
Imagine a missing part that no one noticed, until it stops the entire production line. Or stacks of finished goods sitting untouched due to a simple labelling error. Meanwhile, the team scrambles to trace raw materials for a surprise compliance audit.
If you're in manufacturing, you know these issues are all too common. Many still rely on outdated methods, overlooking how these inefficiencies quietly drain profits.
In 2025, it's about keeping up with stricter regulations, sustainability goals, and rising customer expectations. Laws like EUDR and carbon reporting mean transparency is no longer optional; it's essential.
The cost of inefficiency isn’t just financial. It leads to:
- Wasted raw materials and energy,
- Lost production time due to unplanned downtime,
- Damaged brand trust when deliveries are delayed or compliance fails.
To put it in a cliche, operational efficiency is no longer a “nice to have”, it’s a must-have. Manufacturers today are turning to smart solutions that offer real-time visibility, data-driven insights, and automated processes to eliminate guesswork and plug revenue leaks.
In this blog, we’ll see the sources of factory inefficiency and show how digital tools, sustainability-first practices, and smart inventory tracking can help transform your operations from a cost centre into a competitive edge.
Before we get into this, let’s take a look at:
What is Operational Efficiency?
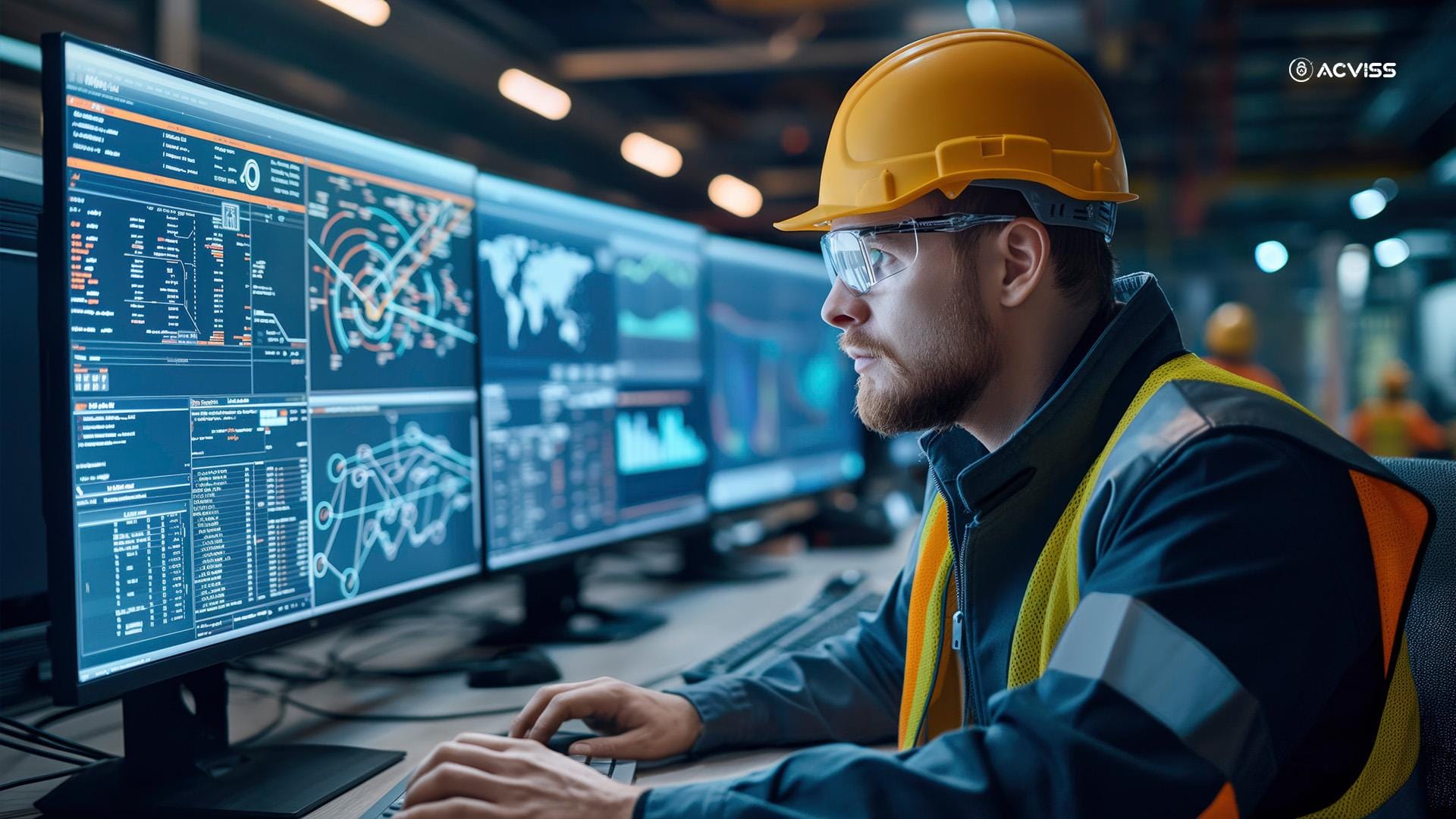
Operational efficiency in manufacturing refers to how well a factory converts inputs, like labour, raw materials, energy, and time, into outputs with minimal waste and maximum productivity.
It's the balance between output quality, resource utilisation, and cost-effectiveness.
The Operational Efficiency Formula
While the exact formula may vary across industries, a common one used is:
Operational Efficiency = (Output / Input) × 100 |
---|
But in factories, it's often measured more precisely using ratios and metrics that account for production output, downtime, and resource consumption.
Key Metrics That Define Operational Efficiency
- Efficiency Ratio
Measures output per unit of input (e.g., units produced per labour hour). - Cycle Time
Time taken to complete one unit of production, from start to finish. - Overall Equipment Effectiveness (OEE)
Combining availability, performance, and quality. A high OEE means machines are running efficiently with minimal downtime and defects. - First Pass Yield (FPY)
Measures how many products are manufactured correctly the first time without rework. - Inventory Turnover
How fast inventory is sold and replaced, a sluggish turnover hints at overproduction or demand mismatch.
Example
Imagine a beverage factory that makes 10,000 bottles a day.
But every day, it loses:
- 2 hours due to sudden machine breakdowns
- And has to discard 500 bottles because of quality issues
That’s a lot of time, money, and materials going to waste.
Now, the factory installs real-time monitoring tools and predictive maintenance systems. What happens?
- Downtime drops by 80%
- Defective bottles reduced by 50%
The result?
More bottles produced. Less waste. Lower costs. That’s operational efficiency in action.
So we understood what operational efficiency is, now let's…
Understanding Operational Inefficiencies in Manufacturing
Operational inefficiency in a factory is like a slow leak in a pipe. It’s unseen at first, but over time, it drains resources, increases costs, and cripples margins.
Put simply, operational inefficiency refers to the failure to fully optimise resources, whether it’s time, labour, inventory, machinery, or data. In today’s competitive and regulated environment, even minor inefficiencies can snowball into major setbacks.
Here are some hidden drains that hurt factory performance:
- Material Waste
Excess raw materials, production scrap, and defective outputs often go unnoticed but account for a significant cost over time. - Idle or Excess Inventory
Overstocking leads to storage costs, expiry risks, and working capital lock-up, while understocking disrupts production. - Lack of Visibility
When data is not centralised or real-time, production planning becomes guesswork. This leads to delays, miscommunication, and inefficiencies across departments.
Wondering what happens due to this?
The True Cost of Factory Floor Inefficiencies
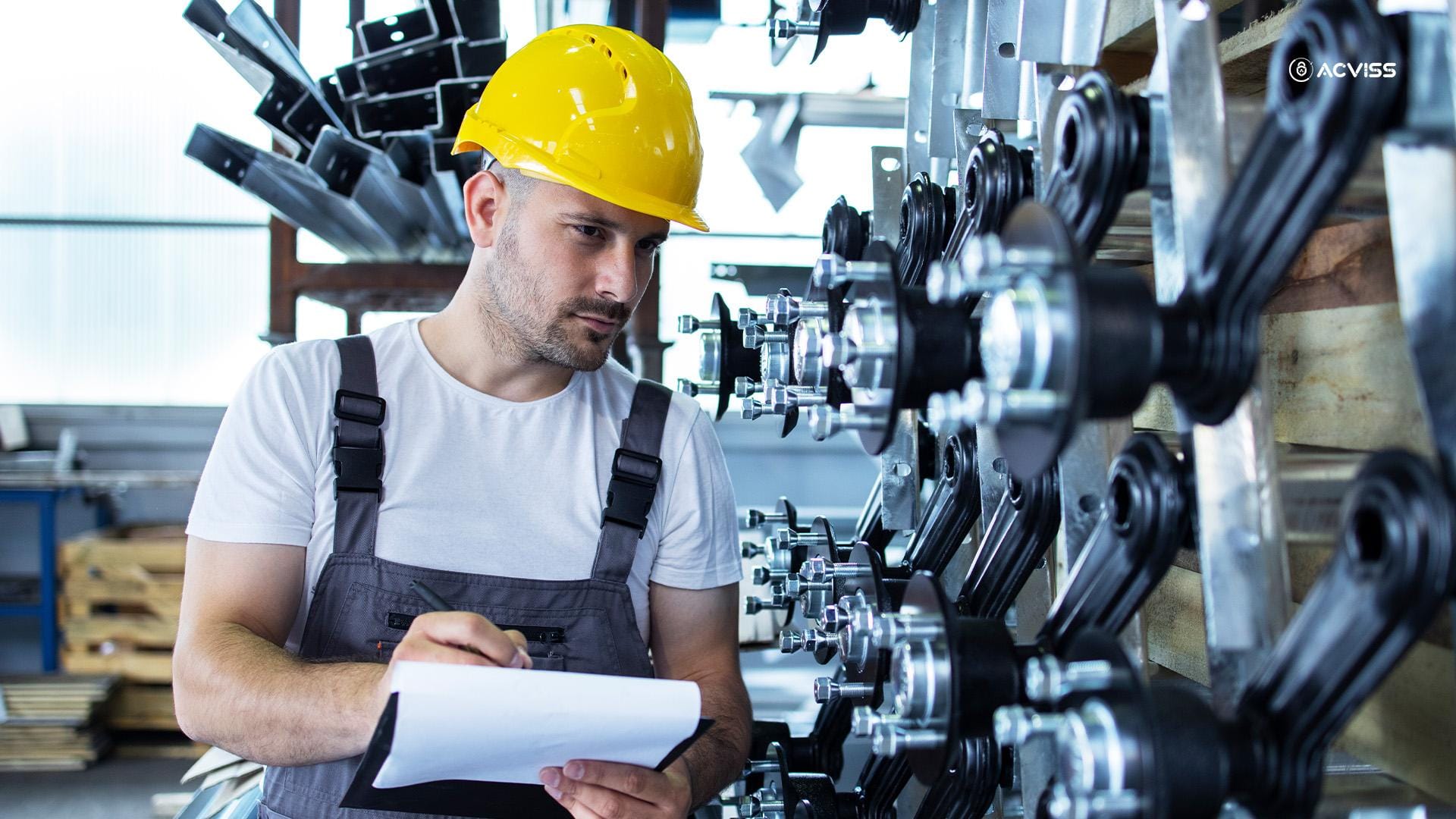
- Downtime and Equipment Failures
Unplanned stoppages due to poor maintenance or delayed intervention disrupt the entire supply chain. - Rework and Quality Issues
Faulty products demand reprocessing or scrapping, driving up production costs and affecting brand reputation. - Human Errors and Manual Bottlenecks
Manual logging, disconnected systems, or untrained staff contribute to slowdowns and costly mistakes. - Compliance and Documentation Errors
Incomplete logs or non-compliance with quality/safety standards can result in fines, recalls, or import/export bans.
Environmental and Regulatory Risks
Factories that ignore inefficiency often end up violating sustainability mandates through excess emissions, packaging waste, or improper disposal of materials. This leads to EPR penalties, lost certifications, or worse, public backlash.
Bottom line?
Operational inefficiency is a technical problem as well as a strategic threat to profitability, compliance, and brand value. Smart factories are tackling this head-on with real-time monitoring, automated alerts, and predictive insights.
Factors Influencing Operational Inefficiencies in Manufacturing
Operational inefficiencies rarely stem from a single cause. They’re usually the result of interconnected problems across people, processes, and systems. To fix the leaks, manufacturers need to first understand where and why they’re happening.
1. Siloed Departments and Fragmented Data
When production, procurement, quality control, and logistics don’t share real-time data, you get bottlenecks. One team over-orders, another misses a deadline, and no one has a clear picture of inventory or output.
Impact:
- Delayed decisions
- Duplicate efforts
- Inventory mismatches
2. Outdated Systems or Manual Processes
Paper-based logs, spreadsheets, and legacy software slow everything down. Manual entries are prone to errors, hard to track, and nearly impossible to scale with growing demand.
Impact:
- Higher error rates
- Inaccurate reporting
- Sluggish workflows
3. Lack of Predictive Maintenance
Many factories still rely on reactive maintenance, waiting until machines break down before acting. This leads to unplanned downtime, costly repairs, and lost production.
Impact:
- Increased machine downtime
- Missed production targets
- Safety risks
4. Untrained Workforce and Poor Collaboration
Even the best tech fails without the right people using it. Poor training, high attrition, and lack of cross-functional communication weaken execution on the ground.
Impact:
- Lower productivity
- Higher error rates
- Reduced morale
5. Supply Chain Disruptions and Compliance Burdens
Global supply chains are under constant strain, from raw material shortages to shifting regulations. Manufacturers must now track everything from sourcing origins to carbon footprints.
Impact:
- Delayed sourcing and deliveries
- Penalties for non-compliance
- Increased operational costs
So, we talked about the problem. Now, let’s talk about the solution – Lean Manufacturing
Factory Waste Management: First Step Towards Lean Manufacturing
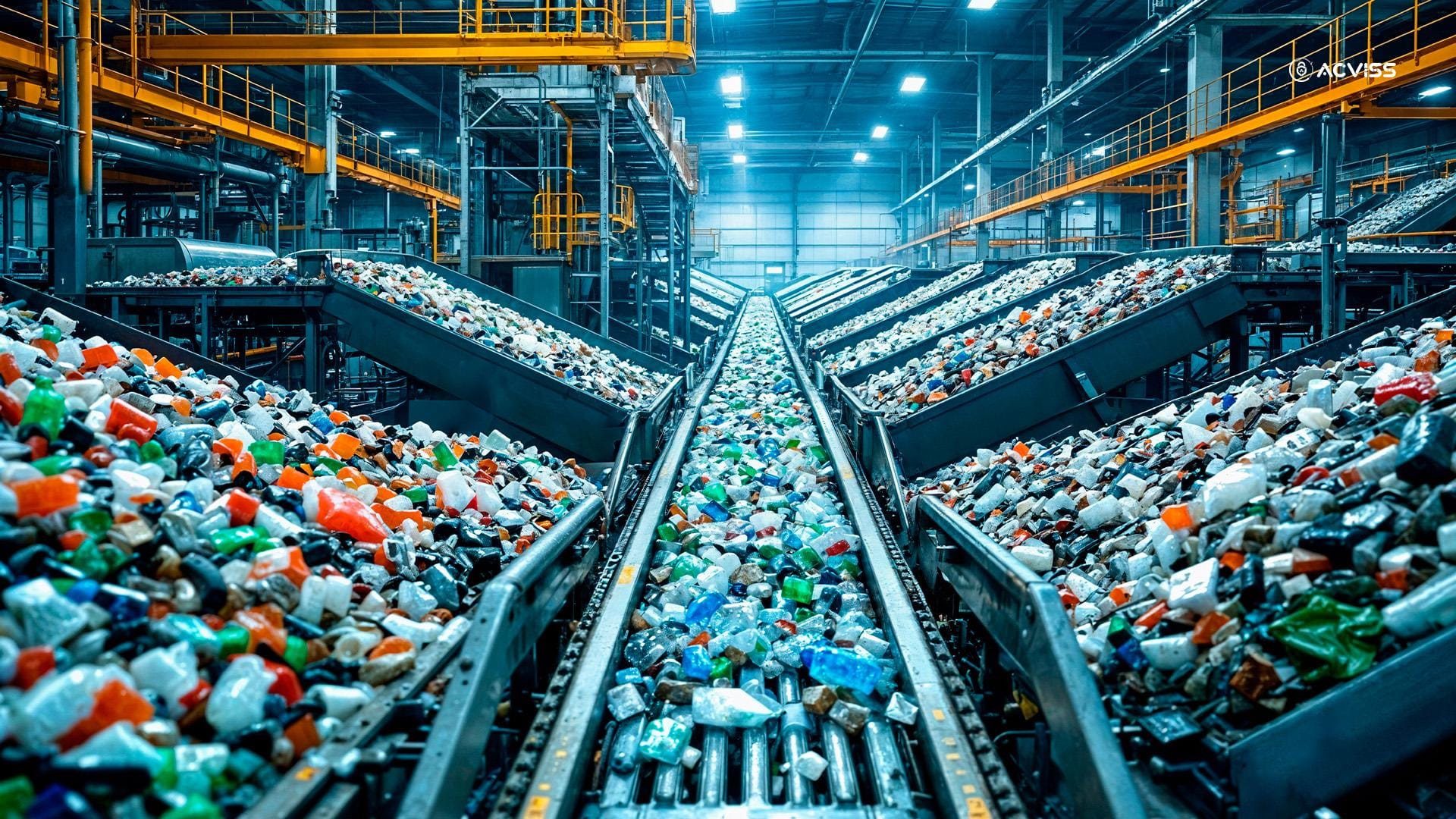
In manufacturing, waste isn’t just about physical scrap; it’s anything that doesn’t add value. Wasted materials, wasted time, wasted energy, all of it eats into your margins, slows down output, and weakens your competitive edge.
Smart waste management is the foundation of lean operations and a must-have for factories in 2025.
What Qualifies as “Waste” in a Factory?
Lean manufacturing defines waste (muda) broadly. It includes:
- Material waste: Excess raw materials, product defects, and off-cuts
- Time waste: Idle machinery, downtime between shifts, inefficient workflows
- Energy waste: Overheating, lighting unused areas, running idle equipment
- Human effort waste: Redundant steps, underutilised skills, manual rework
Common Examples You’re Probably Ignoring
- Overstocking due to poor inventory visibility
- Scrap and rejects from inconsistent production
- Returns and product recalls due to quality or compliance errors
- Excess movement of materials or people (motion waste)
- Underused equipment or production lines
These leaks often go unnoticed until they show up in your monthly loss reports.
How to Audit and Measure Waste Effectively
A robust waste management strategy starts with visibility:
- Conduct a waste audit across materials, time, and energy
- Track production rejects and reasons (e.g. rework, off-spec)
- Map workflow inefficiencies with time-motion studies
- Use KPIs like scrap rate, first-pass yield (FPY), and energy consumption per unit
Regular audits not only highlight where waste occurs, but they also help prioritise what to fix first.
The Role of Tech: Real-Time Waste Monitoring and Reduction
Modern waste reduction isn’t about clipboards, it’s about live dashboards and automated alerts.
Smart factories are using:
- IoT sensors to detect machine anomalies before they lead to scrap
- AI analytics to flag patterns in product defects or energy overuse
- Track and trace tools to identify where in the supply chain waste originates
- Digital twins to simulate workflow improvements before implementing them
When waste is visible in real-time, action becomes instant, and that’s where the savings begin.
Bottom line:
Reducing factory waste is essential for sustainability, compliance, and operational agility. And tech makes it not just possible, but scalable.
Manufacturing Cost Reduction Strategies That Actually Work
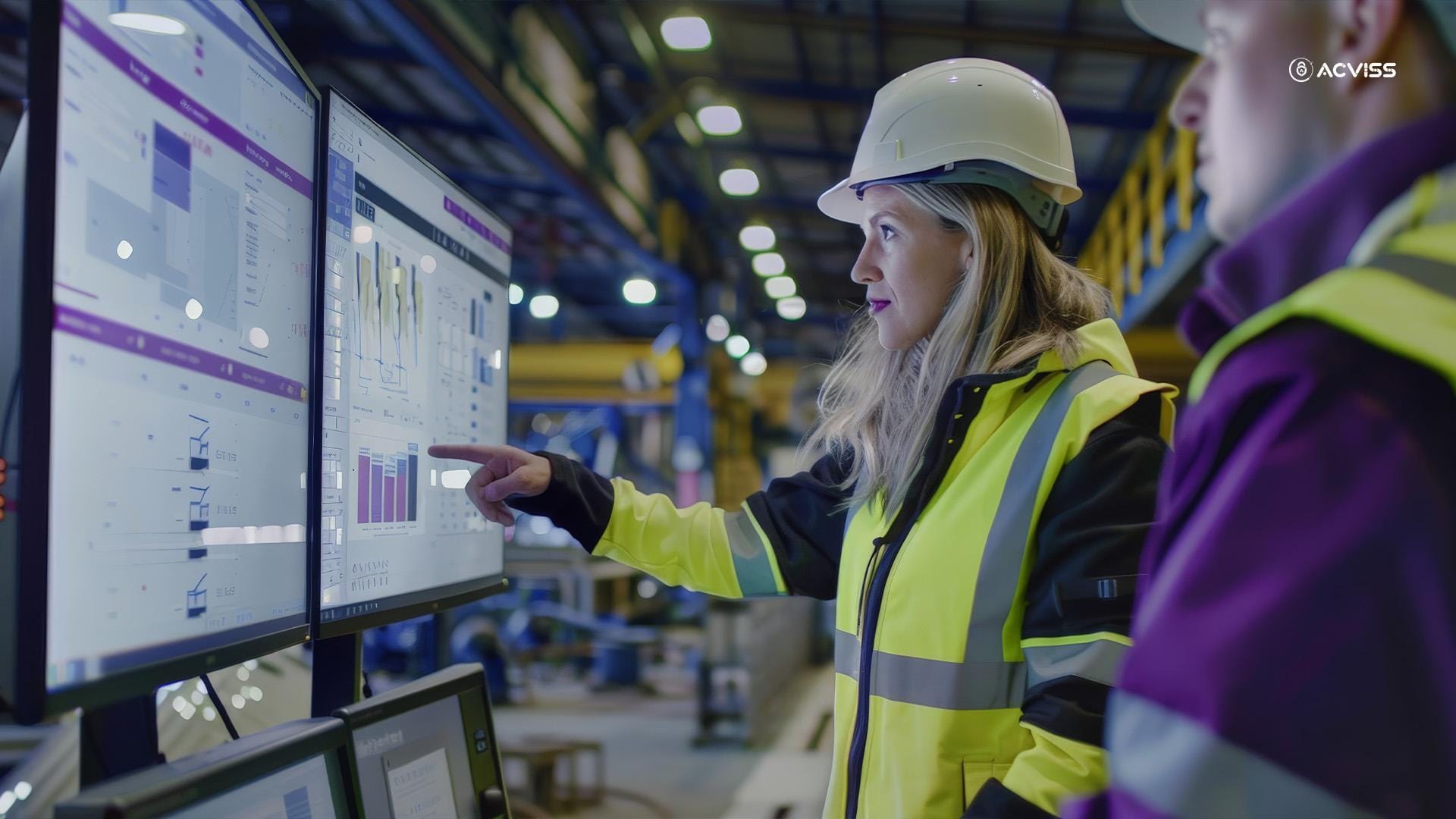
Well, isn’t this a topic that brings sparkle to every business owner’s eyes? xD
Here’s how it works in the Lean Manufacturing technique
Cost-cutting in manufacturing often starts with layoffs or cheaper inputs, but that’s a short-term fix.
The smarter way? Optimise what you already have. By combining smart processes with the right tech, manufacturers in 2025 are slashing costs without sacrificing quality or output.
Just-in-Time vs. Smart Inventory Management
Just-in-Time (JIT) production was once the gold standard, but it's vulnerable to disruptions.
Enter smart inventory management:
- Uses real-time inventory tracking to balance supply and demand
- Flags overstocking and understocking before they hit your balance sheet
- Integrates with ERP systems for automated reorder triggers
With live visibility into stock movement, you reduce holding costs, free up space, and prevent dead inventory from clogging your cash flow.
Track and Trace: Prevent Overproduction and Counterfeiting
Producing more than you need? That’s not efficiency, that’s risk.
Track and trace systems help by:
- Aligning production with actual demand data
- Detecting diversion or counterfeiting, so you don’t lose product or brand trust
- Ensuring compliance with labelling and serialisation laws
By pinpointing inefficiencies in your supply chain, you avoid duplication and fraud, two silent cost killers.
Predictive Maintenance = Less Downtime, Fewer Losses
Reactive maintenance is expensive and disruptive. Predictive maintenance, powered by IoT and machine learning, monitors equipment health in real-time.
Benefits:
- Alerts you before breakdowns happen
- Reduces emergency repair costs and spare part wastage
- Extends equipment life and boosts uptime
More uptime = more production = more revenue. It’s that simple.
Packaging and Raw Material Optimisation
Sometimes, the savings are hiding in the little things, like your packaging.
- Switch to lightweight or recyclable materials to cut costs and stay sustainable
- Redesign packaging to minimise space (and reduce shipping cost)
- Track raw material usage in real-time to prevent overuse and pilferage
Even minor improvements here can compound across thousands of units.
Bottom line:
Cost reduction in 2025 is only possible with data, automation, and lean thinking. You’ll not only save money, but improve quality, compliance, and speed.
Sustainable Manufacturing Practices for Long-Term Margin Growth
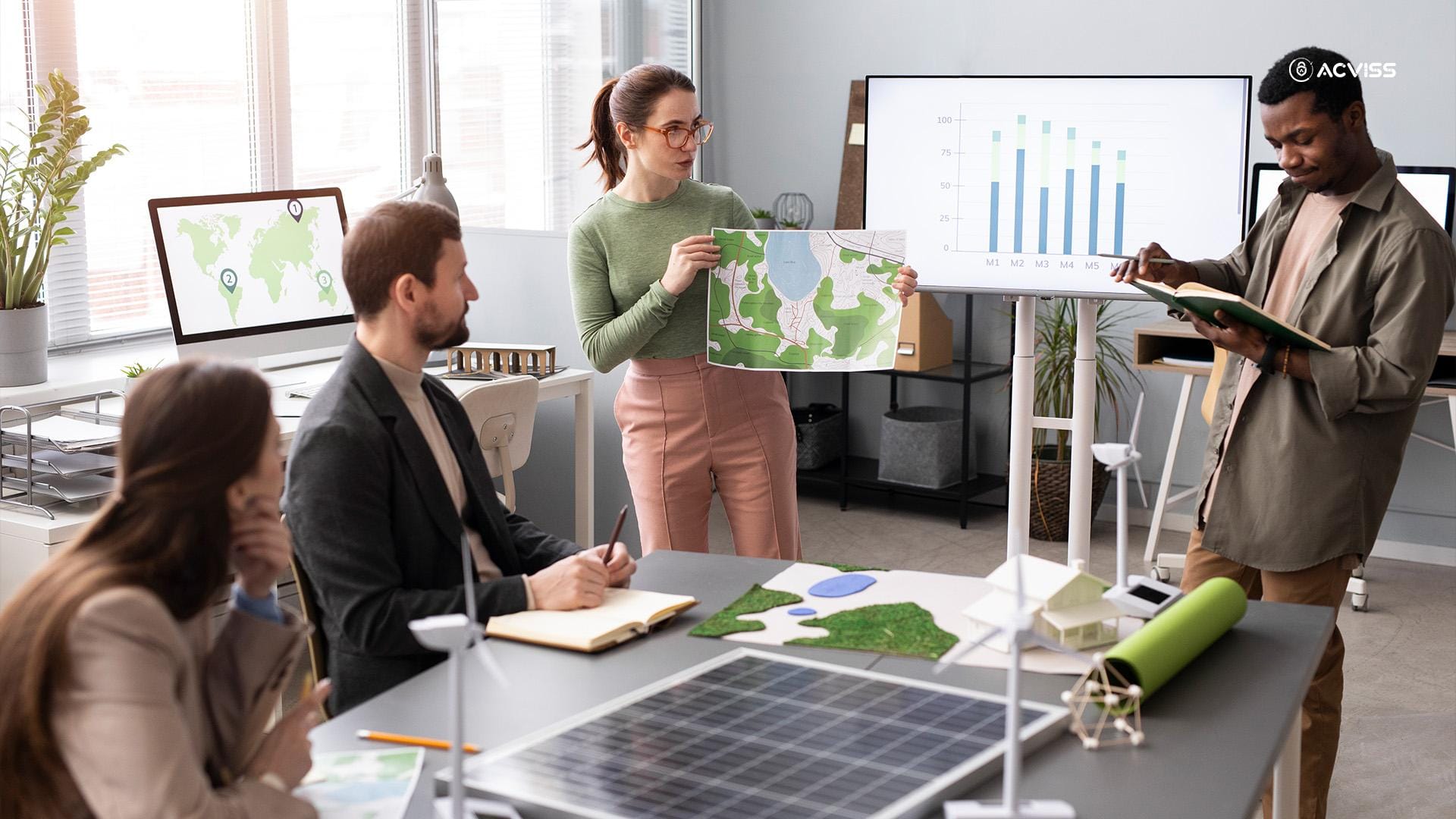
In the modern era of business, sustainability isn’t just about saving the planet; it’s about saving money, reducing risk, and building trust. In 2025, green manufacturing is lean manufacturing. The right environmental practices don’t cut into your margins; they protect and grow them.
Green = Lean: How Sustainability Improves Margins
Sustainability drives resource efficiency, which directly affects the bottom line:
- Less waste means lower disposal and raw material costs
- Efficient processes = reduced energy and water bills
- Eco-compliant factories avoid regulatory fines and delays
Sustainability is no longer a cost centre; it’s a strategic business lever.
Energy-Efficient Processes and Waste-to-Value Initiatives
Smart factories are using tech to monitor and minimise energy usage across operations:
- IoT sensors detect energy leaks and usage spikes in real-time
- Process automation helps reduce idle time and unnecessary consumption
- Waste-to-value projects convert scrap, by-products, or heat into reusable inputs
Example: A food processing unit repurposing organic waste into biogas can cut energy costs and reduce carbon emissions.
Compliance with EPR, RoHS, ISO 14001, and More
Environmental regulations are tightening globally. Key mandates include:
- EPR (Extended Producer Responsibility): Ensures manufacturers manage post-consumer waste like packaging and electronics
- RoHS (Restriction of Hazardous Substances): Controls the use of toxic materials in electronics
- ISO 14001: International standard for environmental management systems
Non-compliance can mean penalties, bans, or reputational damage, especially in export markets.
The Business Case for Eco-Compliance: Brand Trust + ROI
Today’s consumers and B2B buyers care where their products come from.
Sustainable practices:
- Increase brand loyalty and perceived value
- Open access to ESG-friendly markets and investors
- Help win government contracts and green certifications
- Attract and retain top talent who want to work for mission-driven brands
It’s not just good PR, it’s good business.
Takeaway:
Sustainable manufacturing is a strategic choice. It offers a strong RoI, stronger margins, and a stronger position in the global marketplace.
Inventory Tracking and Supply Chain Traceability: The Core of Smart Manufacturing
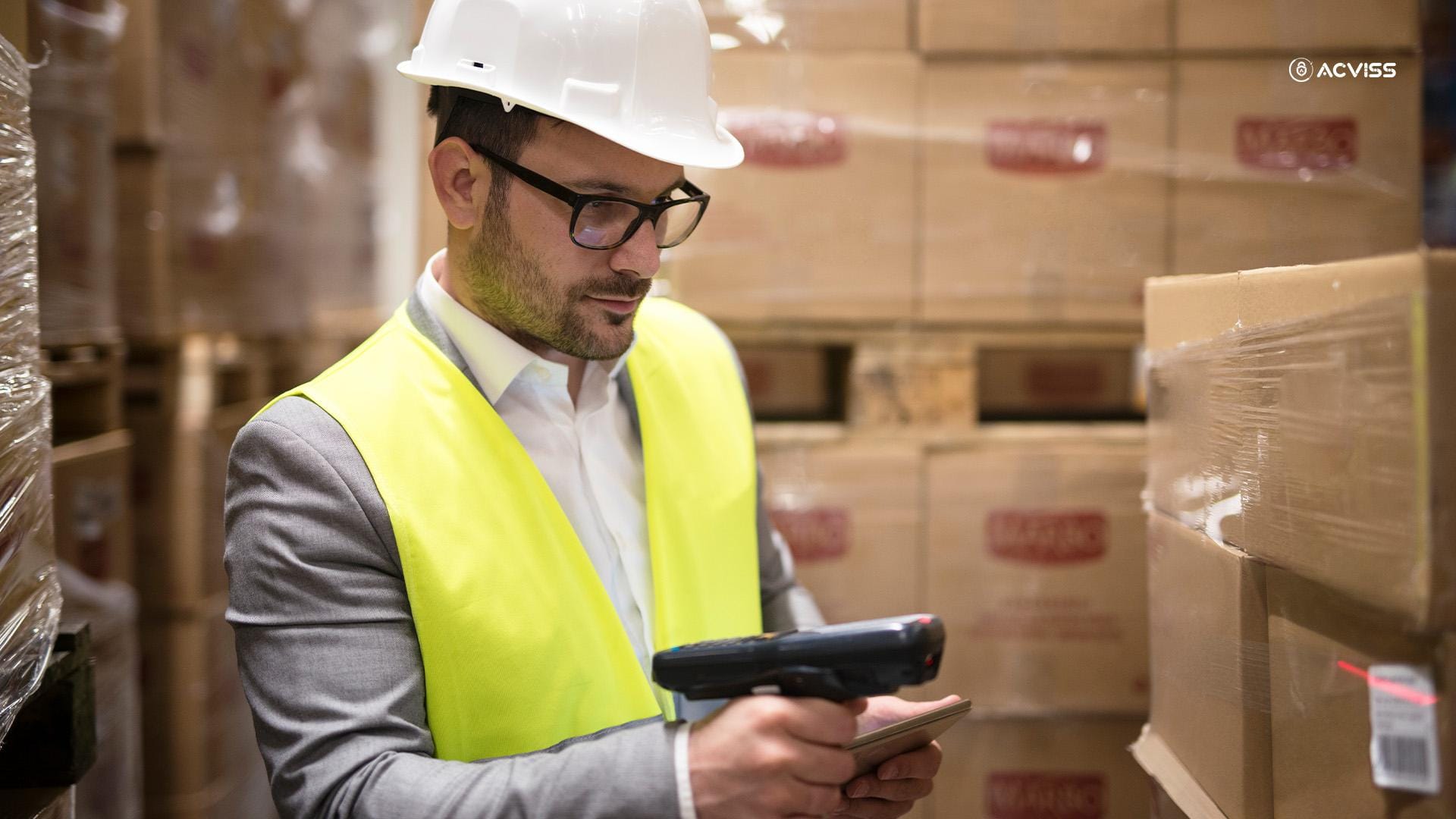
Inventory is where profits are made, or lost. And in 2025, spreadsheets, siloed ERPs, and manual reconciliations just don’t cut it. Manufacturers today need real-time visibility, not just data collection. That’s where traceability and smart tracking come in.
Why Spreadsheets and ERPs Alone Aren’t Enough
Traditional tools are reactive. They show what went wrong after it happens:
- Delayed updates create blind spots
- Inventory mismatches cause stockouts or overproduction
- Manual processes increase the chance of human error
Even the best ERPs lack granular, real-time traceability across production, warehousing, and distribution unless integrated with modern tools.
Real-Time Traceability = Faster Disruption Response
When disruptions hit, whether it’s a supplier delay or a product recall, real-time tracking can be the difference between quick containment and a supply chain crisis:
- Instantly identify affected batches or suppliers
- Isolate risks before they spread
- Comply with traceability audits from regulators or partners
With track and trace, businesses act in minutes, not days.
Benefits: Cost Savings, Compliance, and Forecasting
Real-time inventory tracking and traceability offer multiple payoffs:
- Reduce holding costs with accurate stock levels
- Prevent overproduction and understocking
- Meet export, pharma, or food safety regulations (like EUDR or FSSAI)
- Improve demand forecasting through historical and live data
This isn’t just about efficiency. It’s about competitive survival.
Smart Integration with ERP, MES, and SCM Systems
Modern traceability solutions don’t replace your existing platforms; they enhance them:
- Syncs with ERP for financial and planning visibility
- Links to MES (Manufacturing Execution Systems) for shop floor operations
- Aligns with SCM tools for end-to-end supply coordination
With seamless integration, you get a single source of truth, updated in real time, across your factory and beyond.
Production Downtime Reduction with Smart Tech
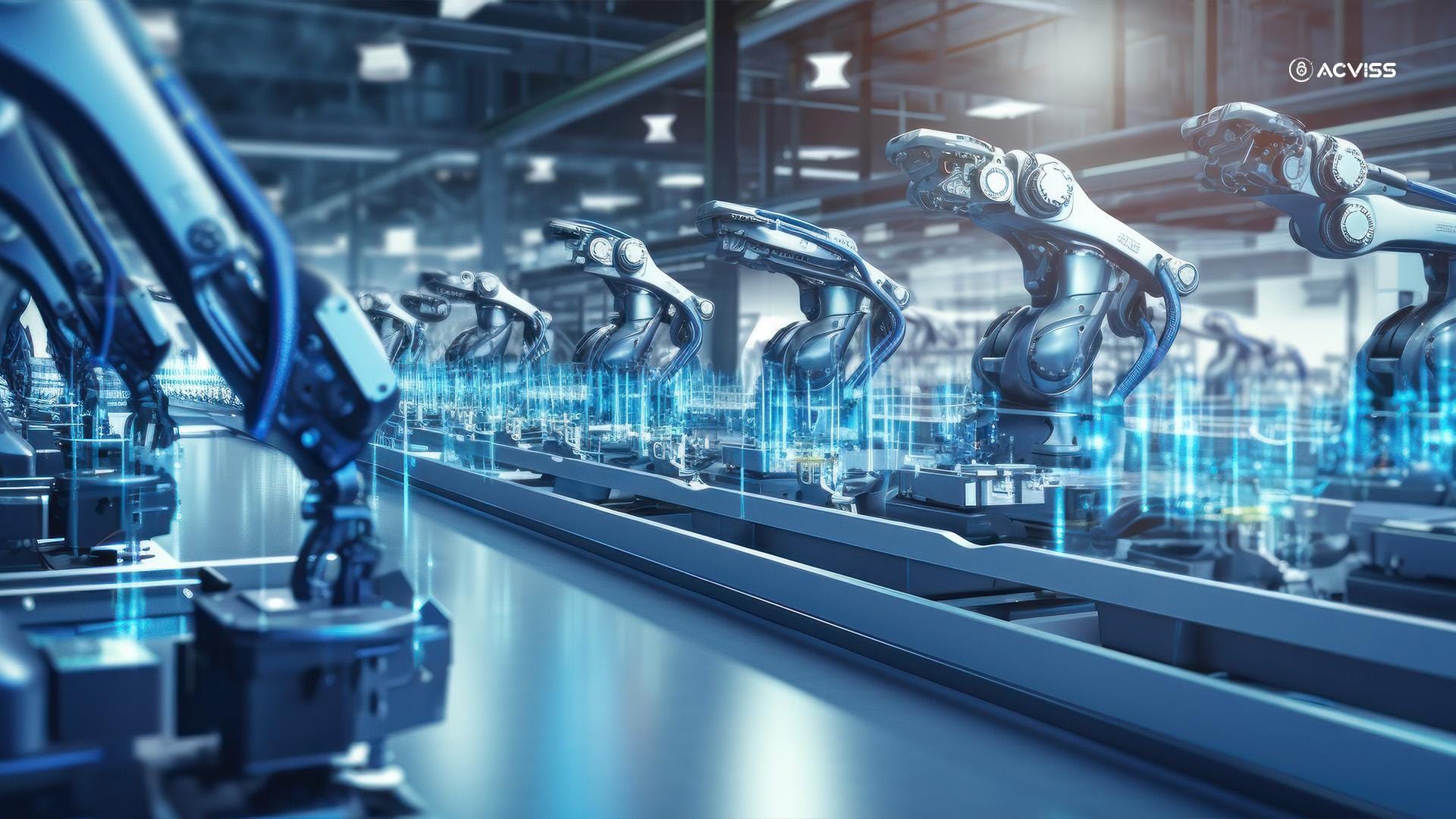
Downtime is the silent profit killer on factory floors. Every minute machines stand idle, costs pile up, delivery deadlines slip, and customer trust wanes. In 2025, understanding why downtime happens and how to prevent it is essential for manufacturers aiming to stay competitive.
Common Causes of Downtime
- Unplanned maintenance: Equipment failures catch teams off guard
- Miscommunication: Lack of real-time updates delays repairs or adjustments
- Breakdowns: Ageing machinery and wear and tear increase the risk
- Workflow bottlenecks: Inefficient processes cause stoppages
Without the right tools, many of these issues snowball into costly production halts.
How AI, IoT Sensors, and Digital Logs Preempt Failure
Smart factories leverage emerging technologies to stay ahead of downtime:
- IoT sensors continuously monitor equipment health (temperature, vibration, runtime)
- AI algorithms analyse sensor data to predict when a machine might fail
- Digital logs provide detailed maintenance history and workflow records
This creates a proactive environment where failures are spotted before they happen.
Proactive Alerts, Machine Tracking, and Workflow Optimisation
Smart tech does more than just detect problems:
- Sends instant alerts to maintenance teams for quick action
- Tracks machine utilisation to avoid overuse or underuse
- Optimises workflows by identifying bottlenecks or inefficient steps
The result? Faster repairs, less unplanned downtime, and smoother production runs.\
⭐Takeaway: |
---|
How Acviss Enables Smart Manufacturing & Compliance
Acviss offers a comprehensive smart manufacturing platform designed to tackle inefficiencies and boost compliance from start to finish.
Real-Time Traceability and Digital Product Verification
Acviss provides real-time traceability across your supply chain, which lets you track every product and component digitally, from raw material to finished goods. This digital verification ensures authenticity and quality at every stage.
Source-to-Shelf Inventory Tracking
Acviss enables source-to-shelf tracking, giving you precise, up-to-the-minute insights into stock levels, movements, and usage. This visibility helps reduce overstocking, minimise waste, and optimise procurement decisions.
Reduces Waste, Counterfeiting, and Downtime
By integrating advanced analytics and smart tracking, Acviss empowers manufacturers to:
- Cut down waste through better resource monitoring
- Prevent counterfeiting with secure product verification
- Decrease downtime by enabling predictive maintenance and faster issue resolution
Seamless Integration with ERP and Factory Systems
Acviss is designed to work with your existing infrastructure. It integrates smoothly with ERP, MES, and other factory management systems, ensuring that data flows seamlessly across platforms without disrupting your workflows.
⭐ Bottom line: |
---|
Conclusion
In 2025, operational efficiency is a survival strategy. Factories that fail to optimise waste management, reduce costs, and boost margins risk falling behind in a fiercely competitive, sustainability-driven market.
To truly future-proof your factory and turn operational efficiency into a competitive advantage, you need technology that delivers real-time insights, traceability, and actionable control. That’s exactly where Acviss comes in.
Ready to transform your factory floor? Leverage Acviss’s smart manufacturing solutions to reduce waste, enhance compliance, and maximise your margins today.