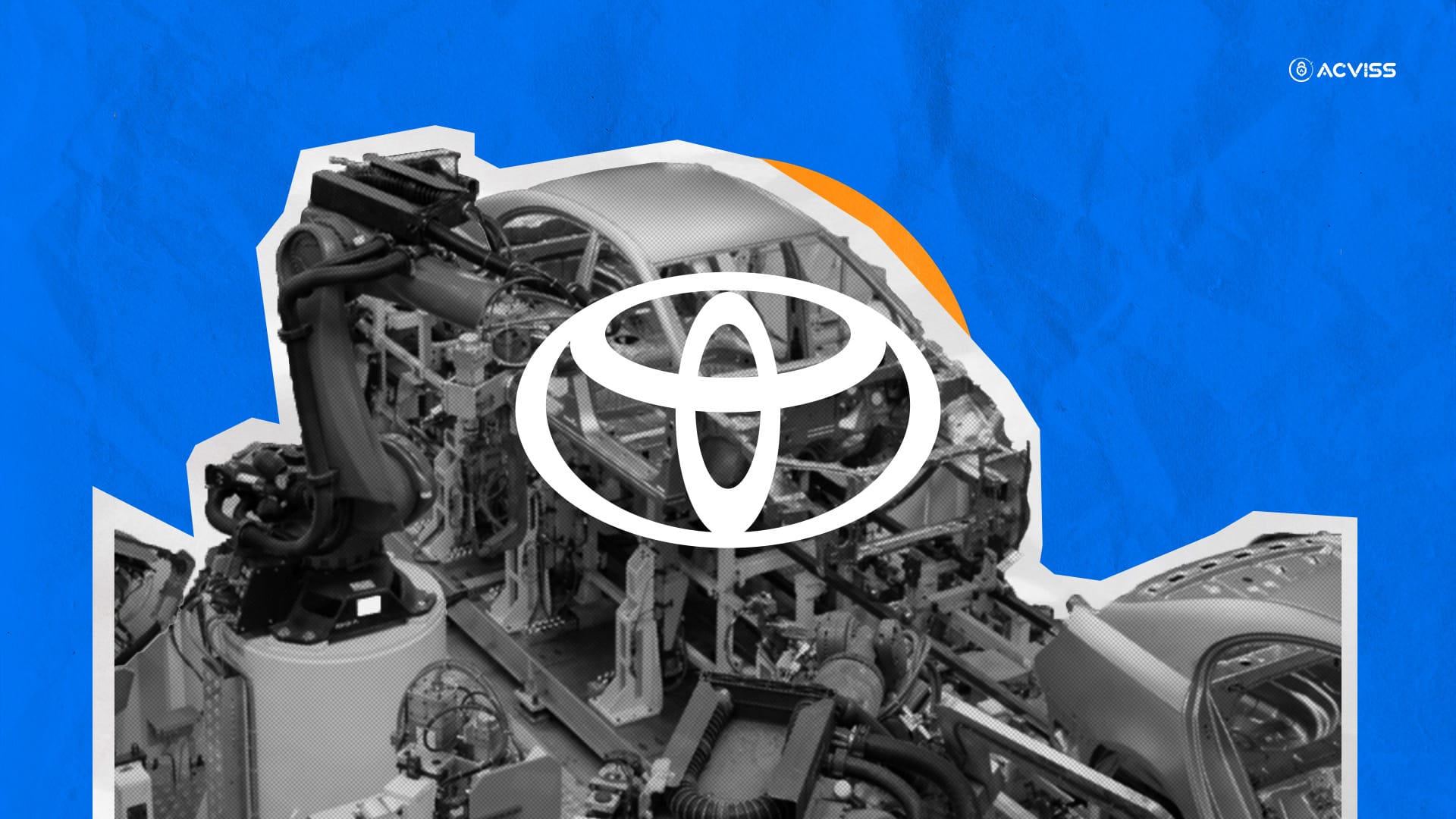
Manufacturing has come a long way over the decades. There have been many developments, changes, and iterations in how things work in manufacturing today. However, one system developed in post-war Japan will still be the base of any manufacturing process. The Toyota Production System (TPS), created by Toyota Motor Corporation, set a standard for how things could be made faster, smarter, and with almost no waste. It wasn’t just about building cars; it was about building better processes.
TPS was built on two powerful ideas:
- Just-in-Time (JIT) production
- Jidoka, or automation with a human touch.
Together, these philosophies introduced a lean, efficient way to manufacture goods. These philosophies reduced excess inventory, improved product quality, and encouraged continuous team improvement.
Modern manufacturers today are still facing some big challenges: the pressure to produce faster, prevent counterfeit products, trace every step of the supply chain, and meet rising consumer expectations. And even now, TPS offers a strong foundation to tackle them.
What makes TPS so remarkable and timeless? Many of today’s most advanced practices, like track and trace systems, manufacturing process optimisation, and product traceability in manufacturing, all echo the very principles that Toyota introduced decades ago.
In this blog, we’ll explore how TPS revolutionised manufacturing, how its lessons are still relevant today, and how new technologies are taking these ideas even further into the future.
What is the Toyota Production System (TPS)?
The Toyota Production System (TPS) is a set of manufacturing techniques that transformed how products are made around the world.
It all started in post-World War II Japan when Toyota faced a big challenge: limited resources. Unlike American manufacturers, Toyota couldn’t afford to overproduce or stockpile inventory. So, they had to find a smarter way to work. That need gave birth to TPS.
TPS are two key ideas:
- Just-in-Time (JIT): Produce only what’s needed, when it’s needed, and in the amount needed. No excess, no waste. This kept inventory low, saved money, and made production more flexible.
- Jidoka (Automation with a Human Touch): If a problem happens during production, stop everything and fix it immediately. Machines were designed to stop automatically when something went wrong, and workers were empowered to do the same. This helped maintain quality at every step, not just at the end.
Together, these philosophies introduced what we now call lean manufacturing. It is a technique where one focuses on eliminating anything that doesn’t add value. That includes excess materials, time, movement, or even overprocessing.
TPS taught the world that efficiency doesn’t mean cutting corners. It means removing the clutter, solving problems early, and building better systems over time. That’s a lesson that still shapes modern manufacturing today.
Key Pillars of TPS That Transformed Manufacturing
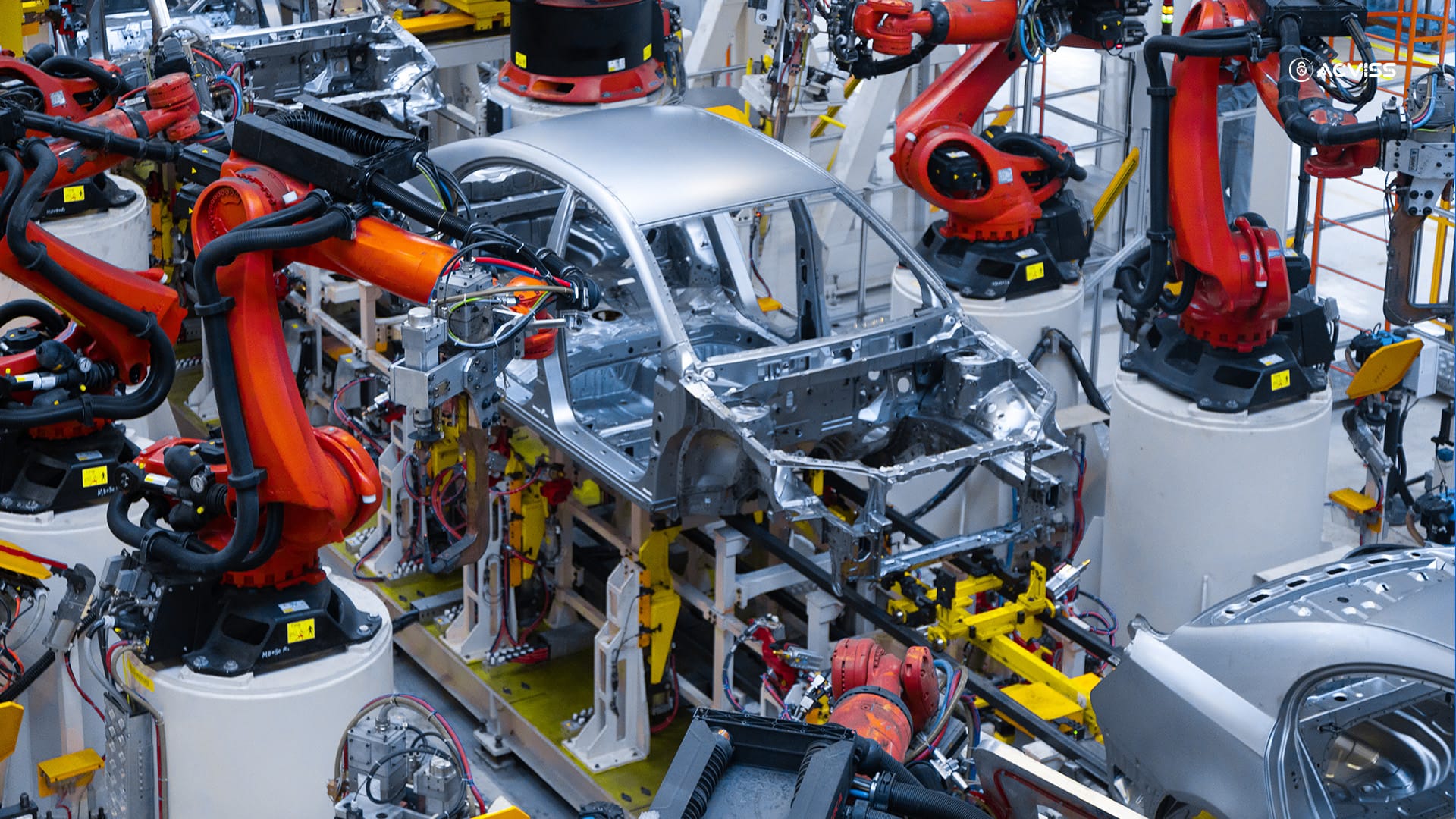
The Toyota Production System may seem simple on the surface, but it’s built on strong, well-defined pillars that continue to guide manufacturing practices across the world. Let’s break down these three core principles:
1. Just-in-Time (JIT)
Just-in-Time is all about producing exactly what’s needed, when it’s needed, and in just the right amount.
Instead of overstocking parts or building excess products, JIT ensures that every process flows smoothly, like a well-oiled machine. It reduces inventory waste, lowers storage costs, and keeps factories nimble and responsive.
For modern manufacturers, this translates to:
- Less clutter, both physically and operationally.
- Shorter lead times mean products get to market faster.
- Better use of resources, which improves cost-efficiency.
In short, JIT laid the foundation for what we now call efficient manufacturing systems.
2. Jidoka
Jidoka means "automation with a human touch." It might sound fancy, but here’s the idea:
Machines can stop themselves when something goes wrong. And workers are encouraged to pause production if they spot a defect.
This approach builds quality right into the process instead of trying to fix things later. It prevents defects from passing through unnoticed and empowers people to take responsibility for quality on the spot.
Jidoka ensures that:
- Mistakes are caught early.
- Quality is everyone’s job.
- Machines work smartly, not just automatically.
This principle still plays a huge role in modern quality control systems used by top manufacturing brands.
Kaizen & Continuous Improvement
Kaizen is the Japanese word for “change for the better,” and it’s a core part of TPS.
The idea is simple: small, consistent improvements over time lead to big results. Everyone in the organisation, from the factory floor to management, is encouraged to contribute ideas to make things better.
This mindset has become a global standard for manufacturing process optimisation, and it fuels a culture of:
- Continuous learning.
- Team collaboration.
- Innovation is driven from within.
Kaizen reminds us that you don’t need a big overhaul to improve; sometimes, just one small fix at a time can transform how a factory operates.
Together, JIT, Jidoka, and Kaizen created a system that didn’t just improve Toyota, it transformed manufacturing worldwide.
How TPS Influenced Modern Manufacturing Practices
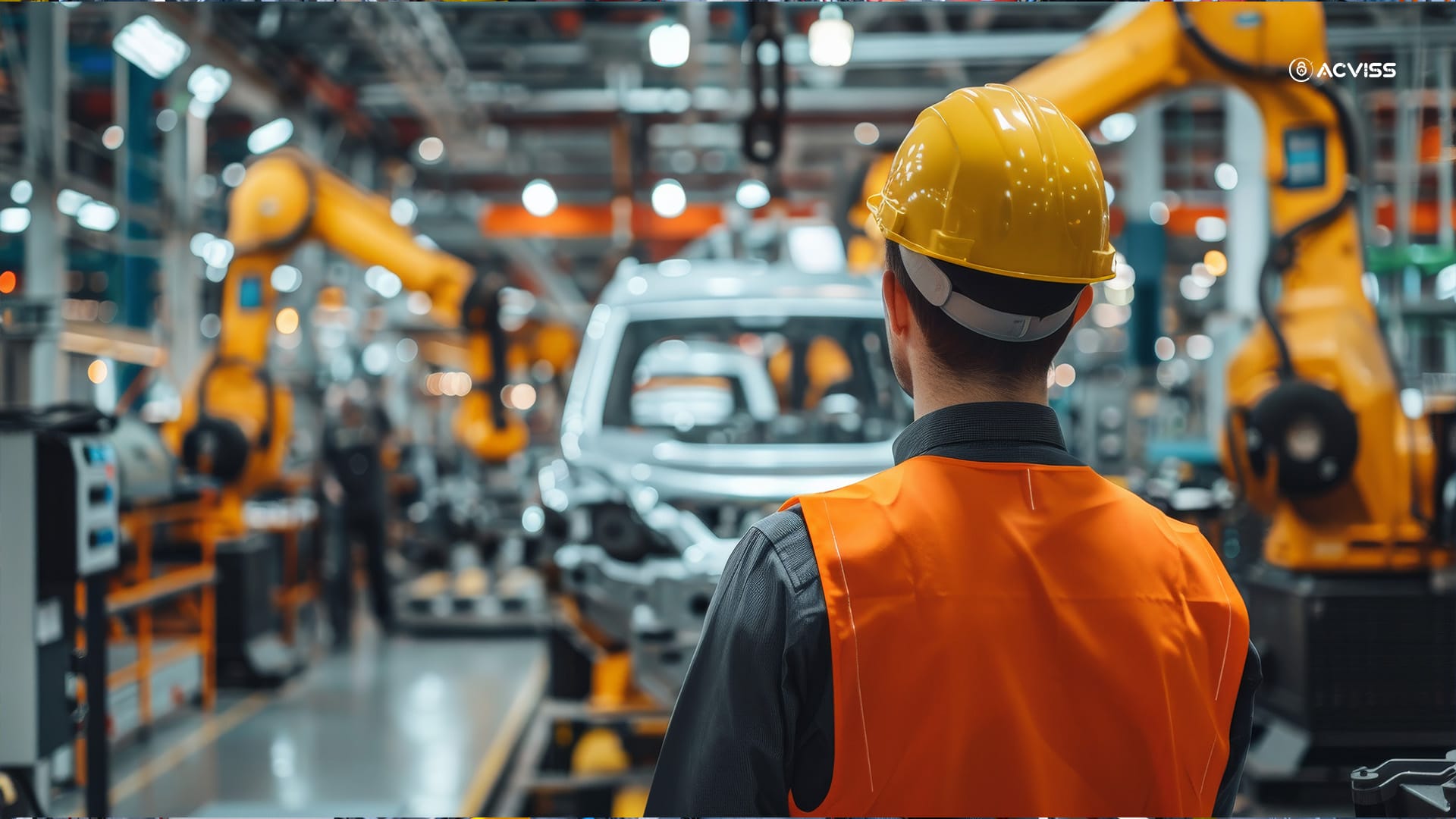
The Toyota Production System (TPS) didn’t just change how Toyota made cars; it completely reshaped how the world thinks about manufacturing. Its influence is visible in nearly every industry today, especially where speed, quality, and traceability matter.
1. From Mass Production to Lean Thinking
Before TPS, the focus was on mass production. Make more, faster, and cheaper. But that often led to waste, overproduction, and defects. TPS introduced the world to lean manufacturing, a system built on eliminating waste, improving flow, and delivering more value with fewer resources.
Now, companies everywhere aim to:
- Build what’s needed instead of overproducing.
- Design smarter, more flexible production lines.
- Respond quickly to customer demands and market changes.
This shift has made manufacturing more agile and sustainable than ever before.
2. Rise of Track and Trace Systems
TPS also laid the groundwork for better visibility and accountability in supply chains. Modern companies now use track and trace systems to monitor every step of a product’s journey, from raw materials to end-user delivery.
These systems help:
- Detect delays or bottlenecks early.
- Prevent counterfeit or substandard products from entering the chain.
- Support real-time decision-making based on accurate data.
In many industries, product traceability in manufacturing has become non-negotiable, not just for efficiency but for safety and compliance, too.
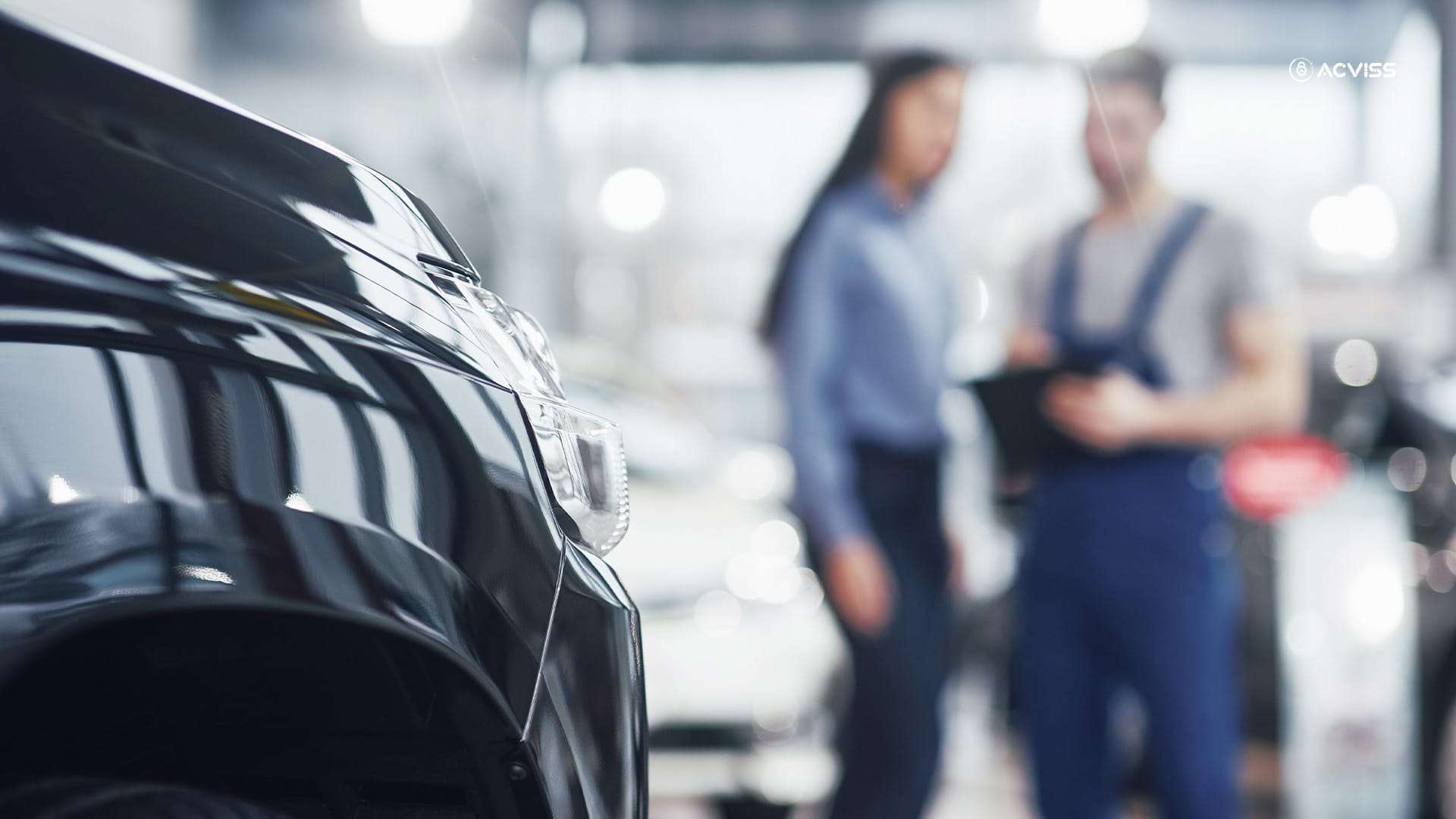
3. Standardisation as a Defence Against Counterfeiting
TPS encouraged standardised processes and high-quality standards, which naturally translated into stronger safeguards against counterfeiting. When every product follows a strict and traceable process, it becomes much harder for fakes to slip through.
This has inspired the adoption of:
- Anti-counterfeiting in supply chain strategies.
- Serial-numbered packaging and authentication systems.
- Stronger enforcement of quality checkpoints.
4. Smarter, Data-Driven Decision Making
TPS encourages real-time problem-solving and continuous improvement. Today, this has evolved into smart manufacturing, where data from machines, sensors, and systems is used to drive improvements.
Thanks to this evolution, brands can:
- Predict maintenance needs and avoid downtime.
- Optimise inventory levels and material flow.
- Quickly respond to disruptions, whether it’s a delay in shipping or a sudden spike in demand.
5. Building a Culture of Ownership
One of the most underrated but powerful contributions of TPS is culture. It shifted how people view their roles in manufacturing; everyone is responsible for quality, efficiency, and improvement.
This mindset:
- Improves teamwork and accountability.
- Encourages problem-solving at every level.
- Builds long-term trust between brands and their customers.
In short, the Toyota Production System didn’t just optimise factories, it inspired a complete transformation of how we think, work, and build in manufacturing.
Real-World Impact of TPS Principles
Once other manufacturers saw the success of TPS, they began adapting its principles to suit their own operations. The result? A global shift in how products are built, with greater speed, precision, and purpose.
Here are some real-world impacts of TPS –
1. Global Brands That Embraced TPS
Many industry giants across the world have adopted TPS-inspired practices to improve efficiency and competitiveness. Some notable examples include:
- Ford: Adapted lean manufacturing and JIT systems to streamline production across its global plants.
- Boeing: Implemented lean principles to reduce waste in aerospace manufacturing, saving billions in costs.
- Nike: Uses lean thinking not only in production but also to empower workers and improve factory conditions.
- Harley-Davidson: Revamped its operations using TPS to increase flexibility and reduce manufacturing time.
- Caterpillar: Applied lean principles to reduce inventory and improve part delivery across its supply chain.
2. Measurable Improvements in Efficiency and Quality
Companies that adopted TPS principles saw a range of tangible benefits, including:
- Shorter Lead Times: Products reach the market faster without compromising quality.
- Reduced Waste: Lower raw material usage, energy consumption, and excess inventory.
- Better Quality Control: Fewer product defects, resulting in less rework and higher customer satisfaction.
- Higher Workforce Engagement: Employees are more involved in innovation and problem-solving.
- Greater Profit Margins: By reducing waste and improving processes, costs go down, and profits go up.
3. Strengthening Supply Chain Trust & Product Authenticity
TPS principles, especially those related to standardisation, quality checks, and process visibility, have made it easier to implement modern manufacturing authenticity solutions. These include:
- Serialised packaging and labelling, which ensures every product can be tracked and verified.
- Clear, auditable processes reduce the chances of counterfeit parts entering the system.
- Integrated traceability systems help manufacturers detect anomalies before they impact customers.
4. TPS as a Catalyst for Innovation
While TPS was born out of necessity, it evolved into a philosophy that drives continuous innovation. Many manufacturers now use TPS not just for efficiency, but as a framework for digital transformation.
- AI-powered quality control, inspired by Jidoka.
- Real-time supply chain monitoring, building on JIT logistics.
- Predictive analytics for inventory, grounded in lean thinking.
The Relevance of TPS in the Digital Era
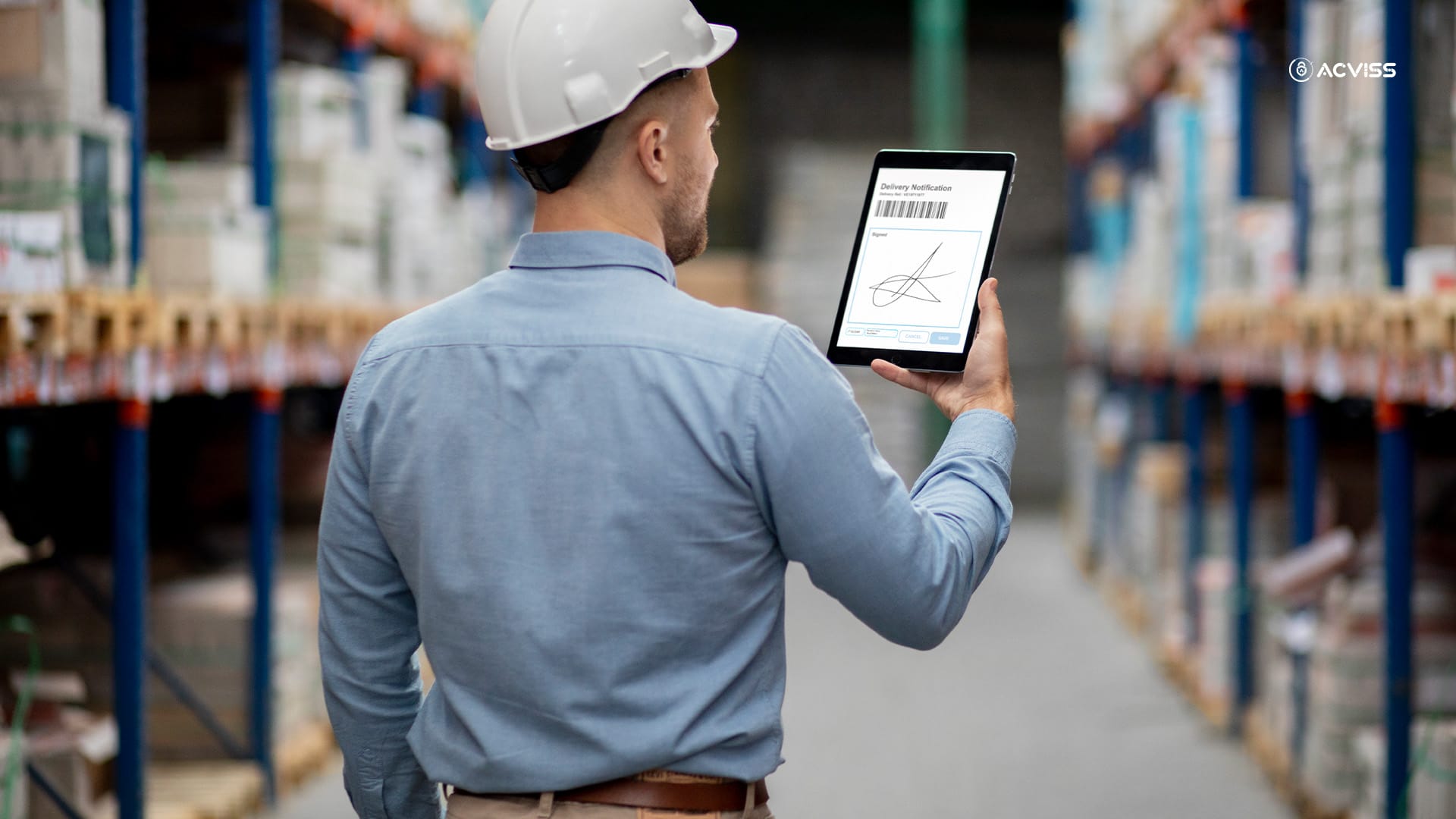
TPS is more relevant today than ever before as manufacturers race to meet the demands of a faster, smarter, and more transparent supply chain.
1. Integrating TPS with AI, IoT, and Blockchain
Modern manufacturing is powered by real-time data, automation, and smart systems. Luckily, TPS was built on adaptability. Now, its values are being supercharged by:
- AI (Artificial Intelligence): Automatically identifies inefficiencies, predicts maintenance, and flags defects—pushing Jidoka (automation with a human touch) to new heights.
- IoT (Internet of Things): Sensors on machines and products feed live data into production lines, enhancing Just-in-Time operations and minimising waste.
- Blockchain: Builds a transparent and unalterable chain of custody for products, aligning with TPS’s commitment to quality, authenticity, and continuous improvement.
2. The Growing Need for Product Traceability in Manufacturing
As global supply chains stretch across borders, manufacturers must know exactly where their products are and where they’ve been. Traceability isn’t just a nice-to-have anymore; it’s critical for:
- Regulatory compliance
- Recall readiness
- Anti-counterfeiting in the supply chain
- Consumer trust
TPS laid the foundation with its focus on visual control, standardisation, and accountability. Today, it’s being expanded with track and trace systems that offer granular visibility into every stage of the manufacturing process.
3. Addressing Cybersecurity and Counterfeit Threats
Modern supply chains aren’t just physical—they’re digital. And with digital transformation comes new challenges:
- Cybersecurity risks: Digital systems must be protected from breaches that can halt production or expose sensitive data.
- Counterfeiting: Without proper traceability and verification, fake products can enter even the most sophisticated systems.
- Compliance complexities: Global regulations are tightening, requiring end-to-end transparency and auditability.
TPS principles of quality control, error prevention, and root-cause analysis help companies navigate these digital risks. Pair that with modern anti-counterfeiting solutions, and brands are far more secure.
4. Accelerating Continuous Improvement Through Digital Tools
In the digital era, Kaizen goes beyond whiteboards and team huddles. Now, continuous improvement is driven by:
- Real-time dashboards
- Predictive analytics
- Cloud-based collaboration tools
- Instant feedback loops between production, supply chain, and customers
This leads to faster problem-solving, smarter decision-making, and a more connected workforce.
5. Agile, Customer-First Manufacturing
Finally, TPS taught the world to build what the customer needs when they need it, not just what the factory wants to produce. That’s more important than ever in a world of personalisation, e-commerce, and global demand shifts.
- Digitally enabled flexibility allows small production runs and quick changeovers.
- Smart scheduling ensures minimal downtime and optimal resource usage.
- Customer data drives better planning, design, and delivery.
In short, the Toyota Production System may have started on a factory floor in Japan, but today, its heart beats in cloud dashboards, blockchain ledgers, and AI-powered quality checks. It’s a timeless framework evolving for a digital future.
How Acviss Powers the Next-Gen TPS Vision
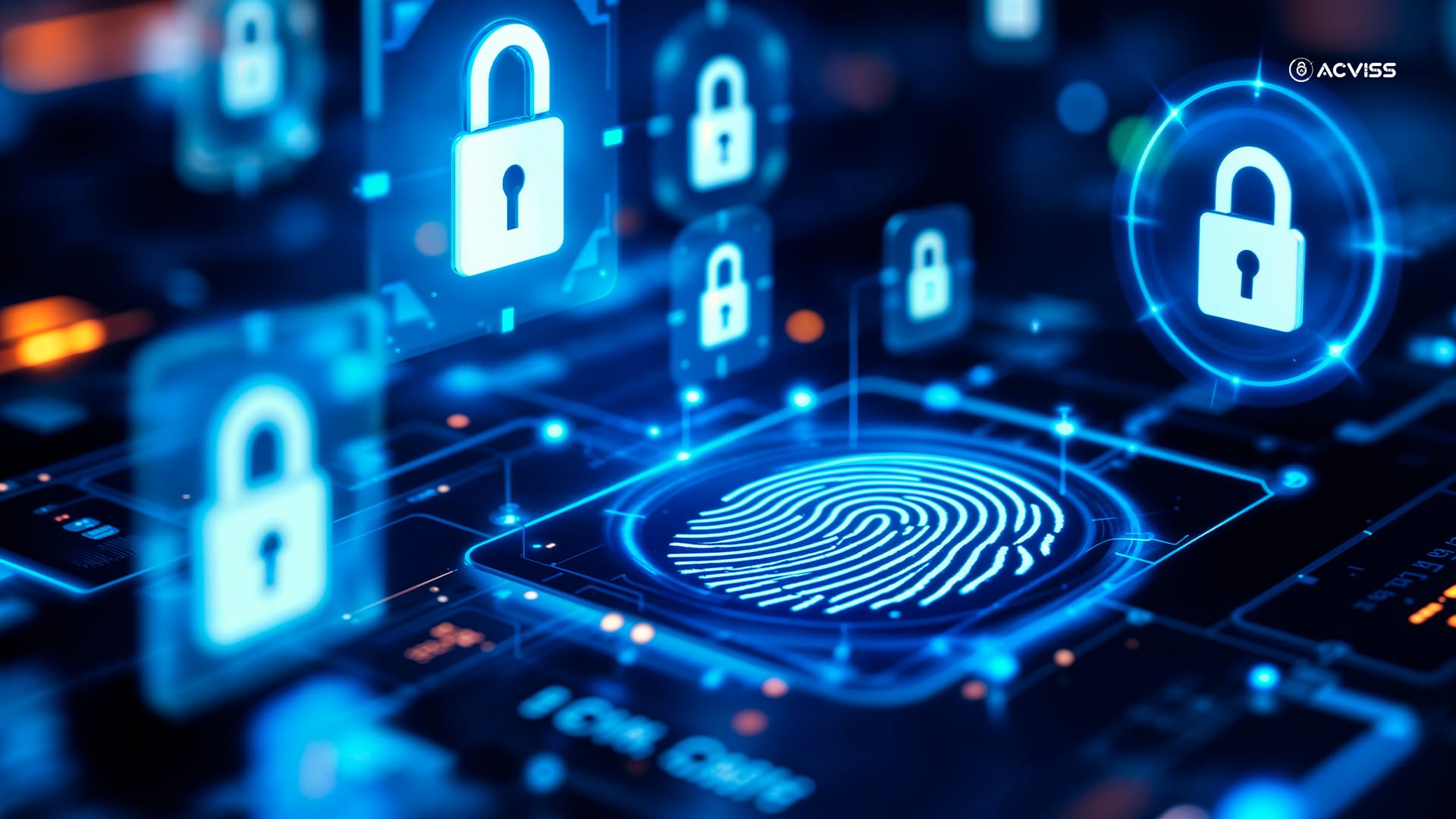
As manufacturing evolves, so do the challenges: counterfeit parts, lack of visibility, regulatory pressure, and cyber threats. That’s where Acviss steps in.
Acviss shares the same values as TPS: transparency, accountability, and continuous improvement. But it brings something new to the table—next-gen technology designed to secure modern manufacturing from the ground up.
1. Certify: Product Authentication and Anti-Counterfeiting
TPS believes in quality at every step. Certify ensures that quality is authentic.
- Every product gets a unique digital identity, allowing brands, suppliers, and even end customers to verify authenticity.
- By preventing fake components from entering the supply chain, Certify supports lean operations and reduces costly recalls or quality failures.
- It also builds customer trust, which is vital in competitive markets.
2. Truviss: AI-Powered Monitoring of Supply Chains
TPS emphasises proactive problem-solving. Truviss takes that a step further by spotting issues before they become problems.
- Using AI, it scans e-commerce platforms, B2B channels, and even social media to detect counterfeit listings and unauthorised sellers.
- Brands receive real-time alerts, enabling faster response and minimising damage.
- This aligns perfectly with Jidoka, where smart systems help maintain quality without constant human oversight.
4. Blockchain Supply Chain Tracking: For Transparency and Compliance
Just-in-Time only works when your entire supply chain is visible and reliable. Acviss brings blockchain into the mix to:
- Track every step of a product’s journey, from raw materials to finished goods.
- Create a tamper-proof record that meets global compliance standards.
- Provide instant traceability during audits, recalls, or customer complaints.
This supports manufacturing authenticity solutions that are both secure and scalable.
5. Building Efficient, Trust-Centred Manufacturing
Acviss helps brands create manufacturing systems that are:
- Secure – from raw material sourcing to customer delivery.
- Transparent – with real-time visibility into supply chain movements.
- Authentic – ensuring that every product is traceable and verifiable.
In other words, it brings the TPS philosophy into the digital era, where trust, efficiency, and innovation go hand-in-hand.
Conclusion
It’s fascinating how a system developed decades ago in a post-war factory continues to inspire how the world builds things today. The Toyota Production System
The manufacturing world is no longer just about speed or scale. It’s about trust, traceability, and resilience. In today’s digital-first, risk-heavy environment, it's not enough to produce efficiently—we need to produce securely.
That’s where tools like Acviss come in. They don’t replace the philosophies of TPS—they evolve them. By merging age-old principles with next-gen technologies, we’re building supply chains that aren’t just smart—they’re safe, transparent, and future-ready.
So here’s a thought: Maybe the future of manufacturing isn’t just about doing things faster or cheaper. Maybe it’s about doing them with clarity, integrity, and a whole lot more trust.
And if that’s the future you’re aiming for, Acviss is already there.