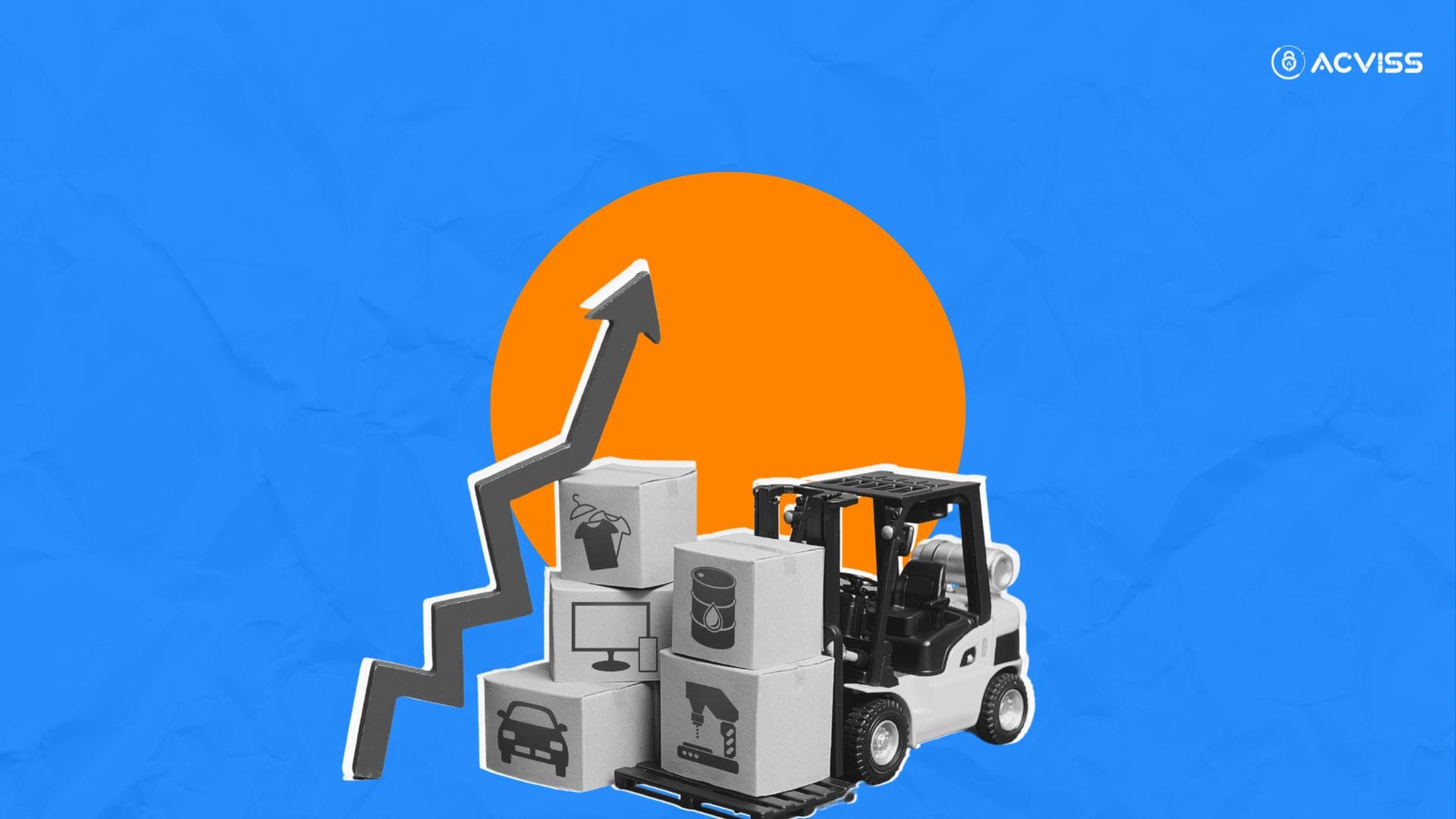
A spike in demand, a promising forecast, a strategic hunch, businesses ramp up production, eager to stay ahead of the curve. After all, having too much stock seems better than having none at all, right? But this well-meaning drive to prepare, scale, and satisfy often veers into dangerous territory: overproduction.
It’s not just about unsold inventory gathering dust in a warehouse. Overproduction quietly chips away at profits, clogs supply chains, drains resources, and leaves a trail of waste behind. What looks like a bold move toward market readiness can become one of the most expensive mistakes a business makes, both financially and environmentally.
Overproduction isn’t just a logistical inconvenience. It’s a systemic inefficiency. And its impact is far deeper than unsold stock.
When “More” Isn’t Better: The Subtle Start of Overproduction
Overproduction doesn’t always stem from negligence. It often arises from a desire to prevent stockouts, exploit full-capacity operations, or reduce per-unit manufacturing costs. But the reality is, these assumptions rarely consider shifting consumer behaviour, real-time demand insights, and the rising cost of storage and disposal.
In an age of just-in-time delivery and digital forecasting, producing more than necessary is no longer a sign of preparedness, it’s a liability.
The Tangible and Intangible Costs of Overproduction
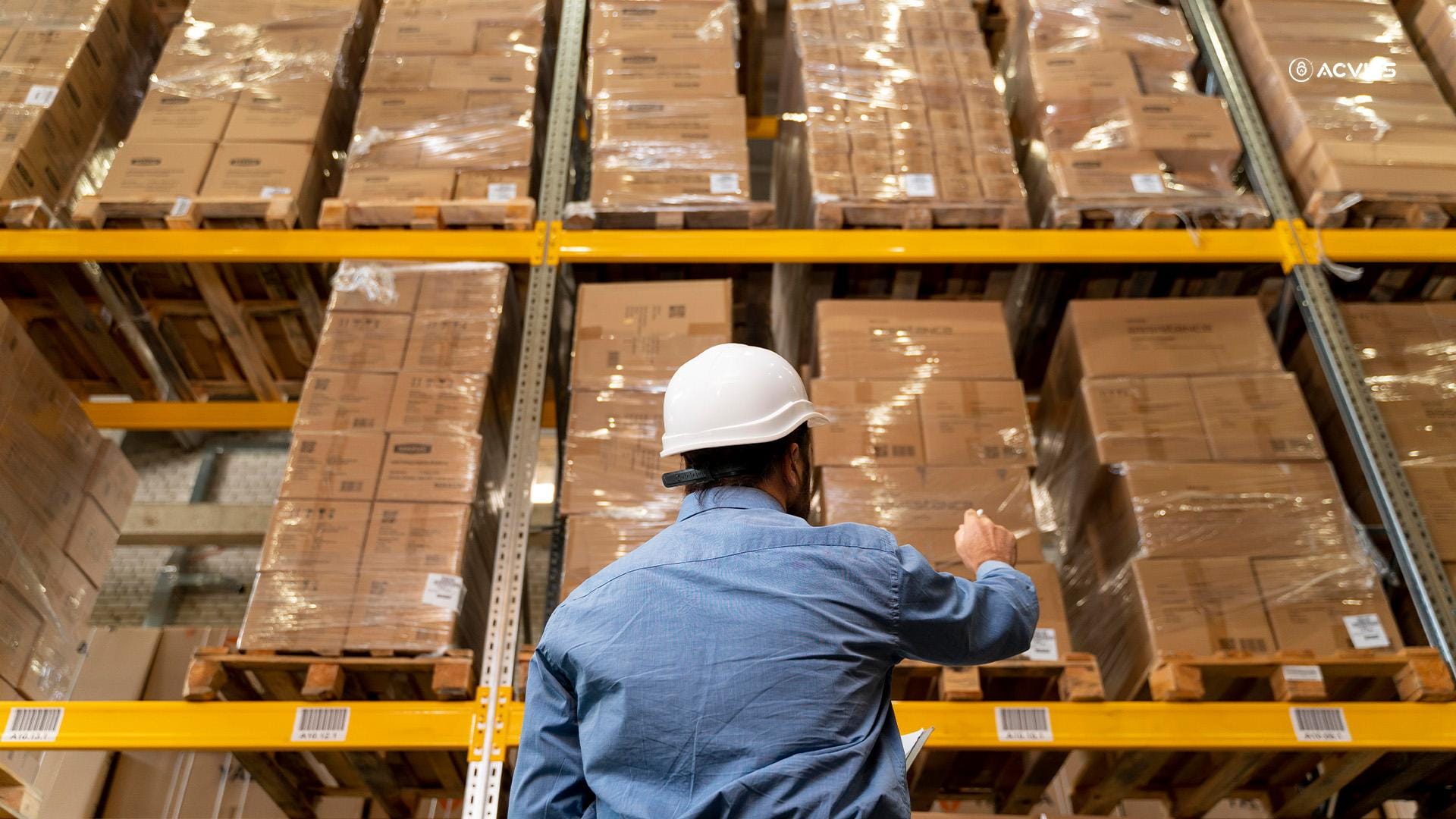
Overproduction incurs far more than just excess inventory. Its costs span multiple dimensions, some visible on the balance sheet, others buried in operational inefficiencies and reputational risks.
1. Inventory Holding and Warehousing Drain
Every excess unit produced needs a place to stay. That space, whether a high-tech warehouse with climate control or a simple pallet in a godown, comes at a cost. Rent, security, climate management, handling, and insurance charges accumulate rapidly. Even a modest buffer stock, when extrapolated across hundreds of SKUs, can result in idle capital.
Worse, the longer products stay unsold, the more they depreciate. Seasonal goods lose relevance. Technology products become obsolete. Perishables expire. The result: a warehouse full of sunk costs, depreciating assets, and locked working capital.
2. Cash Flow Obstruction
In financial terms, overproduction represents working capital converted into unsellable inventory. This diverts funds away from growth initiatives, innovation, or procurement of in-demand items. Businesses often misinterpret this as a cash shortage when, in reality, they are facing liquidity starvation caused by asset misallocation.
Instead of investing in marketing, R&D, or employee development, funds are tied up in managing and maintaining unsold goods. In many industries, this leads to discounting wars, write-offs, or worse, dumping practices that damage long-term brand equity.
3. Environmental Degradation and Waste
A less visible but more alarming impact of overproduction is its toll on the environment. When companies produce beyond need, they consume more raw materials, energy, water, and transportation resources. What doesn’t sell often ends up as waste, burned, buried, or dumped, creating a linear cycle of extraction, production, and disposal.
Fashion brands have come under scrutiny for this. A 2018 report exposed how several high-street apparel brands incinerated unsold stock worth millions every year to protect brand image and pricing structure. Not only does this contribute to greenhouse gas emissions, but it also represents a tragic misuse of finite resources.
4. Operational Inefficiencies and Overburden
Production systems designed to run at maximum capacity often push beyond optimal levels when targeting volume over demand. The result is increased wear and tear on machinery, higher maintenance needs, more frequent downtimes, and overstretched human resources.
Employees working in such systems face burnout and disengagement, while machines running beyond sustainable limits show reduced longevity and greater error rates. Ironically, in trying to be efficient through scale, systems become inefficient through overuse.
5. Missed Opportunities and Inflexibility
Excess inventory from overproduction also reduces a business’s agility. When resources are tied to products that may not move, companies find it hard to pivot quickly in response to market signals. New trends, product updates, or strategic shifts are hindered because the current stock must be cleared first.
For example, in the tech sector, holding a warehouse of slightly older devices can prevent the timely rollout of upgraded versions. In pharmaceuticals, regulations may require recalls or relabelling, impossible if excess stock has already been shipped or is awaiting expiry.
Real-World Examples of Overproduction Gone Wrong
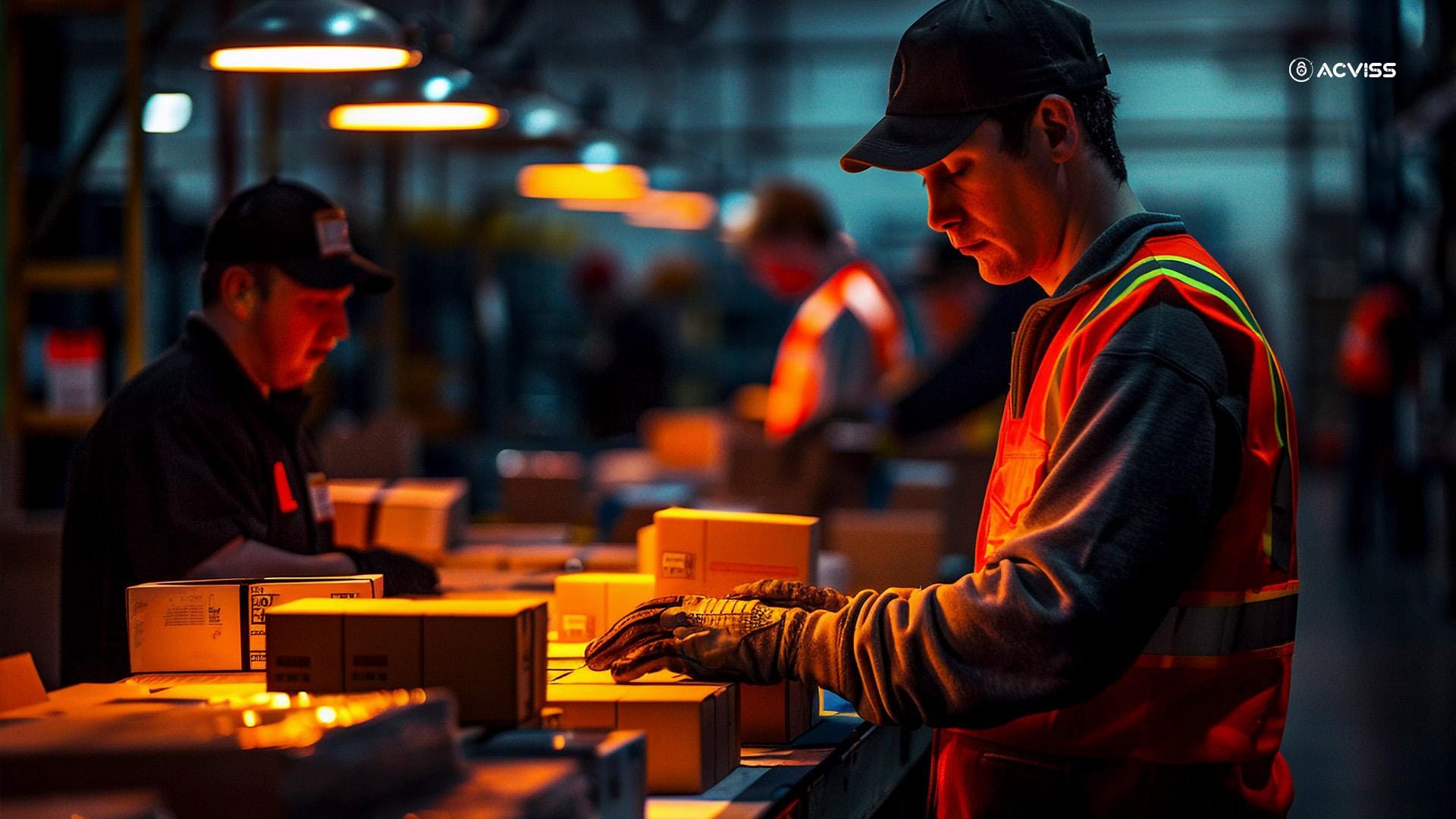
1. Zara’s Inventory Overhaul
Zara, one of the few fashion retailers praised for avoiding overproduction, didn’t always get it right. Early in its growth, the company faced significant losses in Southern Europe, where regional warehouses stocked excessive quantities of fashion lines that failed to resonate locally. The unsold apparel led to deep markdowns and brand dilution.
Learning from this, Zara adopted a demand-driven model, small batch production, rapid replenishment cycles, and hyper-local demand sensing. This shift helped it significantly reduce excess inventory and strengthen margins.
2. General Motors in the 1980s
GM’s attempts to outpace Japanese automakers led to a production surge in the 1980s. But the demand for many models never matched the inflated forecasts. Vehicles piled up in dealer lots, leading to aggressive discounting and reputational damage. Overproduction forced the company into an expensive cycle of markdowns and incentive programmes that strained profitability for years.
The lesson? Scale without demand is not growth, it’s debt.
3. Agricultural Overproduction and Government Buybacks
In agriculture, particularly in the U.S. and parts of Europe, overproduction is chronic. Government subsidies often incentivise farmers to produce more than needed, especially of wheat, corn, and milk. The result? Surpluses that require government buybacks or export dumping disrupt global markets and cause volatility for smaller producers in developing economies.
Worse, this also leads to unsustainable land use, degradation of soil quality, and wastage of water, commodities already under pressure from climate change.
Root Causes of Overproduction
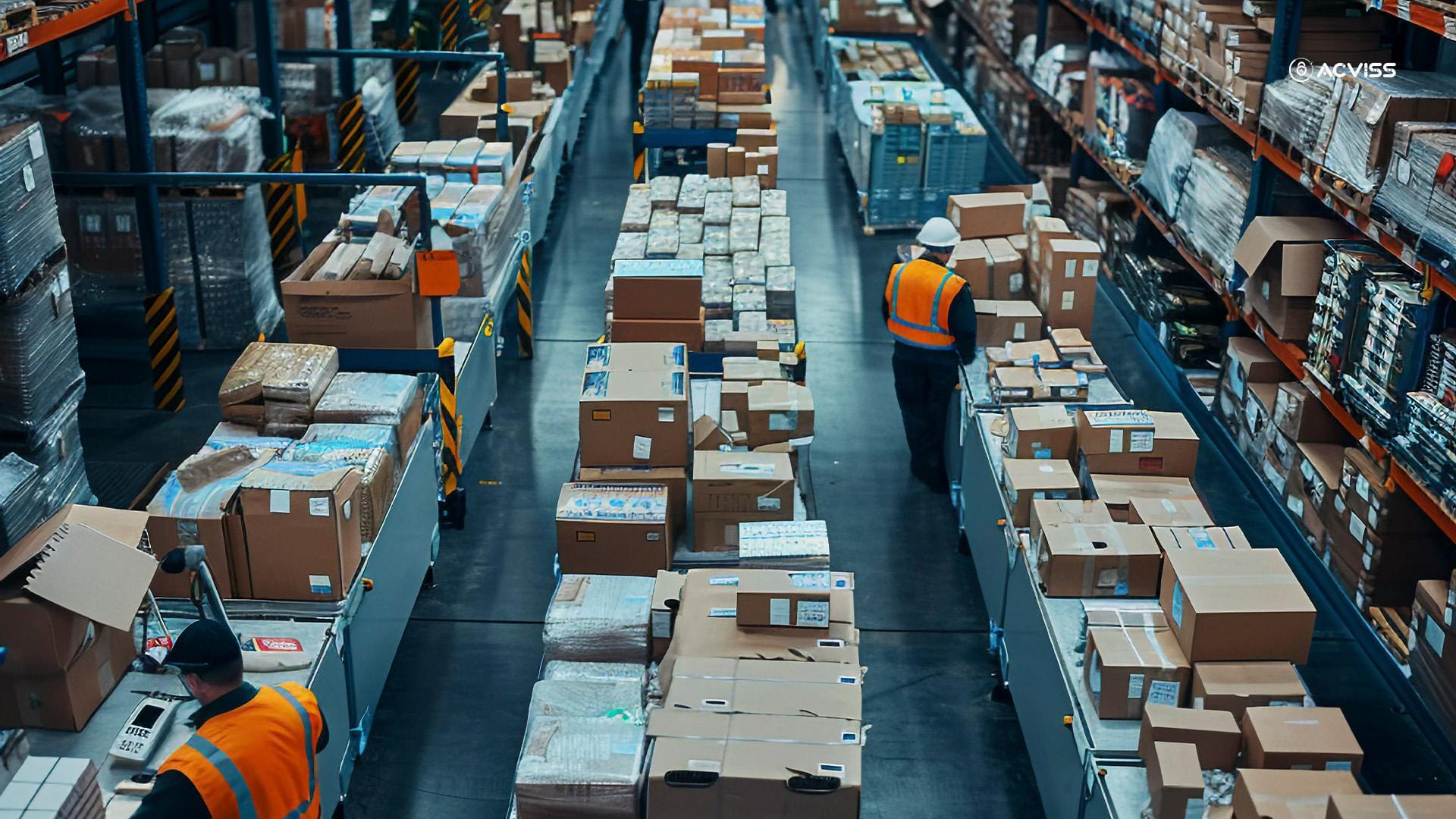
Understanding the drivers of overproduction is crucial to developing systemic solutions. Key factors include:
- Forecasting inaccuracies driven by outdated or rigid demand models
- Push-based manufacturing systems focused on maximum capacity utilisation
- Disconnected sales and production planning, where market feedback loops are weak
- Overreliance on economies of scale without factoring in storage and obsolescence costs
- Short-term KPIs that reward output quantity over inventory efficiency
Recognising these systemic roots allows companies to design more resilient and demand-driven systems.
Practical Solutions to Combat Overproduction
Addressing overproduction requires a combination of technological intervention, strategic alignment, and cultural change. The following approaches have shown real-world success.
1. Demand-Driven Manufacturing
The shift from forecast-based to demand-driven production is the most impactful transition. Technologies like advanced analytics, AI-driven demand sensing, and dynamic inventory modelling allow companies to sync production closer to real-time market needs.
Procter & Gamble, for instance, leveraged predictive analytics to fine-tune its production lines for high-velocity SKUs, reducing overproduction by over 20% across certain product lines in just two years.
2. Digital Twins and Simulation Modelling
Digital twin technology allows manufacturers to simulate production and demand in virtual environments before committing resources. By modelling different scenarios, companies can understand the risks of overproduction, test lean strategies, and validate product mixes without physical output.
This is particularly relevant in capital-intensive industries like aerospace or heavy engineering, where every batch represents a significant investment.
3. Agile Supply Chains and Just-in-Time (JIT) Systems
Toyota’s just-in-time methodology remains a gold standard in avoiding overproduction. By focusing on replenishment only when needed, Toyota minimises waste and enhances flexibility. This model requires strong supplier relationships, real-time data exchange, and impeccable coordination, but the results speak for themselves.
Modern JIT systems, bolstered by IoT and ERP integrations, enable even mid-sized manufacturers to embrace similar agility.
4. Product Life Cycle Synchronisation
Aligning production with product lifecycle stages helps companies prevent overproduction of maturing or declining products. This involves tighter coordination between R&D, marketing, and operations teams. For instance, a company nearing the end of a model’s lifecycle should taper production, manage promotions strategically, and transition marketing efforts toward new launches.
Tech companies like Apple carefully manage supply and phase-outs during product transitions, ensuring minimal obsolete stock.
5. Circular Economy and Reverse Logistics
Even with the best efforts, some overproduction may be unavoidable. In such cases, building a circular economy approach, through product take-back schemes, upcycling, and repurposing, can help extract value from excess stock.
For example, IKEA has invested in reverse logistics to collect unsold furniture and recondition it for resale at a discount or donation, significantly reducing landfill contribution and reinforcing its sustainability credentials.
Looking Ahead: Overproduction in a Sustainable Future
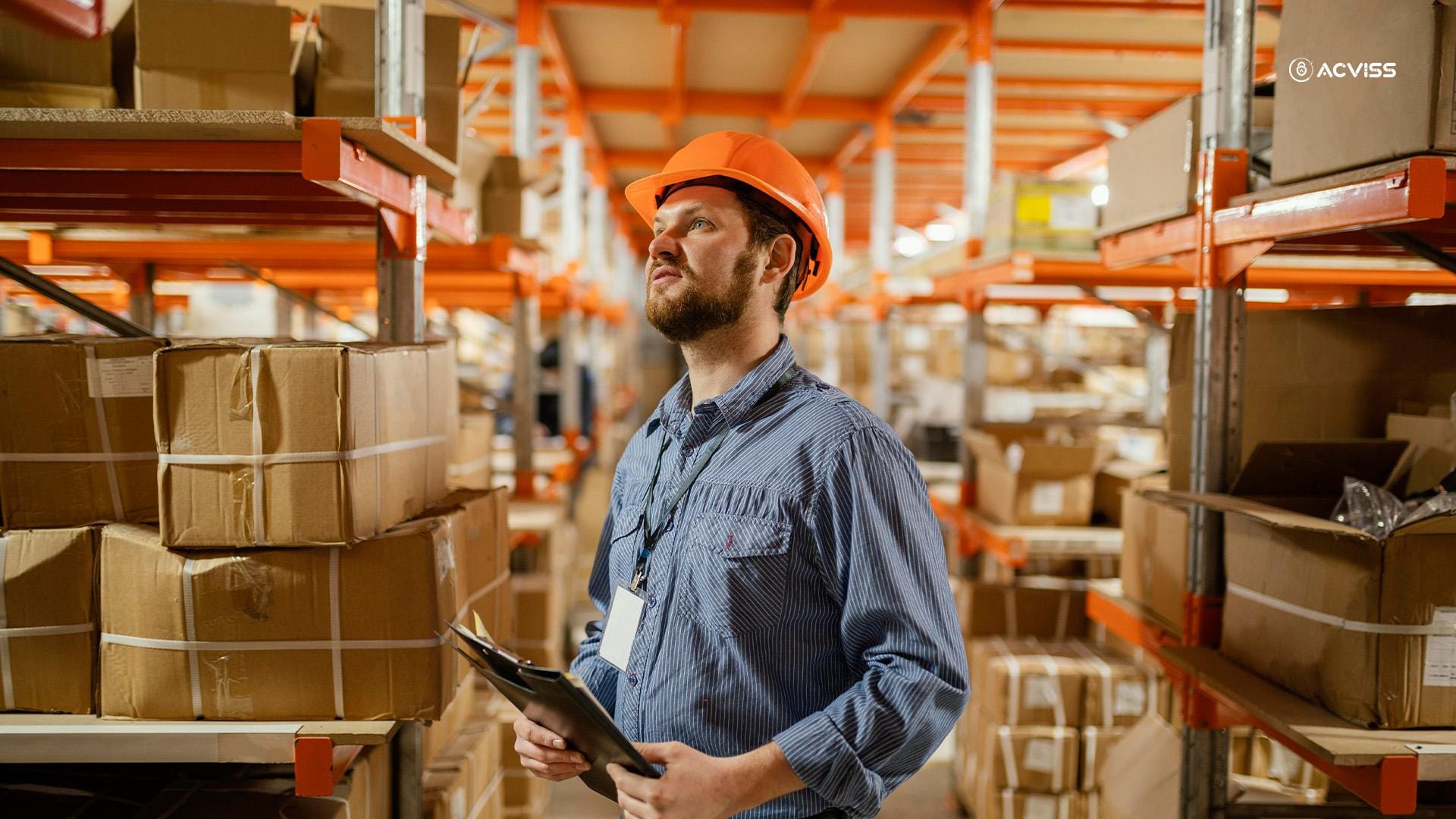
As ESG pressures mount and consumer consciousness rises, the tolerance for overproduction is diminishing. Investors, regulators, and consumers now scrutinise waste and inefficiency as signs of poor governance and short-termism.
The future belongs to manufacturers who can produce precisely what’s needed, when it’s needed, and in the quantity it’s needed. That requires investment in data systems, culture shifts in operations, and an unwavering commitment to lean, intelligent production.
Conclusion
Overproduction is a relic of an era when success was measured in volume, not value. In the modern economy, driven by customisation, agility, and sustainability, producing more than the market requires is no longer a strategy. It’s a risk.
Companies that recognise this shift and recalibrate their systems accordingly will not only save costs but unlock agility, customer trust, and resilience in the process.
Because in the end, the future isn’t about making more. It’s about being smart.
If you're ready to take control of your production, protect your brand, and eliminate wasteful inefficiencies, it's time to see how Acviss can help.
Request a demo today and discover how our intelligent track and trace solutions can transform your supply chain with precision, visibility, and control.