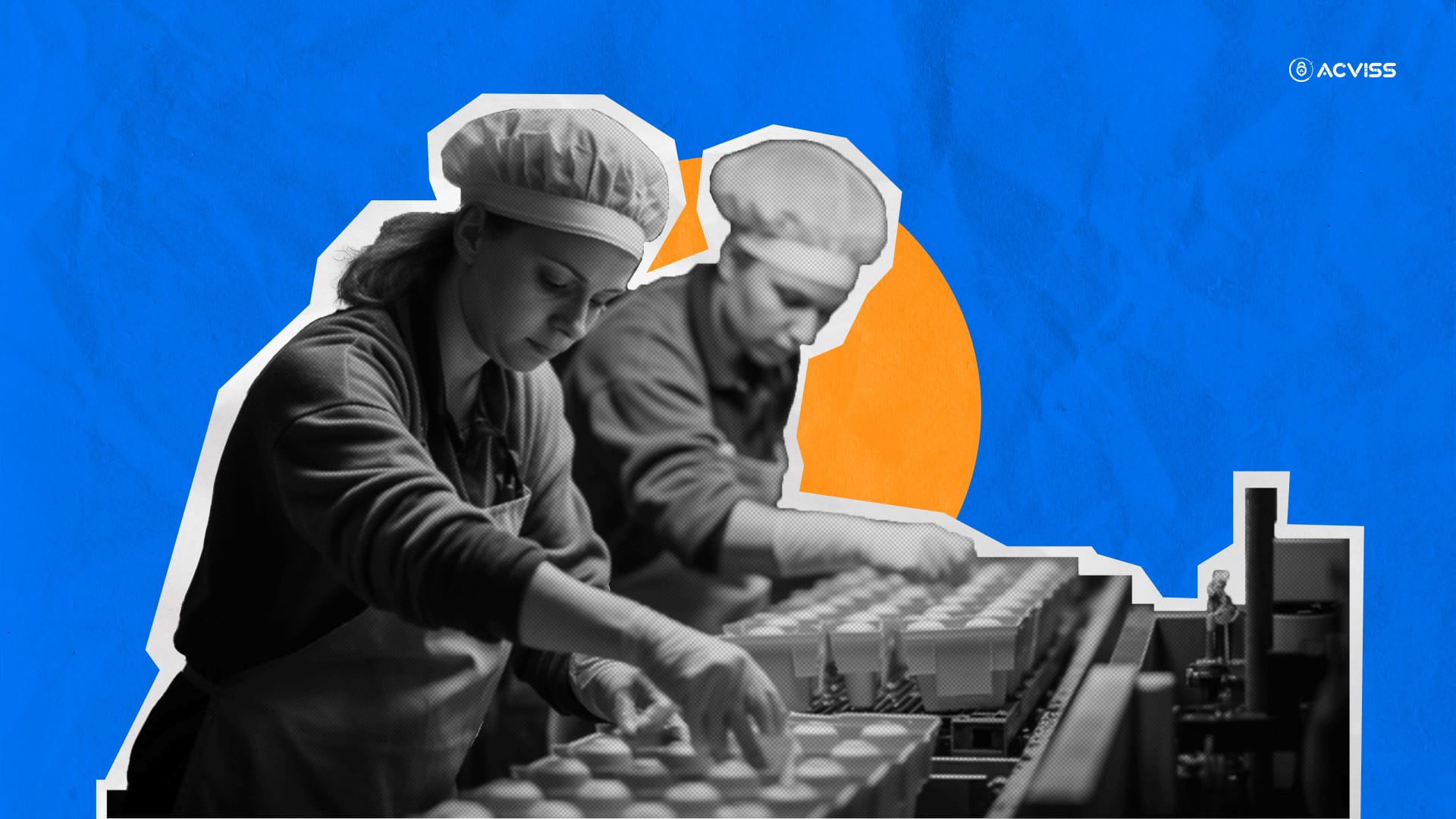
Selecting the appropriate production strategy may make or break your manufacturing efficiency. Flexibility, cost management, and quality assurance are not just desirable qualities in today's fast-paced environment but are essential.
Batch production is one strategy that achieves an ideal mix of size and flexibility. It is a standard solution in businesses that require specific outputs, frequent product changes, or seasonal demand.
In this article, you will learn how this process works, where it fits into the larger manufacturing environment, its advantages and disadvantages, real-world instances, and how technology makes batch production smarter than ever.
Let us start with the basis.
What Is Batch Production?
The method of creating goods in predetermined groupings, or "batches," as opposed to one at a time or in a continuous process, is known as batch production. Each batch finishes one stage of the manufacturing process before proceeding to the next.
Think about baking. You make a batch of dough, bake it all at once, and then start another batch. This approach allows you to reliably repeat the operation while also adjusting aspects as needed.
You’ll often find batch processing in manufacturing industries like:
- Food and beverage
- Pharmaceuticals
- Fashion and apparel
- Cosmetics
- Consumer electronics
It is one of the main types of production processes, ranging somewhere between job production (customisation) and mass production (high volume, little variation).
The Batch Manufacturing Process: Step-by-Step
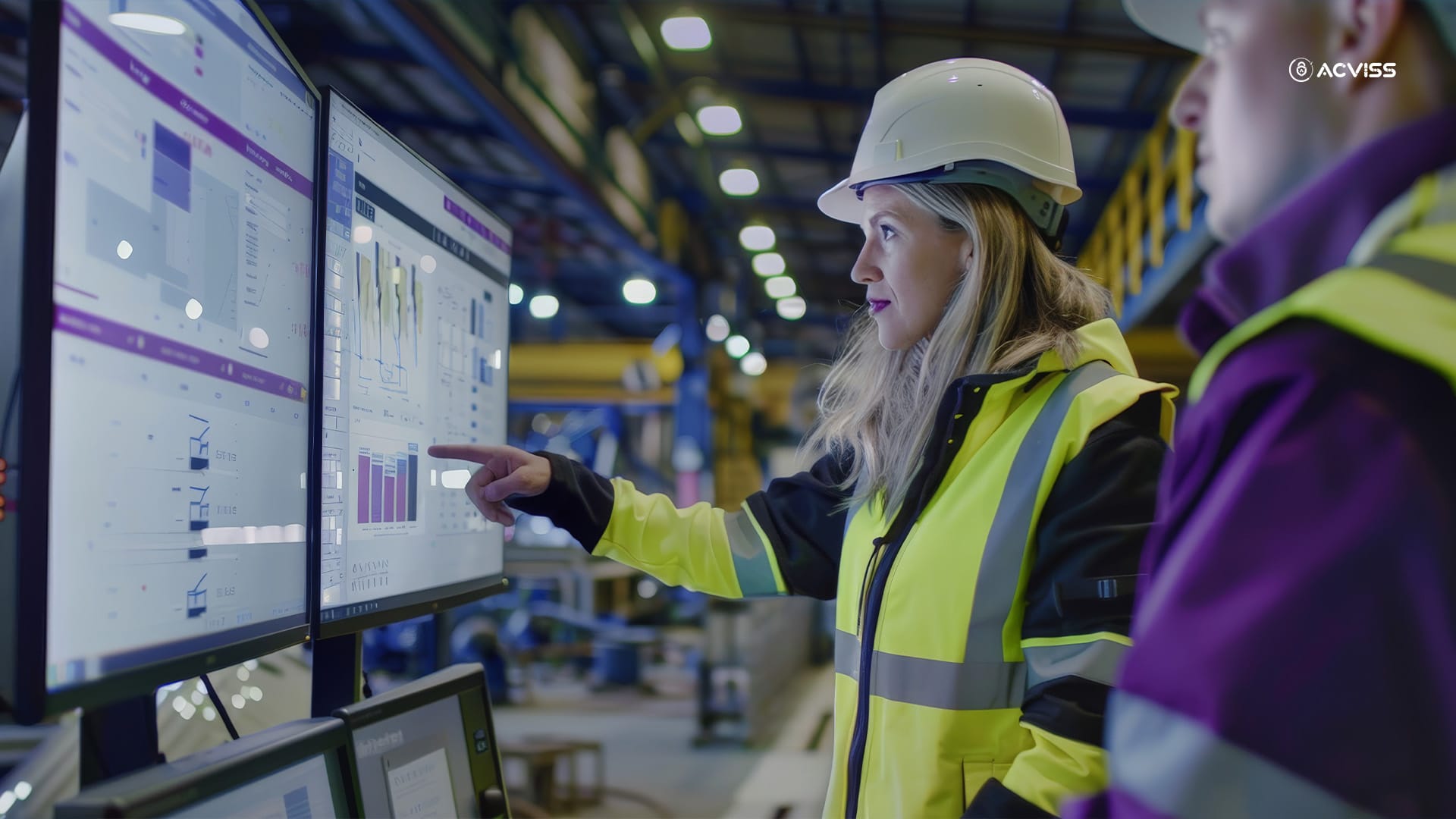
Batch manufacturing is more than simply a method; it's a beat. Once you understand the stages, you may fine-tune the entire operation to make it more efficient and flexible.
Let us explain it so you can understand how each component interacts and why it is essential.
1. Planning
This is your starting line. Before you make anything, you need a clear plan.
- What’s the demand like?
- How many units will you produce per batch?
- Which machines, tools, or team members will be involved?
- How much time does it take to complete?
This is where you set a production schedule and define the batch size. Think of it like making a recipe, where you decide how many portions you will need and when they will be done.
Whenever possible, use a visual planner or Gantt chart to plan and change batch schedules for your team.
2. Sourcing
Now is the time to gather all of your supplies. You obtain materials and components precisely for the next batch.
This may include:
- Raw materials (e.g., fabric, flour, chemicals)
- Packaging materials
- Special components or custom parts
Getting this properly prevents last-minute delays and waste. You are not merely stockpiling; you are preparing exactly what is required for this specific batch and simply this batch.
Ask yourself: Do you have a reputable supplier list that can manage short lead times for a variety of batch sizes?
3. Processing
Here's where the magic happens: manufacturing begins.
Your batch is now moving through the production process, one group at a time. Depending on your field of work, this might entail:
- Mixing or combining ingredients
- Assembling parts
- Molding or shaping
- Painting or coating
- Labeling and packing
Each batch completes one stage before proceeding to the next. This sequential approach keeps things structured and allows you to make adjustments between batches without resetting the entire system.
⭐️Pro tip: If you utilise shared equipment, plan cleaning or resets between batches to avoid contamination or mix-ups. |
---|
4. Inspection
You never want quality to slip; this is where your checks come in.
After each batch is processed, you (or your team) inspect it. This could involve:
- Visual checks
- Functional tests
- Weight/volume measurements
- Sampling for lab tests
Because you're inspecting batch by batch, any issues can be caught early and corrected before the next round starts. It’s a built-in quality control system.
Mini-Challenge: Review your inspection checklist: does it cover everything that could go wrong in one batch?
5. Storage or Distribution
Your batch is complete! It is currently in storage or on a journey to customers, suppliers, and retailers.
At this stage, it is vital to accurately figure out and record the complete batch in order to track it down later. This is especially important in sectors like drugs, food, and beauty products, which need traceability.
Are you aware that using batch-level barcodes or QR codes allows you to observe precisely when every product ends up?
Imagine this as a loop; you repeat it as demand requires, adjusting the size and frequency as needed.
Batch Production in Action: Industry Examples

Here’s how batch production works in the real world:
A. Food and Beverage
Visualise a bakery that makes 200 loaves of bread every day. The next batch begins once the previous batch has been mixed, proofed, baked, cooled, and packaged.
Why it works: Keep your recipes consistent and practice good hygiene. Batch manufacturing helps make both your goals simpler.
As an illustration, a chocolate manufacturer modifies batch size in response to seasonal demand, such as around Easter or Diwali.
B. Pharmaceuticals
Medicines are frequently prepared in sterile batches under strict standards. Every batch adheres to a regulated recipe and process.
Why it works: It is simpler to monitor, recall (if necessary), and adhere to regulatory requirements.
For instance, a vaccine producer may change the components of a batch in response to changes in regulations or pathogen variations.
C. Fashion and Apparel
Seasonal collections or limited editions are created in batches based on design and trend forecasts.
Why it works: Flexibility to switch styles or materials with each batch.
Example: A clothing brand releases a “spring edit” in five colorways, produced in small batches per SKU.
D. Electronics
Printed circuit boards are frequently manufactured in batches to suit different designs or technical specifications.
Why it works: Reduces setup time and expense when several versions are required.
For example, a smartphone manufacturer may batch-produce three versions with varying features, utilising similar components.
Advantages of Batch Production
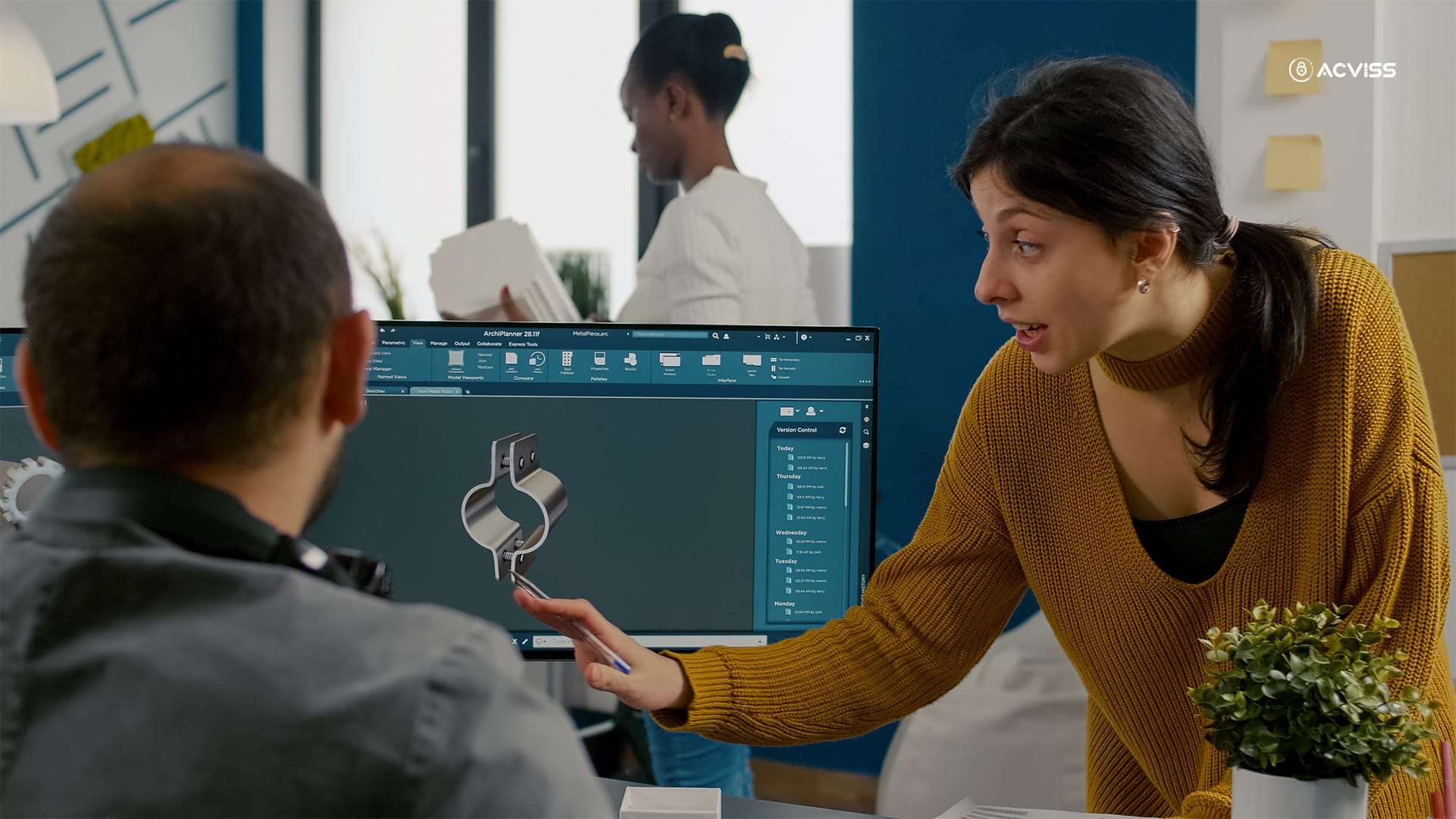
Now that you've seen how batch production works across different industries, let’s talk about why it’s such a popular choice.
If you’re not running a massive factory but still want to scale efficiently, batch production gives you the best of both worlds: control and flexibility. Here’s how it benefits you:
1. Cost-effective for medium-scale manufacturing
You don’t need to produce thousands of units at once to stay profitable. Meeting demand through batch manufacturing prevents a surplus and excessive spending.
2. Flexibility in customisation
Want to change the color, design, or recipe? No problem. You can tweak your batches between runs, which is great if your products change with seasons, trends, or customer needs.
3. Lower setup costs than mass production
Since you’re not investing in massive production lines or expensive continuous systems, your upfront costs stay manageable. This makes it ideal if you're launching new products or experimenting with variations.
4. Efficient use of machinery
Your machines don’t sit idle for long. You can use the same equipment across different batches, which helps you get more out of your existing setup.
5. Simpler batch-level quality control
As opposed to inspecting individual units, you examine each batch. That makes it easier to identify problems, ensure uniformity, and detect faults early.
6. Reduces waste in variable-demand scenarios
Not sure how much you’ll sell next month? Producing in batches lets you react to demand without flooding your warehouse or wasting materials.
All these benefits add up to one thing: you stay agile without sacrificing efficiency. However, like with any procedure, there are obstacles to overcome.
Challenges in Batch Manufacturing
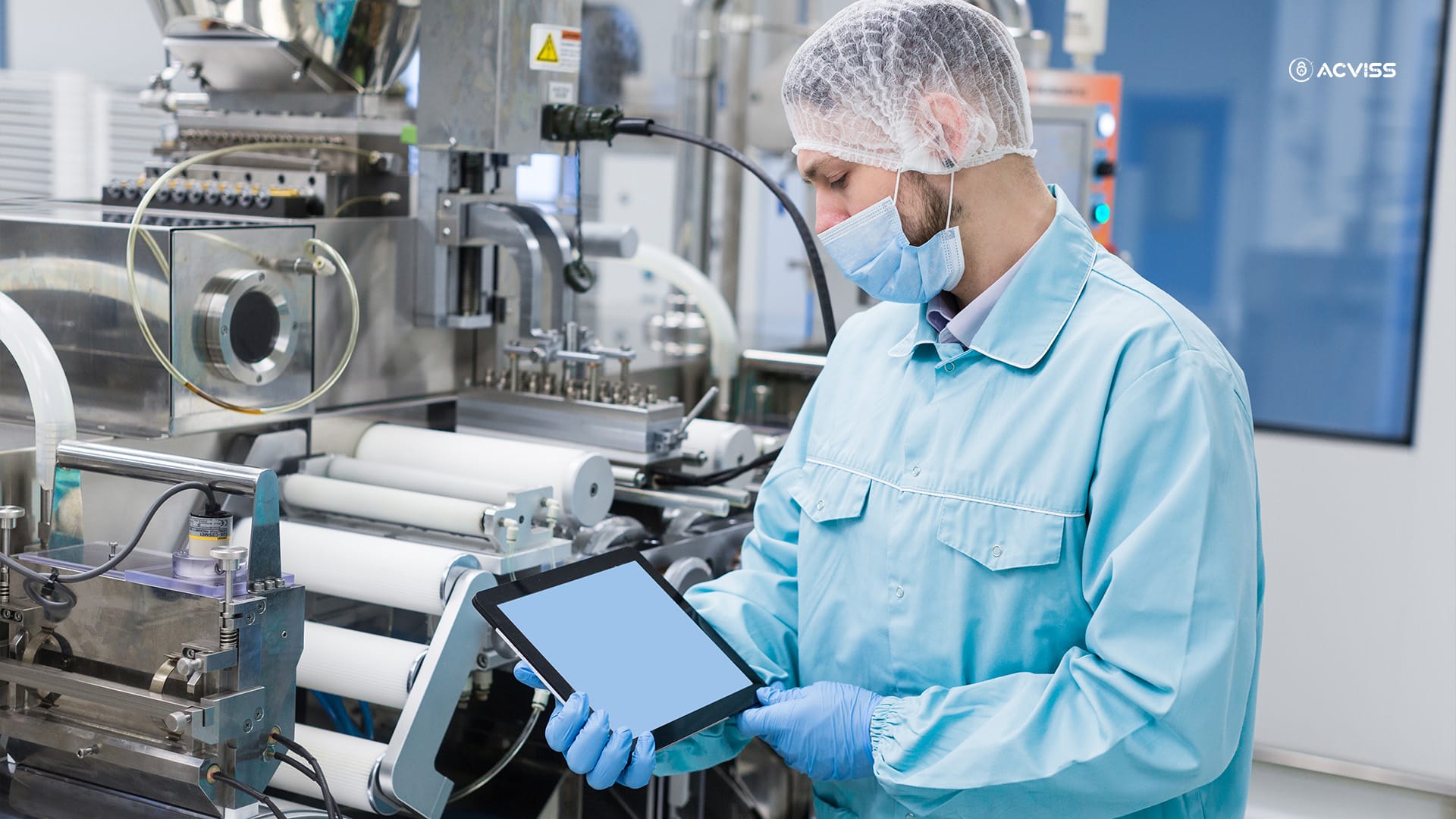
While batch manufacturing allows you greater flexibility and control, you must also deal with a few frequent difficulties. Understanding these problems beforehand allows you to keep one step ahead.
Here’s what you might face, and how it connects back to the way batches are made:
1. Idle time between batches
After one batch finishes, your machines might need cleaning, resetting, or reconfiguring before the next batch starts. This downtime can add up if not planned properly.
2. Increased storage needs
Because products are made in groups, you’ll need space to hold them before they're moved or sold. If demand slows down or distribution is delayed, storage can become tight.
3. Complex inventory management
With multiple products or versions in play, keeping track of which materials go into which batch and where that batch is can be tricky. You’ll need a good system to avoid mix-ups or shortages.
4. Risk of errors between batch transitions
Switching from one product or recipe to another? That’s when errors are most likely. One small mistake, like using the wrong ingredient or setting, can affect an entire batch.
5. Requires skilled labor to handle changeovers
Unlike fully automated systems, batch production often needs experienced workers to manage transitions, inspect products, and make adjustments. Training and supervision become essential.
But here's the good news: these barriers are not deal breakers. In reality, they are becoming simpler to tackle with the correct technology. Smart tools can help you reduce downtime, track batches more accurately, and even automate quality control.
Batch Production vs Mass Production
So, which approach fits your business better: batch or mass production?
It all depends on what you create, how frequently you update your product, and the type of demand you are handling.
Let us dissect it for you:
Feature | Batch Production | Mass Production |
---|---|---|
Output Volume | Medium | High |
Flexibility | High | Low |
Cost Per Unit | Moderate | Low (at scale) |
Setup Complexity | Medium | High (initial setup) |
Common Use Cases | Seasonal/flexible goods | Uniform high-demand goods |
If your products change with seasons, trends, or customer preferences, batch production gives you the freedom to adjust. It lets you test, switch, and experiment without a huge setup cost.
On the flip side, if you’re churning out the same product in large volumes (think water bottles or toothpaste), mass production could be more efficient and cost-effective.
But here’s the thing: batch production doesn’t mean giving up on efficiency or scale. That’s where technology steps in.
How Technology Enhances Batch Production
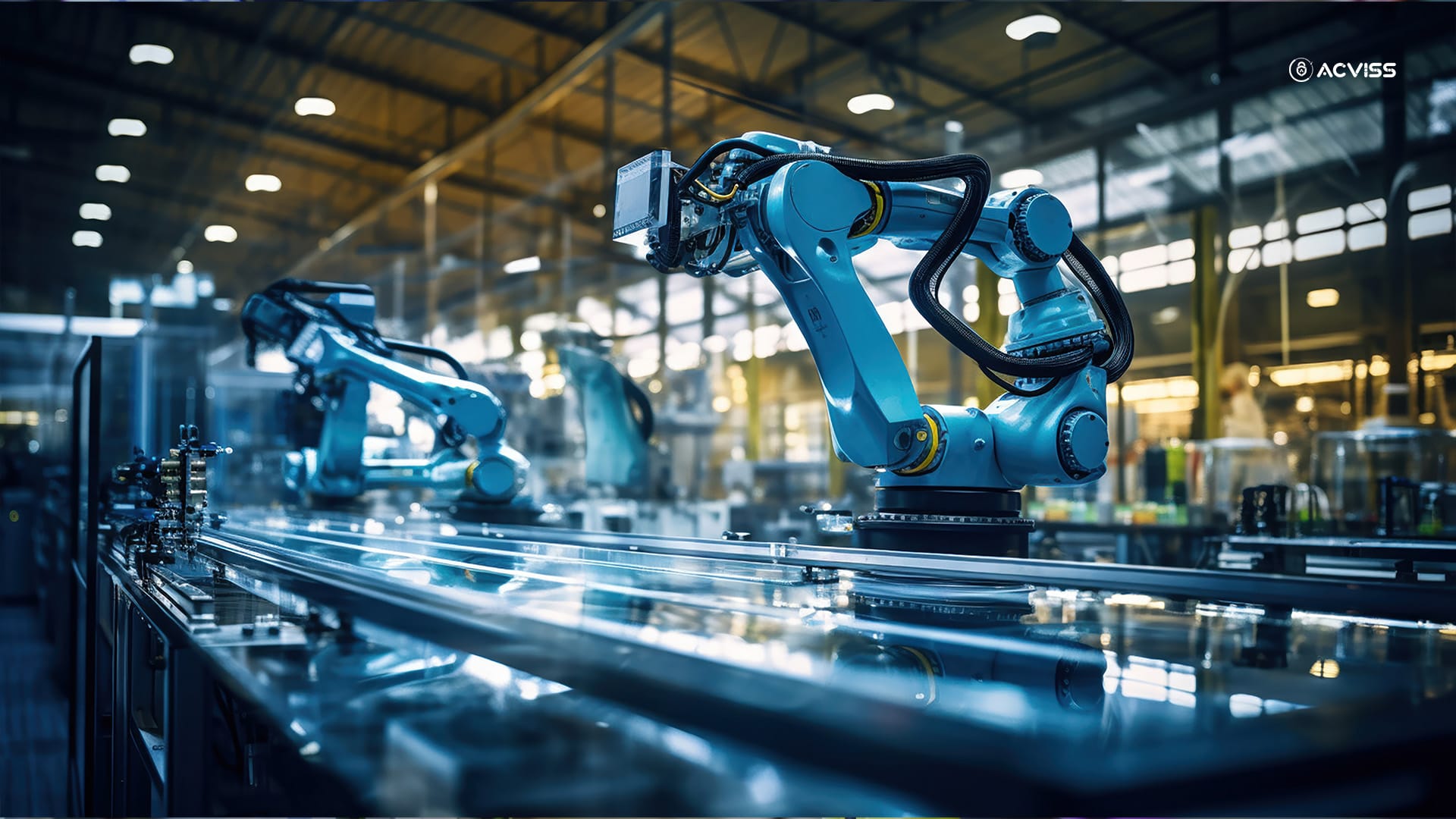
Now that you know batch production is more flexible, you might be wondering how you can make it faster, smarter, and even more reliable.
This is where modern tech becomes your best friend. It takes the traditional batch setup and gives it a digital upgrade.
Let’s explore how:
1. Automation
You no longer have to manually reconfigure machines or supervise every stage. Automation handles repetitive tasks, speeds up changeovers, and keeps everything consistent. That means fewer errors and more uptime between batches.
2. AI Forecasting
Ever produced too much or too little of something? AI allows you to figure out demand more precisely. It looks at trends, seasonality, and even past sales to suggest optimal batch sizes, helping you avoid waste and shortages.
3. IoT Sensors
These tiny devices can be installed on your machines to monitor performance in real-time. They alert you when a part needs maintenance or if a batch is falling behind schedule, so you’re never caught off guard.
4. Digital Twins
Think of this as a virtual version of your production line. You can test different scenarios, tweak batch settings, and plan new runs without touching the actual machinery.
5. Blockchain for Traceability
In industries such as food and pharmaceuticals, knowing where and when a batch was produced is critical. Blockchain technology securely stores that data, allowing you, your partners, and even your customers to verify it instantly.
Integrating these tools ensures that your batch production not only remains relevant but also evolves. You’ll be able to produce faster, track better, and adjust quicker to whatever your market wants.
Let us look at how a platform like Acviss combines all of this into a single, smart solution so you do not have to figure it out on your own.
How Acviss Solutions Supports Smarter Batch Manufacturing
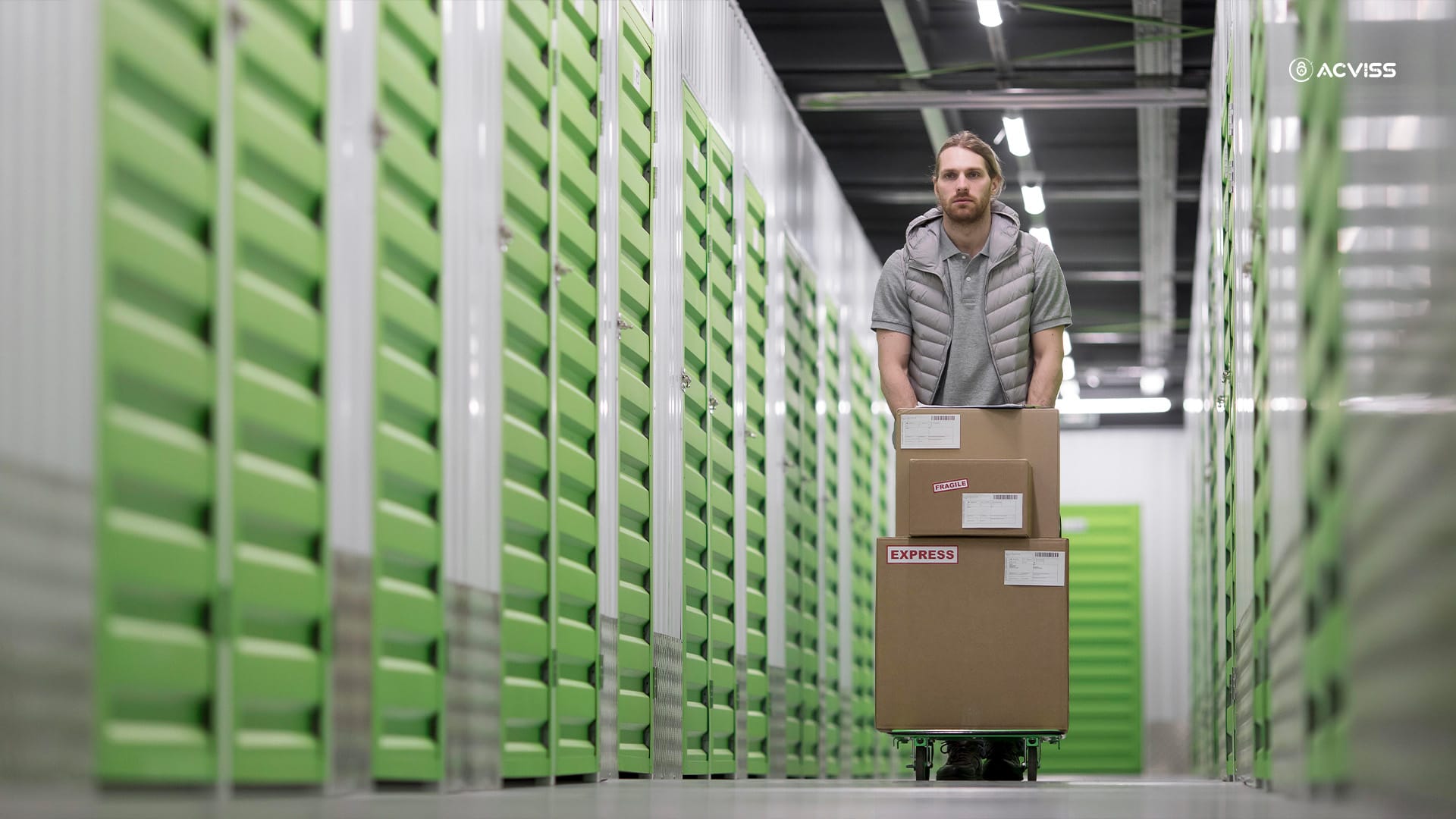
Acviss is a leader in product authentication and traceability. If you're managing batch-based production, Acviss can help you secure and track every batch, from the factory floor to the end customer.
How Acviss Empowers Batch Production:
1. Track & Trace: Monitor each batch across your supply chain in real time.
2. Non-Cloneable Labels: Assign a unique identity to every batch; no duplicates, no counterfeits.
3. Blockchain Integration: Lock each batch's data securely, preventing tampering or unauthorised changes.
4. QR Code Verification: Allow partners and customers to verify authenticity instantly.
5. Compliance Readiness: Stay ahead of evolving traceability laws and industry standards.
These features give you full control and visibility, critical when managing multiple batches or product lines.
Conclusion
The capacity to react quickly without sacrificing quality becomes more crucial as production methods change. Batch production offers the best possible combination of efficiency, flexibility, and scalability. However, without the necessary technologies, gaps in traceability and inefficiencies may arise.
With solutions driven by AI, IoT, and blockchain, your batch production line may operate safely, legally, and as efficiently as possible.
It is time to consider improved batch management solutions if you want to enhance your operations, boost transparency, and safeguard your reputation.
Partner with Acviss Solutions today. Discover how our authentication and traceability tools can transform your production process, one secure batch at a time. Get in touch with us and start building a smarter, more secure production line.