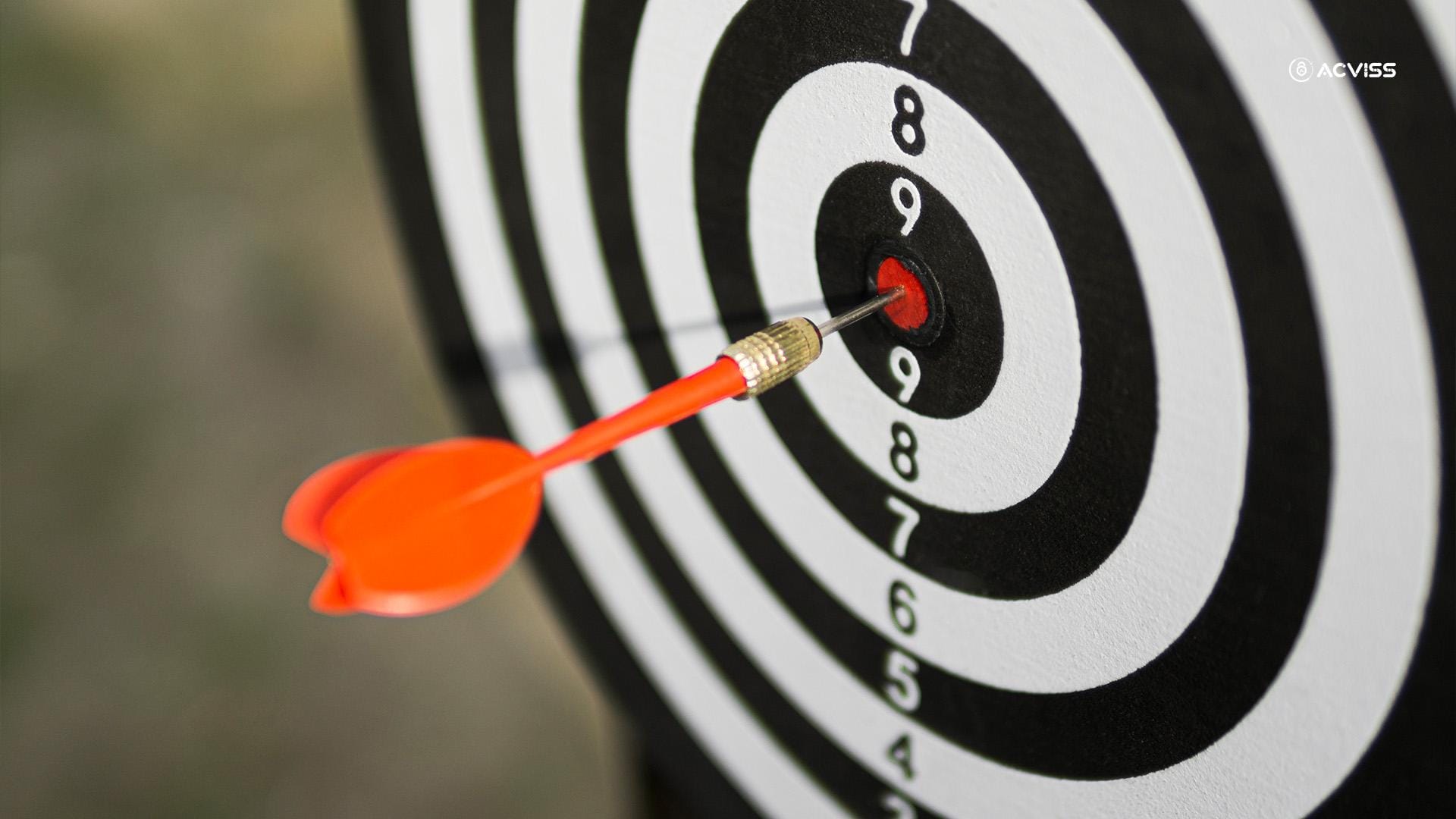
Once the protocol is approved, execution begins with heightened vigilance. Every PPQ batch is manufactured under strict controls, with meticulous documentation of each process step, test result, and deviation, if any. The execution phase demands heightened collaboration between quality assurance, production, validation, and analytical teams.
Operators must be adequately trained, equipment must be in a qualified state, and materials must come from verified sources. Any lapse at this stage can compromise the credibility of the entire PPQ campaign. Data must be collected in real-time, cross-verified, and reviewed per Good Manufacturing Practices (GMP).
One of the critical challenges during execution is balancing consistency with realism. While the temptation may exist to run PPQ batches under ideal conditions to ensure success, this would be counterproductive. Instead, the process should reflect the normal variability expected during routine operations, thereby providing a true representation of long-term process performance.
Beyond PPQ: Continued Process Verification
PPQ is not a one-time event. It marks the beginning of Stage 3 in the process validation lifecycle: Continued Process Verification (CPV). This stage involves ongoing monitoring of production batches to ensure the process remains stable and in control over time.
Key metrics from routine manufacturing are tracked to detect trends, identify shifts, and respond to deviations before they impact product quality. This feedback loop supports continuous improvement and ensures long-term compliance.
Digital tools and platforms like Acviss play a critical role here as well. Their ability to track, verify, and store production data ensures that CPV efforts are data-driven, accurate, and audit-ready.
Final Thoughts
A successful PPQ campaign depends on rigorous planning, thorough documentation, and reliable execution. With the increasing focus on data integrity, digital systems and traceability platforms like Acviss are becoming integral to modern validation strategies.
As global regulatory expectations continue to rise, the ability to demonstrate not only process performance but also data reliability and end-to-end traceability will differentiate manufacturers who are ready for the future from those who are not. In this context, PPQ is not just about compliance. It’s about building a foundation for consistent quality, trust, and operational excellence.
Ready to bring visibility and control to your validation workflows? Get in touch with us and explore how our technology can support your compliance and quality goals.