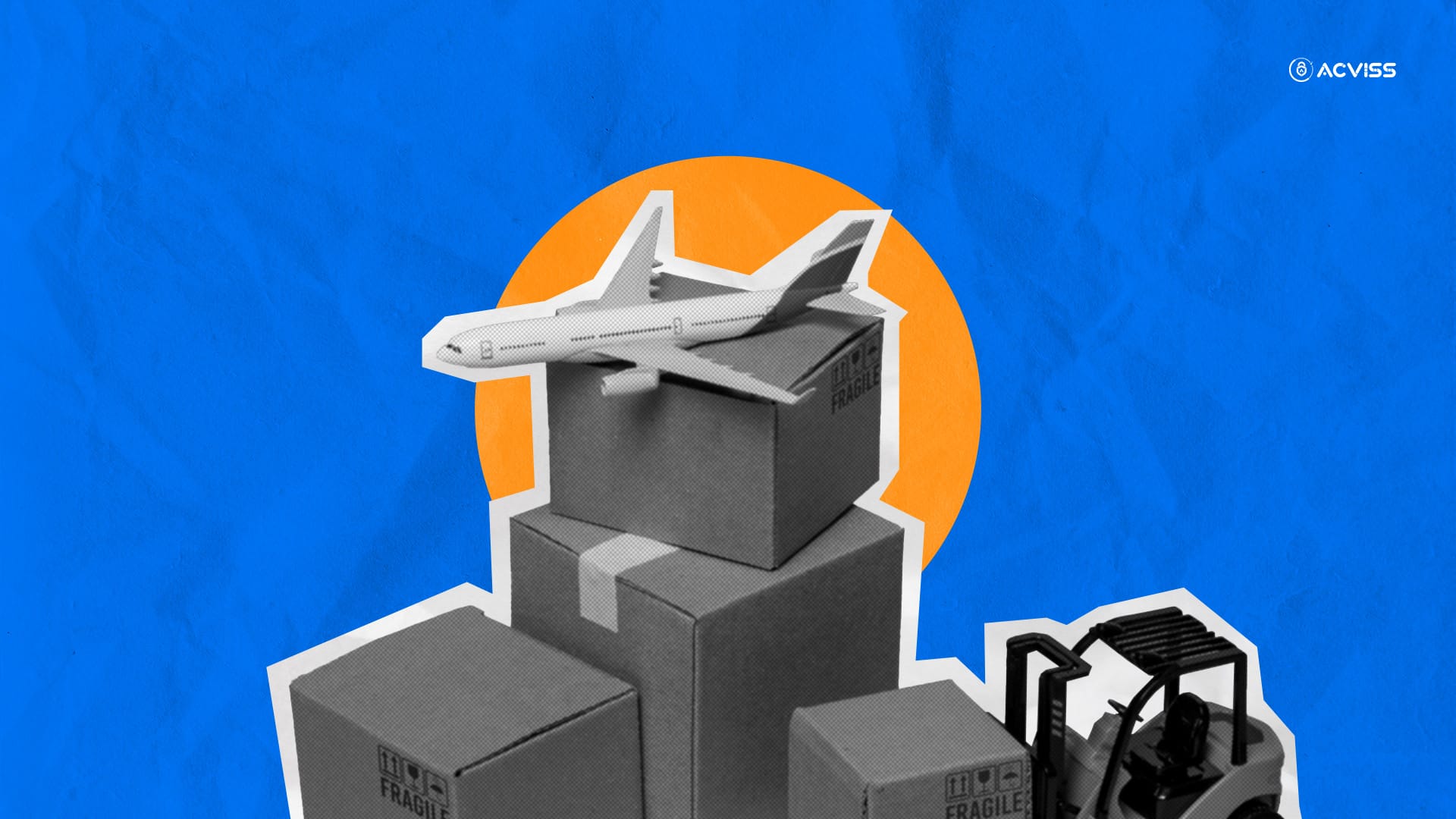
Did you know, a single disruption in your supply chain can cost you almost 50% of your annual profits over a decade? Isn't that shocking? But that is exactly what the World Economic Forum's Resilience Compass Report (2021) found.
Nowadays, supply chains are more complex than ever due to the interconnectedness of the global financial system. Because commodities are subject to many compliance checks, cross different countries, and involve numerous vendors, product traceability is now a necessity rather than a luxury.
What makes this significant to you? Because without clear visibility, your company is subject to delays, counterfeiting, compliance concerns, and decreased clientele. But worry not, because you are not the only one in this. Many businesses experience comparable challenges, but the good news is that there are effective and practical solutions.
In this blog, you will learn about the top ten supply chain challenges that hinder monitoring efficiency, as well as how to deal with each one confidently. Let us get started!
Top 10 Supply Chain Challenges of Product Tracking
1. Inconsistent Data Across Supply Chain Partners
Did you ever handle incompatible inventory statistics from multiple partners? This exemplifies contradictions in data perfectly.
Disconnected systems such as ERP, WMS, and TMS frequently fail to communicate with one another, resulting in fragmented, obsolete, or duplicate data. When your data sources are not in sync, it is practically impossible to maintain a reliable supply chain tracking.
How does this affect you?
- Insufficient accountability and transparency across stakeholders: You can not adequately track a product if each team is working with different data. This causes confusion, blunders, and finger-pointing.
- Unreliable predicted demand and delayed decision-making: With scattered data, your planning team might buy too much or too little inventory, reducing cash flow and client happiness.
Here’s the fix:
- Implement centralised digital platforms or middleware. Maintaining a single channel guarantees that everyone is in harmony. It includes your warehouse team and logistics partners.
- Use conventional Interfaces for connecting dissimilar frameworks. APIs are interfaces that facilitate interaction among entities. This results in a smooth data flow across your supply chain.
When your data is disorganised and contradictory, integrity and consistency suffer. Streamlining your data architecture is more than merely a technical update; it is a strategic decision that benefits every aspect of your supply chain.
2. Lack of Real-Time Visibility
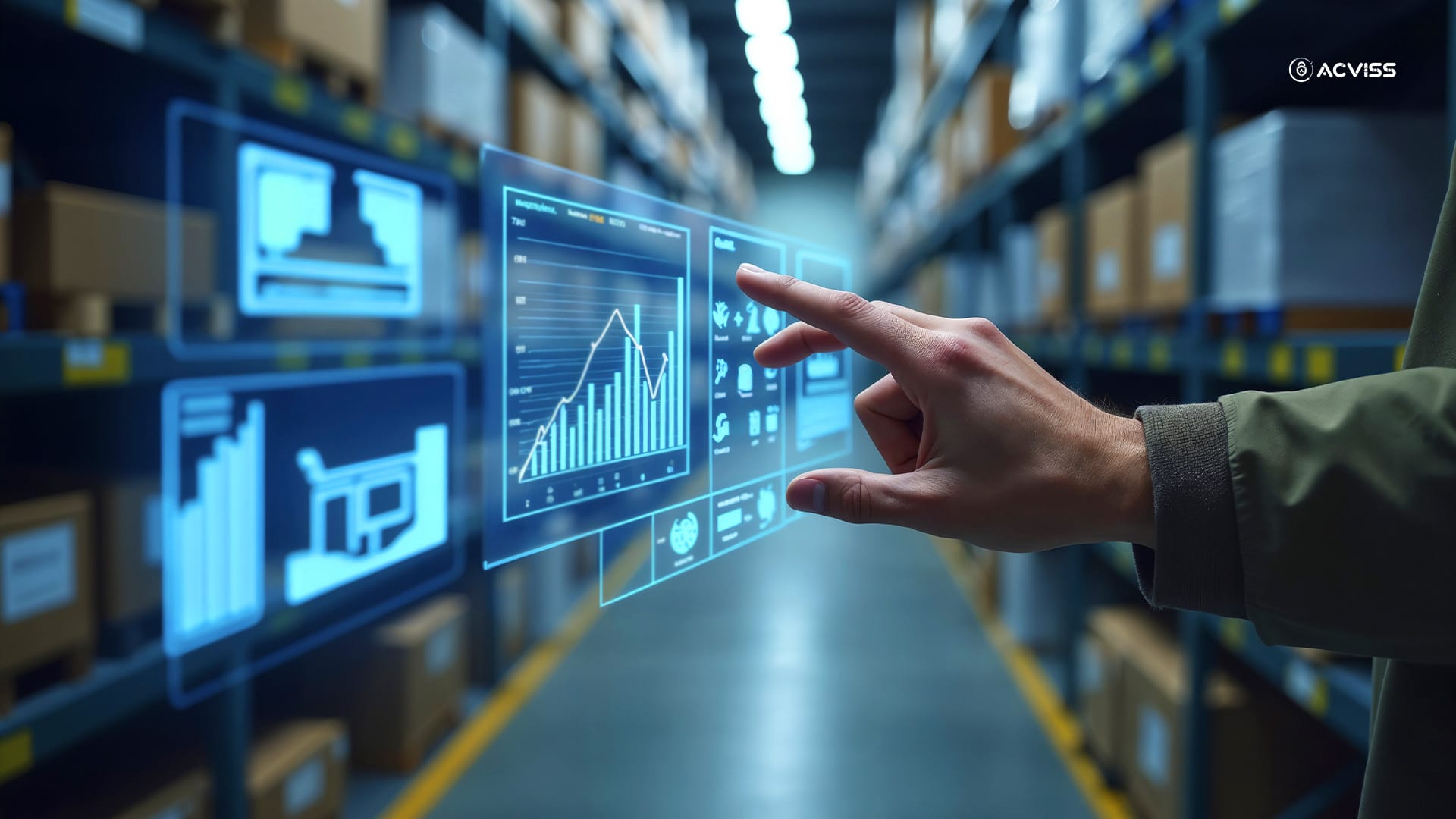
Have you been informed about your product's exact location? If you are depending on manual updates or spreadsheets, you probably do not, which is a major issue for supply chain visibility.
How does this affect you?
- Late deliveries and adaptive difficulty management: Without real-time information, you cannot respond quickly when delays arise. You are always catching up.
- Loss of confidence and an increase in consumer complaints: Customers want tracking notifications. If you are unable to give them, they will seek other avenues.
Here's the fix:
- Make use of real-time dashboards, GPS trackers, and the Internet of Things sensors. These systems offer continuous updates on the status, location, and state of commodities. This enables you to react quickly.
- Integrate mobile applications to get on-the-ground information from field employees. Enable drivers and warehouse staff to submit real-time information via mobile applications. This eliminates gaps in your visibility chain.
You are always one step behind if you do not have immediate access to information. Adopting continual monitoring guarantees enhanced oversight and fewer unforeseen events. Did you know that McKinsey & Company (2021) claims that real-time visibility may save transportation expenses by as much as 15%?
3. Counterfeit Products in the Supply Chain
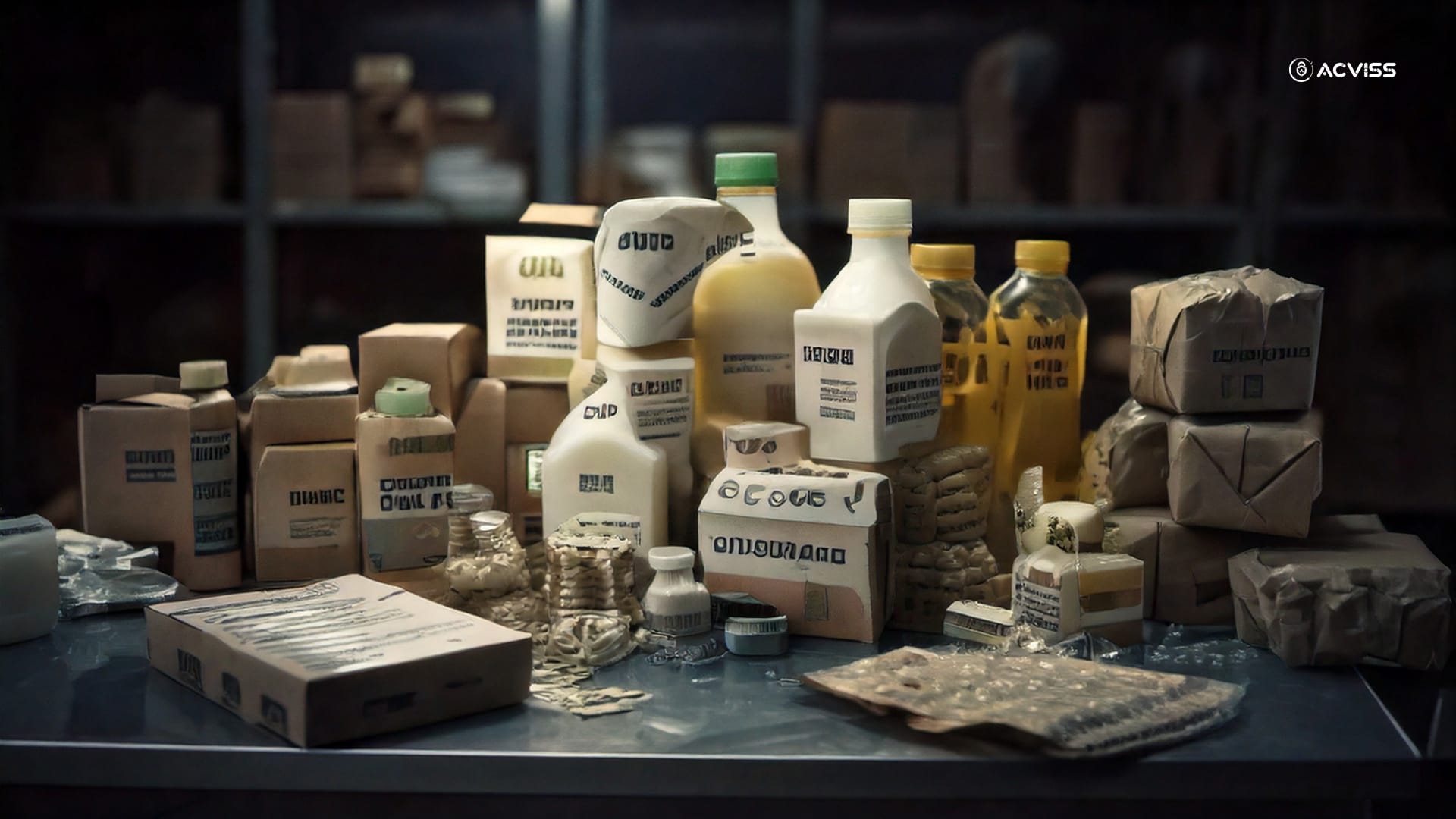
Have you ever been concerned about imitations influencing your supply chain? Counterfeit goods represent a substantial danger to global supply chains, costing firms over $500 billion each year and disrupting international commerce; the OECD reports that counterfeit items account for 3.3% of global trade. You're not abandoned. Product authenticity tracking is becoming a key issue for companies worldwide.
How does this affect you?
- Legal ramifications and product recall: Selling counterfeit goods, even unintentionally, can result in litigation and regulatory fines.
- Revenue loss and brand image damage: Once clients have lost confidence, it is difficult to regain it, and counterfeit items may quickly undermine loyalty.
Here’s the fix:
- Utilise serialisation, blockchain-based tracking, and digital authentication approaches: These technologies enable each product to be distinct and verifiable.
- Use item-level IDs and QR codes for verification at all stages: Allow suppliers, retailers, and buyers to verify a product's legitimacy instantaneously.
For instance, the Falsified Medicines Directive (FMD) of the European Union mandates safety precautions and serialisation to stop counterfeit drugs from entering the pharmacy supply chain.
Counterfeits are more than simply a nuisance; they represent an imminent risk to your brand. Having control over product authenticity protects both money and reputation.
4. Regulatory Compliance and Audits
Does the thought of a surprise compliance audit stress you out? With different countries enforcing different regulations, staying compliant isn’t easy. You may face some serious consequences if you do not satisfy it.
How does this affect you?
- Fines for non-compliance and rejected shipments: Failure to provide traceability logs can delay or stop shipments at borders.
- Brand reputation risks and legal issues: Recurring compliance violations can permanently harm your brand and credibility.
Here’s the fix:
- Automate compliance reporting for peace of mind. Digital systems can generate audit trails automatically, reducing manual work and errors.
- Use configurable supply chain compliance tools. These tools adapt to regional rules like EU FMD or US FSMA, ensuring you stay ahead.
Here you can see some of the regional key regulations across the world in detail:
- EU Falsified Medicines Directive (FMD) – Pharmaceuticals: It aims to stop counterfeit medications from getting into the legitimate supply chain by putting in place uniform safety and control procedures throughout Europe.
- US Food Safety Modernization Act (FSMA) – Food Safety: It allows the FDA to impose preventive controls across the food supply chain by mandating food establishments to use risk evaluation and risk-based preventive controls.
- China's Good Supply Practice for Medical Devices (GSPMD) – Medical Devices: This regulation takes effect on July 1, 2024. It standardised the supervision and administration of medical devices to ensure their safety and quality.
- India's Food Safety and Standards Regulations (FSSR) – Food Safety: FSSAI created these rules, which require safety administration processes and set scientific food guidelines to guarantee the supply of nutritious, safe food.
Regulations are constantly evolving. Automating compliance, you turn a risk into a competitive advantage.
5. Difficulty Tracking Returns and Reverse Logistics
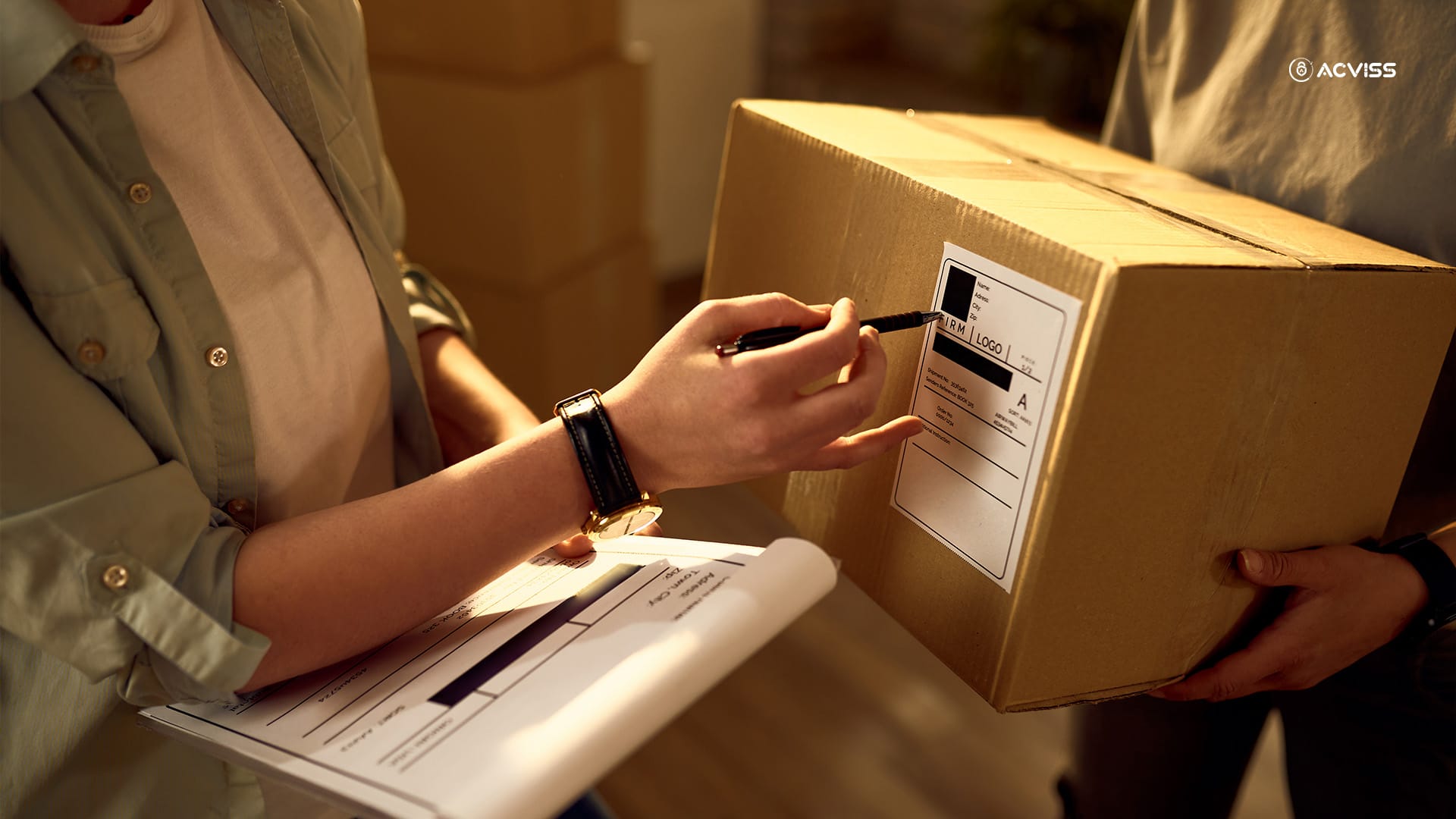
What happens after a customer sends something back? If returns aren’t integrated into your track-and-trace solutions, you’ll face chaos.
How does this affect you?
- Overstock and higher storage expenses: Untouched recoveries take up money and space.
- Poor customer experience and brand disloyalty: Customers expect quick refunds or replacements, and you can’t deliver without solid tracking.
Here’s the fix:
- Integrate reverse logistics into your core tracking system. Ensure returns flow through the same visibility pipeline as outgoing shipments.
- Use QR-based return labels and auto-verification tools. These tools instantly log returned items, speeding up the process and reducing errors.
Returns are a reality of business. If you can’t track them smoothly, you’re losing more than just products; you’re losing customers.
6. Lack of End-to-End Product Traceability
Do you lose track of your product once it reaches your distributor? If so, you’re missing critical steps in product traceability.
How does this affect you?
- Inability to perform effective recalls: If something goes wrong, you need to know exactly where the product is.
- Missed opportunities for consumer engagement and trust-building: Modern consumers want transparency, especially in food, fashion, and health products.
Here’s the fix
- Extend traceability from source to end-user using digital twins or smart labels. This ensures every product can be traced across its entire journey.
- Provide consumer-facing QR codes for transparency. Let your customers verify origins and build trust in your brand.
Nestlé's "Farm to Fork" program, backed by IBM Food Trust blockchain technology, allows customers to monitor food sources in real-time, establishing a high standard for transparency and traceability.
From farm to fork—or factory to front door—traceability builds trust, loyalty, and operational resilience.
7. High Cost of Technology Implementation
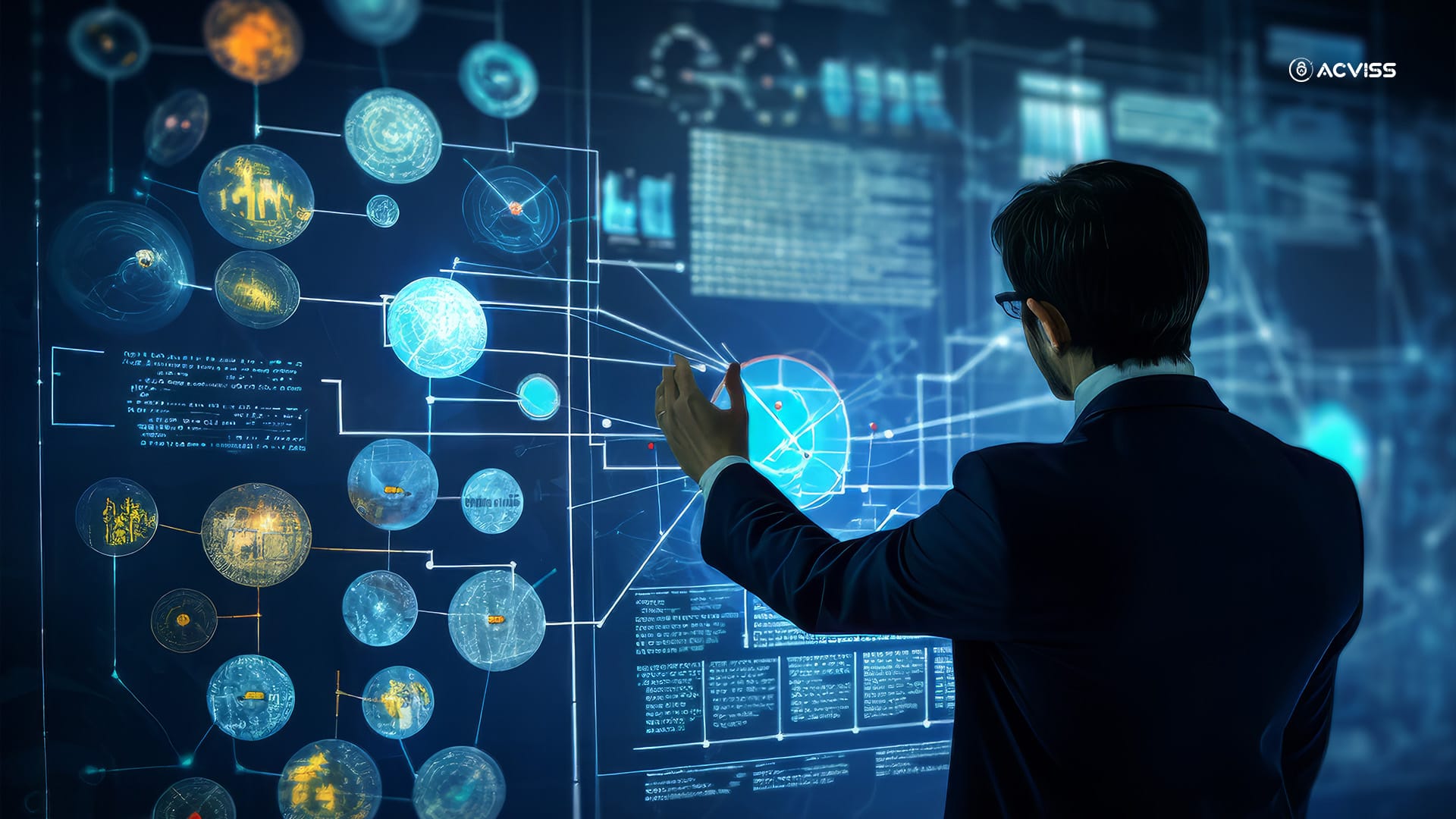
Worried that modern tech is out of reach financially? It’s a common concern, especially for small and medium-sized businesses dealing with challenges in supply chain management.
How does this affect you?
- Hesitation from SMEs to digitise: Fear of cost delays and transformation.
- ROI pressure on large enterprises: Leaders demand proof of value before committing to big budgets.
Here’s the fix:
- Opt for modular SaaS platforms with pay-as-you-go pricing: Start small and scale based on performance and budget.
- Lease hardware and consider open-source blockchain protocols to lower costs: This reduces upfront investment and supports innovation.
According to Deloitte, compared to on-premise options, cloud computing increased profits by 21% and accelerated growth by 26% for small and medium-sized organisations.
Cost does not have to be a barrier. Scalable, adaptable tools enable even tiny enterprises to become digital without going bankrupt.
8. Human Errors and Manual Data Entry
Still, using pen and paper? Or copying data into spreadsheets? Manual methods don’t cut it for common logistics tracking problems and solutions.
How does this affect you?
- Shipment mismatches and inaccurate tracking: A wrong entry can send products to the wrong location or lose them entirely.
- Wasted time correcting avoidable errors: Your team spends hours fixing what automation could’ve prevented.
Here’s the fix:
- Use RFID/barcode scanning to automate data capture: Reduce the risk of mistakes and speed up operations.
- Implement AI-driven anomaly detection to flag and fix errors in real-time: Let technology catch what humans might miss.
Manual data entry is a silent killer in your supply chain. Automating your processes reduces risk and frees up your team for higher-value tasks.
9. Integration Issues with Legacy Systems
Still, relying on systems built before smartphones existed? Legacy tools can stall your entire track-and-trace solutions strategy.
How does this affect you?
- Data delays and integration failures: Old systems can’t keep up with modern data formats, causing breakdowns in communication.
- High IT maintenance costs and low flexibility: Legacy software needs constant patching and lacks adaptability.
Here’s the fix:
- Use middleware and RPA (Robotic Process Automation) for short-term fixes: These tools bridge the gap while you upgrade.
- Gradually modernise through APIs while training your staff to adapt: Make your team part of the transformation, so new tech doesn’t go unused.
Legacy systems might have served you well once, but today’s supply chain demands agility. Update or risk falling behind.
10. Limited Supply Chain Transparency from Third-Party Vendors
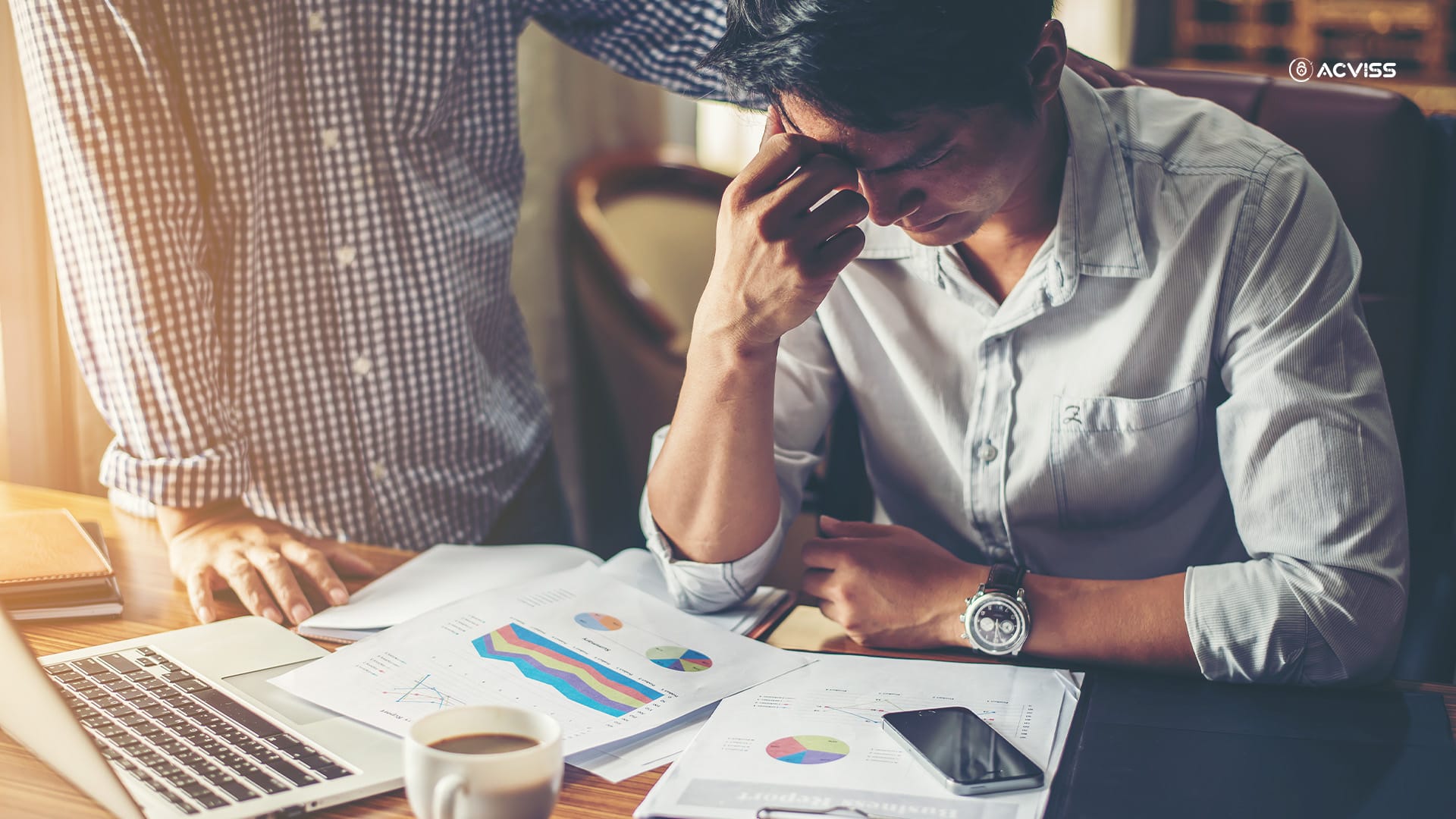
Do you trust your vendors completely? If they lack transparency, your entire supply chain transparency effort is at risk.
How does this affect you?
- Fraud risk and reduced visibility: You won’t know what’s happening behind closed doors, opening the door to shady practices.
- SLA violations and compliance issues: If vendors can’t prove their processes, you suffer the consequences.
Here’s the fix:
- Partner with EUDR-certified or ISO-compliant suppliers: These certifications show a commitment to ethical and transparent practices.
- Use smart contracts and vendor performance dashboards to ensure accountability: Get real-time metrics on vendor reliability.
Take inspiration from industry leaders: For example, Apple’s Supplier Responsibility program uses transparency metrics to monitor third-party suppliers and ensure they adhere to tight criteria.
Trust is earned through transparency. Demand it from every player in your supply chain—because your reputation depends on it.
How Acviss Helps Solve These Challenges
So, how do you bring all of this together in one place? Enter Acviss.
Acviss is your partner in building a secure, transparent, and tech-forward supply chain. Their solutions are designed to tackle these challenges head-on. But how does it help? Let's see:
Key tools from Acviss:
- Origin: Offers complete track and trace visibility, helping you monitor every step of the supply chain journey.
- Certify: Delivers tamper-proof digital authentication to protect against counterfeits and fraud.
- Truviss: Enables third-party monitoring with proactive fraud detection.
- Consumer Product Verification Tools: Let customers scan and verify products instantly, building trust and brand loyalty.
What makes Acviss different?
- Scalable SaaS models that work for both SMEs and large enterprises.
- Low-code integration with your existing ERP/WMS/TMS tools.
- Blockchain-backed traceability that’s compliant with global regulations.
- Dashboards that may be customised for adherence reports, tracking of performance, and supplier auditing.
Securing Tomorrow’s Supply Chain, Today
In today’s volatile landscape, simply managing logistics no longer suffices; you need a supply chain that is trusted, traceable, and transparent. Addressing the challenges of product tracking is not just about efficiency; it’s about ensuring compliance, safeguarding your brand, and fostering lasting customer loyalty.
Acviss empowers businesses with scalable, intelligent solutions designed to secure your supply chain and prepare you for the future.
Ready to take the next step?
Request a demo today and discover how Acviss can help you build a smarter, more secure supply chain, before risks become realities.