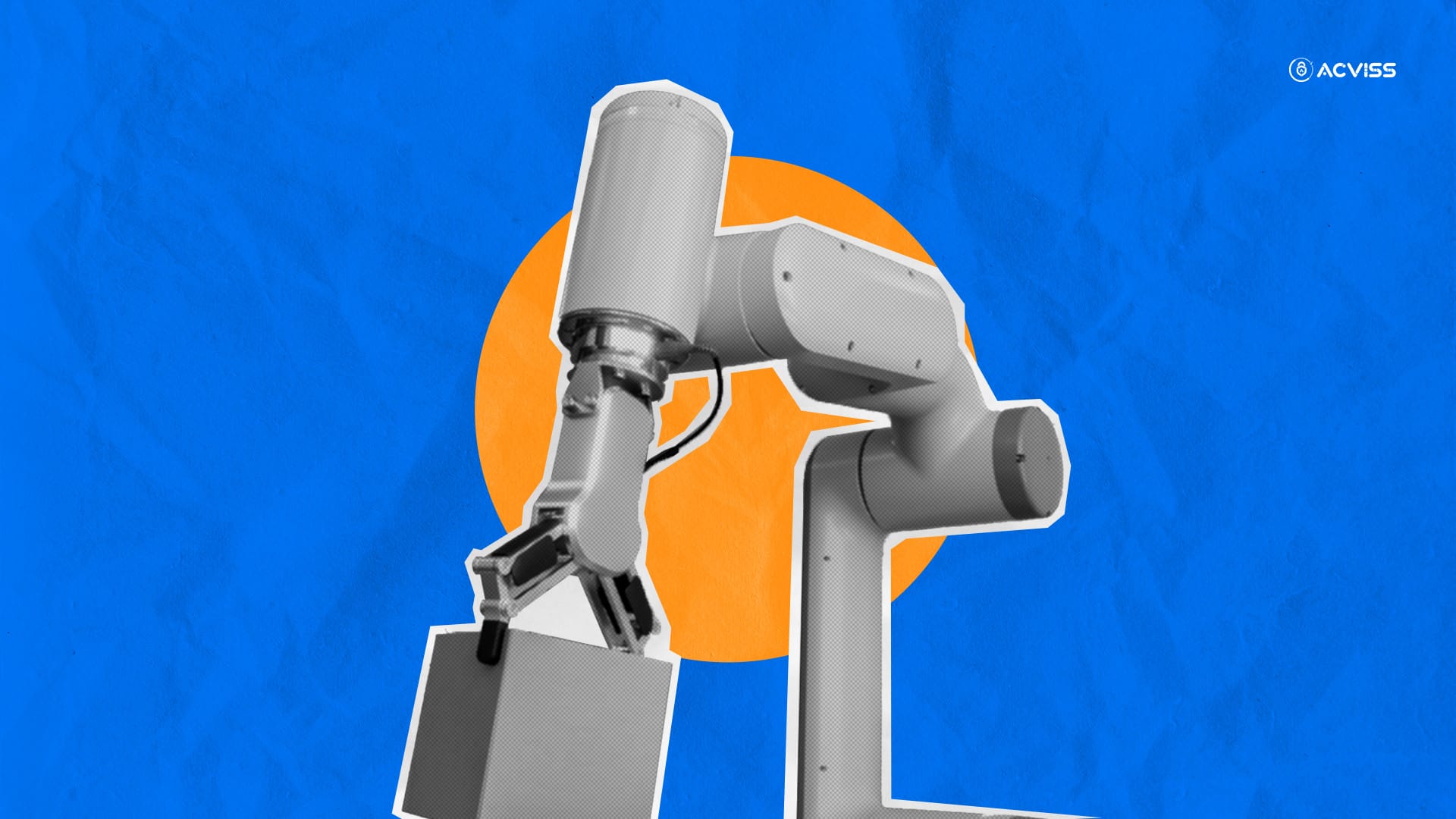
Many factories still rely heavily on manual processes. Not because they want to, but because change often feels complicated, expensive, or disruptive. Yet, as operations scale and customer expectations grow, these manual workflows start to show their cracks: delays, errors, rising costs, and an overdependence on people for tasks that could easily be handled by machines or software.
Explore the advanced landscape of factory automation, mapping out how traditional manual tasks can be transformed using modern technologies.
Understanding the Manual-Automation Divide
At its core, a manual process in a factory context refers to any activity executed by human hands without machine aid, be it assembly, inspection, packaging, or documentation. These processes often suffer from inconsistency, fatigue-induced errors, inefficiency, and scaling limitations.
In contrast, automated processes delegate such tasks to machines, software systems, and robotics. They rely on strict adherence to programmed instructions, ensuring speed, accuracy, and consistency. Automation allows manufacturers to move from reactive operations to predictive and data-driven ones.
But automation isn’t simply about replacing workers with robots. It’s about redefining workflows, augmenting human decision-making, and enabling smarter operations through digital transformation.
Why Automate Manual Processes?
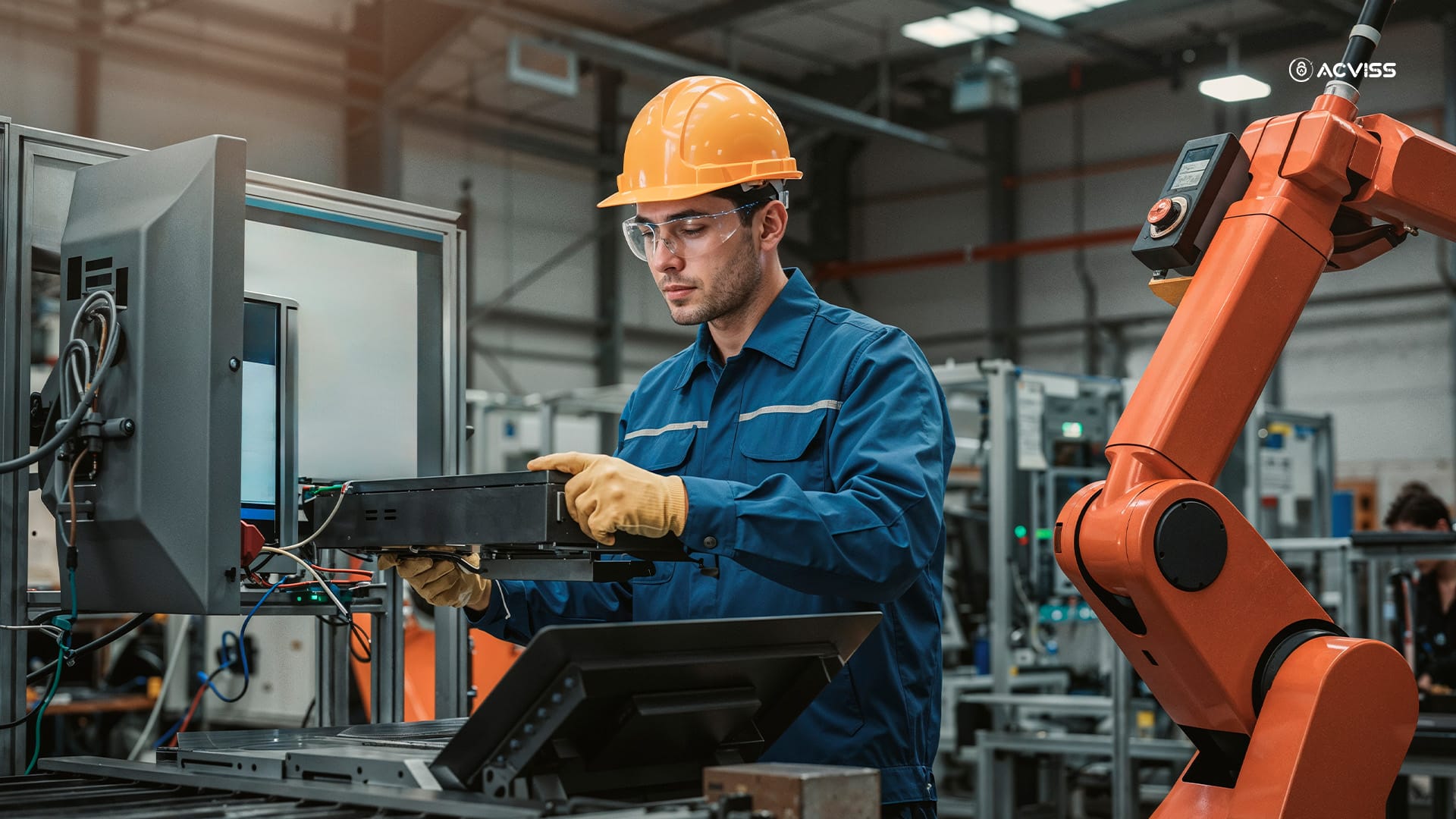
Before diving into the "how," it's crucial to understand the "why." Manufacturers pursue automation for several strategic reasons:
- Boosting Productivity: Machines operate 24/7 without breaks, enabling higher throughput.
- Reducing Human Error: Automated systems are governed by algorithms that eliminate variability.
- Improving Safety: Automation removes human workers from hazardous or repetitive environments.
- Enhancing Quality Control: AI-powered inspection systems can detect micro-defects that humans might overlook.
- Achieving Data Visibility: Every machine and system can become a sensor, feeding data to optimise performance.
In fact, automated factories have reported output gains of 20% to 140%, with improvements largely attributed to uninterrupted machine operation, real-time visibility, and AI-driven scheduling.
Manual Processes Ready for Automation
Let’s examine specific manual processes that are commonly automated, along with the technologies driving these transformations:
1. Assembly Operations
Manual assembly, such as screwing, welding, or component insertion, is repetitive and precision-sensitive. Robotic arms and cobots (collaborative robots) can be programmed to perform these tasks with near-perfect consistency. Tesla's Gigafactories are a benchmark in this regard, using automation across battery installation and final car assembly.
2. Material Handling
Moving raw materials or finished goods across a facility is labour-intensive. Automation replaces forklifts and human handlers with Autonomous Mobile Robots (AMRs) and conveyor systems, reducing labour while increasing efficiency. Amazon’s use of AMRs in warehouses has become a global standard for streamlined logistics.
3. Quality Inspection
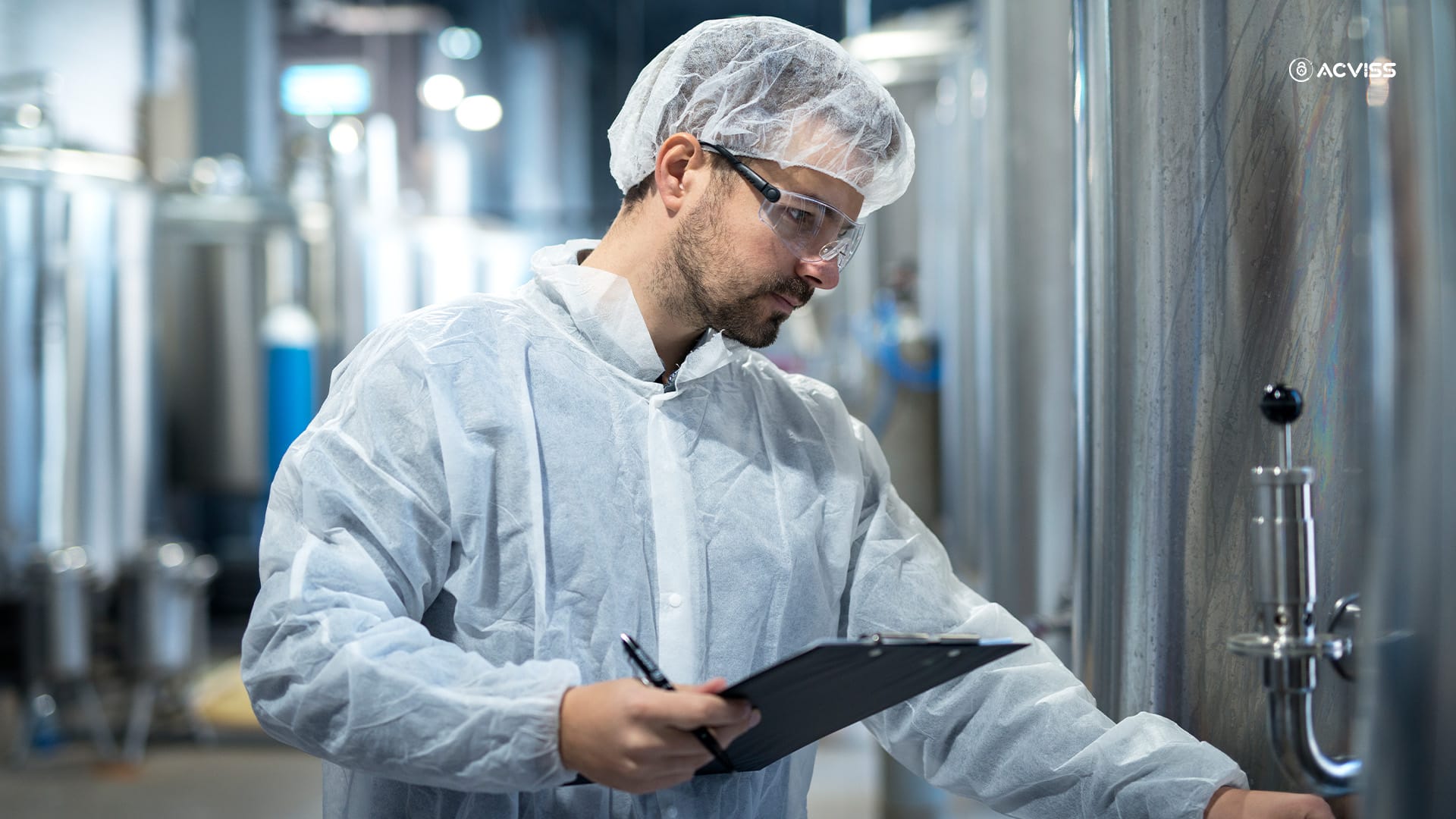
Historically, quality control relied on human inspectors. Today, computer vision systems and AI-based visual inspection can detect inconsistencies or defects at the micron level. For instance, BMW employs AI to validate every element of its car manufacturing process, ensuring flawless output.
4. Data Entry & Reporting
Manual logging of production data is slow and error-prone. Automation enables digital logbooks, automated data capture, and real-time dashboards, removing the need for repetitive entries while ensuring real-time traceability.
5. Inventory Management
Instead of manual stock checks, IoT-enabled inventory systems use sensors and RFID to track product movement, forecast shortages, and trigger reorders automatically, eliminating human oversight while reducing shrinkage.
6. Maintenance Scheduling
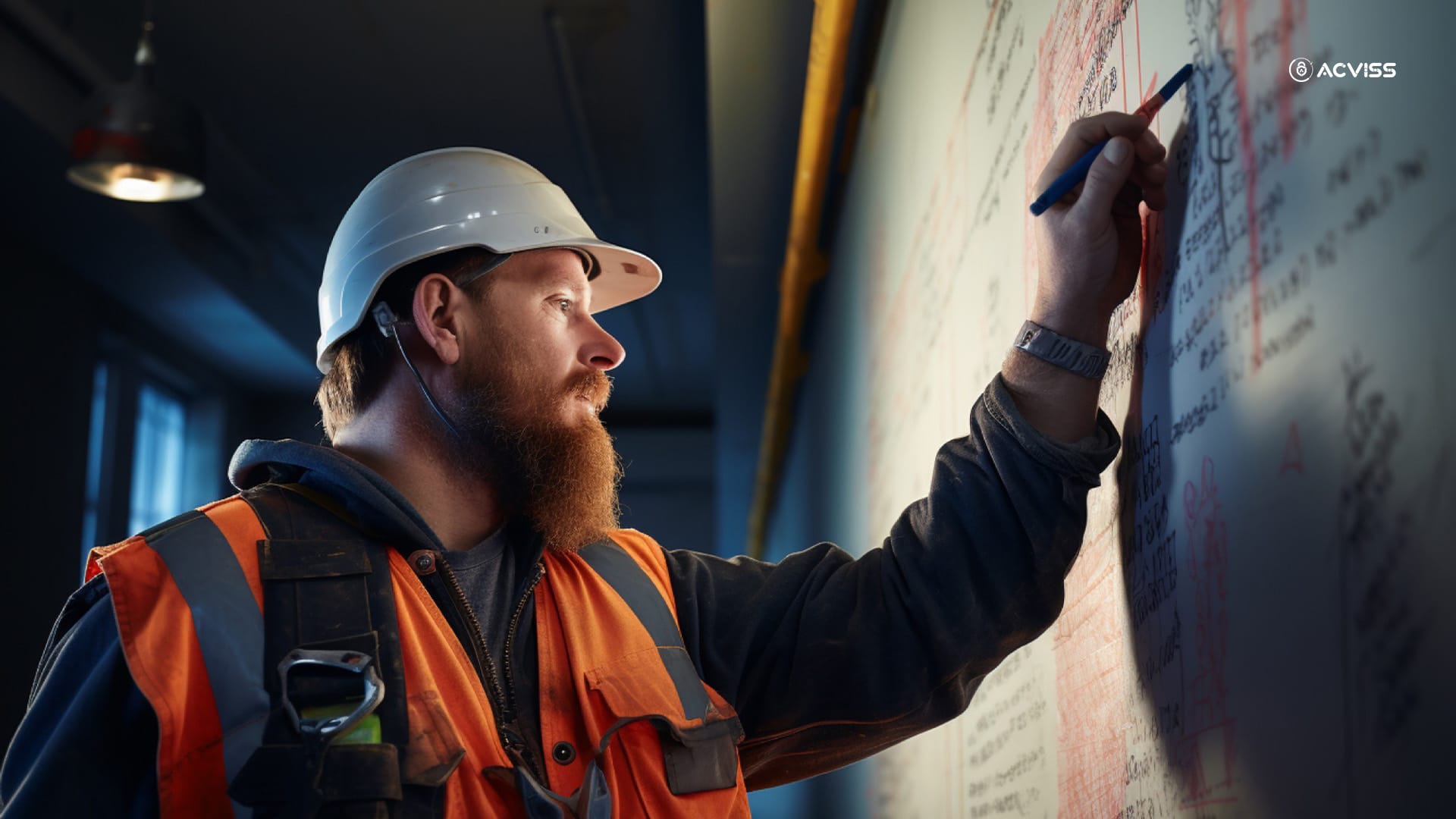
Rather than waiting for a machine to fail and calling for help, predictive maintenance systems use machine learning to analyse performance metrics and predict failures before they happen, saving time and reducing downtime.
7. Production Scheduling
Scheduling was once a manual balancing act on spreadsheets. Today’s Advanced Planning and Scheduling (APS) systems use AI to optimise schedules based on variables like order volume, machine availability, and material supply, even adapting in real-time to changes.
Technologies Powering Automation
A suite of technologies supports the shift from manual to automated systems in factories:
- Robotics and Cobots: For physical tasks like welding, painting, or moving components.
- PLC and Control Systems: The “brain” of automation, coordinating inputs and outputs.
- Machine Vision & AI: For inspection, defect detection, and quality assurance.
- IoT (Industrial Internet of Things): Sensors collect data across machines and processes.
- AR and Digital Twins: For training, simulation, and real-time factory replication.
- ML for Predictive Analytics: Used in quality, scheduling, and maintenance.
- Cloud Platforms & Edge Computing: To store and process data in real time.
- APS & ERP Systems: For planning, resource allocation, and integrated operations.
From Concept to Implementation: The Automation Journey
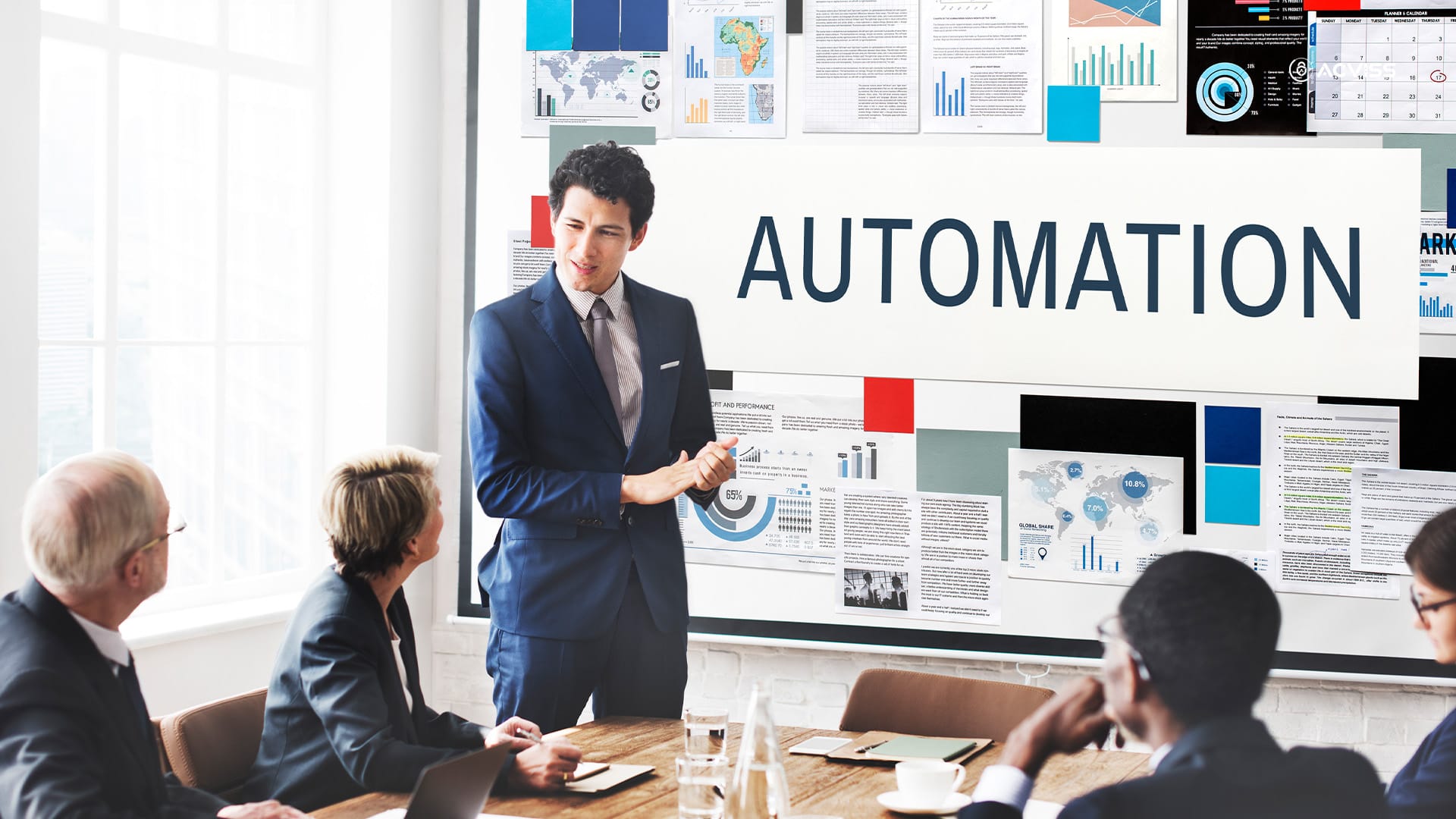
Automating a manual process isn’t a single-button upgrade; it’s a strategic journey that requires planning, investment, and change management.
Step 1: Identify Candidates for Automation
Not all processes merit automation. A critical assessment should be made:
- Is the process repetitive and high-volume?
- Is it prone to errors?
- Does it impact production timelines or safety?
The business technology (BT) team collaborates with process owners to identify inefficiencies and opportunities for digitisation.
Step 2: Define Automation Scope
Detail every step of the current manual process. Understand where human intervention is essential and where machines can take over. Define:
- Data flow requirements
- Notification and error handling protocols
- Integration with existing systems
Step 3: Develop & Test
Implement automation using chosen technologies. Pilot the setup in controlled environments and work closely with end users. Transparency, testing, and iteration are crucial during this phase.
Step 4: Deploy and Monitor
Once live, monitor the automation closely in its initial weeks. Track key performance indicators like error rate reduction, process time improvement, and user adoption. Adjust where necessary.
Step 5: Optimise
Continual refinement ensures the automation adapts as workflows evolve. Revisit the scope, collect feedback, and upgrade components as needed.
Types of Automation Systems: Tailored to Production Needs
Every factory has unique production dynamics, which is why multiple automation architectures exist:
- Fixed Automation: High initial investment, but ideal for mass production of standardised goods.
- Programmable Automation: Best for batch production with moderate flexibility.
- Flexible Automation: Allows for quick changeovers, suitable for high-mix, low-volume operations.
- Integrated Automation: A holistic system where every machine is digitally linked and centrally controlled.
For example, a pharmaceutical factory producing a single formulation may use fixed automation, whereas a packaging company serving multiple clients may rely on flexible automation to switch rapidly between orders.
The Real-World Payoff
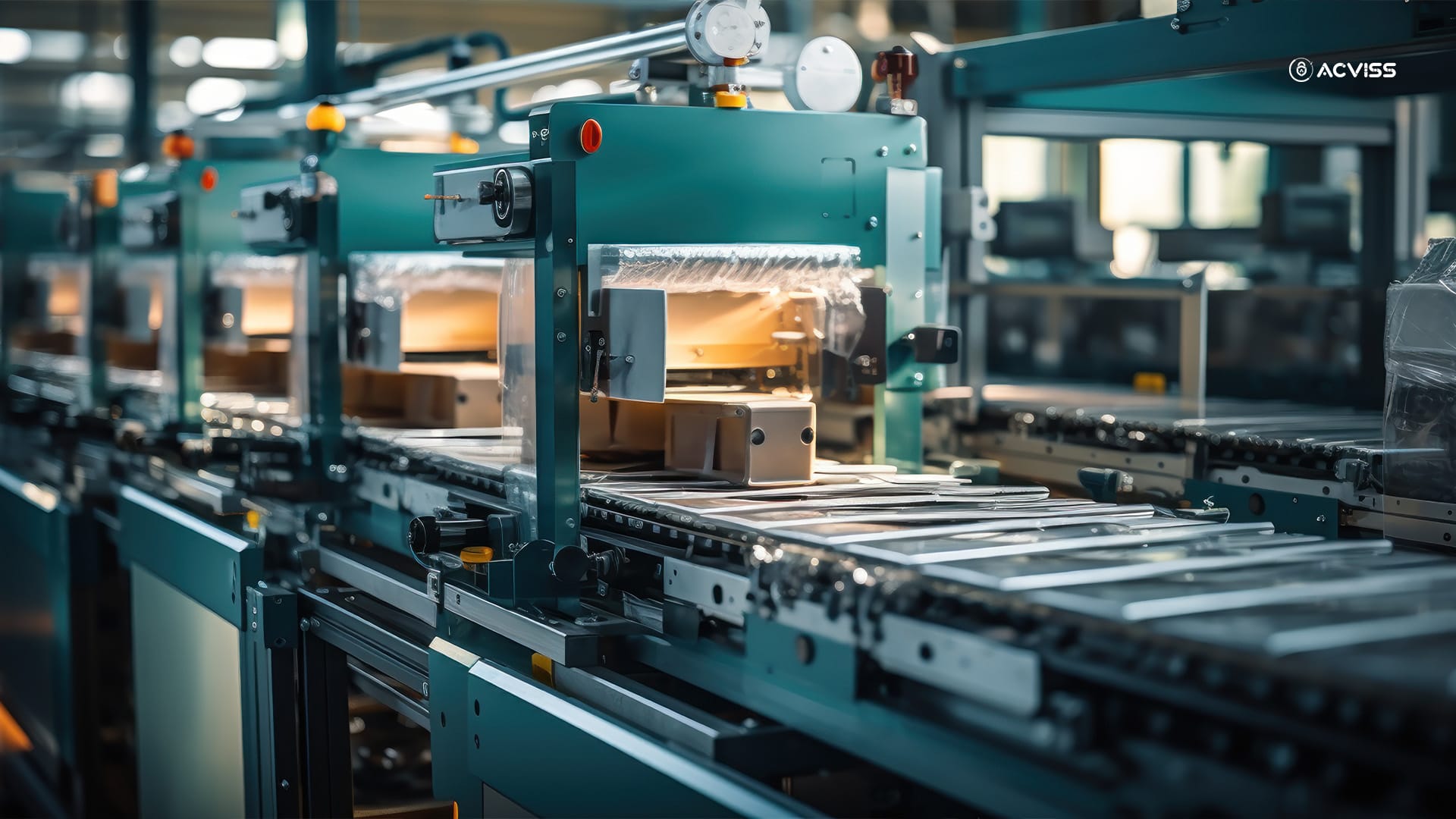
The benefits of factory automation go far beyond efficiency:
- Operational Visibility: Real-time data allows proactive management.
- Employee Upskilling: Workers move to supervisory or analytical roles.
- Sustainability Gains: Reduced waste and better energy utilisation.
- Compliance Made Easy: Automated documentation simplifies audits and quality checks.
- Customer Satisfaction: Faster, defect-free deliveries improve brand perception.
As manufacturers shift towards smart factories, automation becomes foundational, not just in production but in decision-making.
Overcoming Automation Challenges
Despite its promises, automation isn’t without hurdles:
- High Capital Investment: Equipment and integration can be costly.
- Workforce Resistance: Fear of job loss needs to be countered with reskilling and inclusion.
- Integration with Legacy Systems: Many older systems are not built for digital communication.
- Cybersecurity Risks: IIoT devices open new attack surfaces, requiring robust protection protocols.
A successful strategy addresses these head-on, combining technical implementation with cultural adaptation and robust cybersecurity practices.
Automation as a Catalyst for Transformation
Factory automation is not merely a technological shift; it’s a business transformation. When done right, it liberates human capital from monotonous tasks, enhances quality and compliance, and positions manufacturers to thrive in a rapidly evolving global market.
However, success doesn’t lie in the technology alone. It lies in the strategy behind its adoption. Organisations must align automation with their operational goals, involve stakeholders across levels, and foster a culture of continuous improvement.
Automation doesn’t mean replacing people; it means empowering them to focus on what humans do best: innovate, solve, and lead.
At Acviss, we understand the critical intersection between automation, traceability, and product authenticity. Our solutions are built to integrate with smart factories, providing non-cloneable digital labelling, AI-driven quality protection, and real-time insights. If you’re exploring automation to not just scale but secure your operations, reach out to us for a tailored solution that complements your transformation journey.